Precision and efficiency define the modern manufacturing landscape, and the evolution of tools like the square pipe cutting machine is a testament to this drive for excellence. These machines, essential in industries ranging from construction to automotive manufacturing, embody a blend of cutting-edge technology and practical application, ensuring materials are shaped with both accuracy and speed. As experts in the field can attest, incorporating these devices into production lines dramatically enhances output quality and operational efficiency.
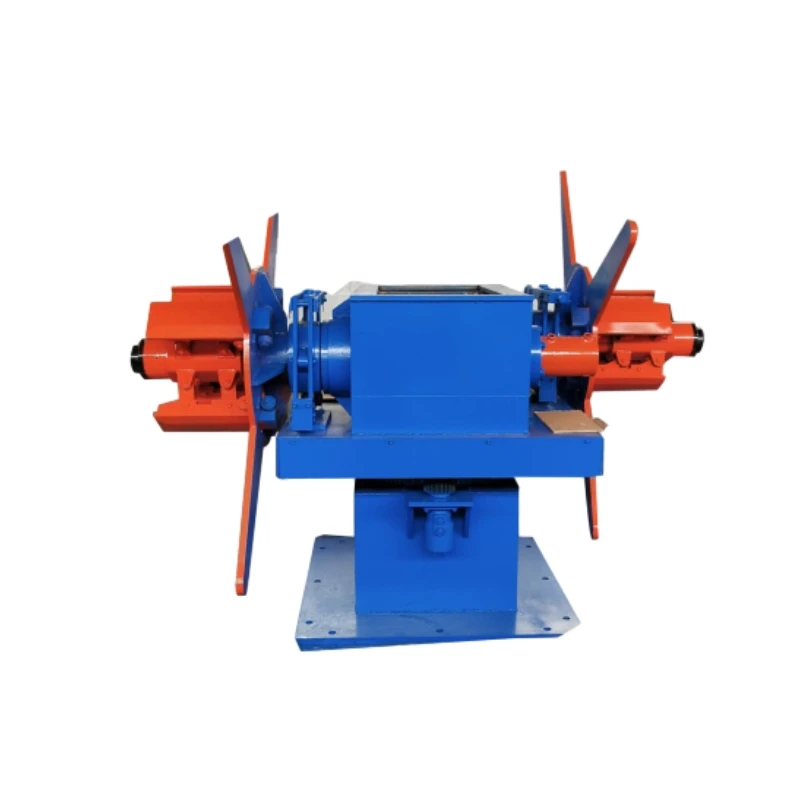
The square pipe cutting machine is designed for the precise cutting of metal pipes with a square cross-section. Its primary advantage lies in its ability to deliver clean cuts, which significantly reduces the need for additional finishing processes. This precision is achieved through advanced controls and cutting technologies, such as automated feeds and computer numerical control (CNC) systems, which enable users to achieve consistency across multiple units without compromising on speed or accuracy.
In hands-on industry applications, the machine’s capacity for handling diverse materials — from steel and aluminum to copper — underscores its versatility. Operators often highlight the ease with which these machines can be adjusted for varying pipe thicknesses, alongside their capability to execute complex cutting patterns that meet bespoke fabrication requirements. Furthermore, built-in safety features, such as automatic shut-off sensors and protective guards, ensure that operational safety is never compromised, a crucial factor in maintaining workforce safety and workflow integrity.
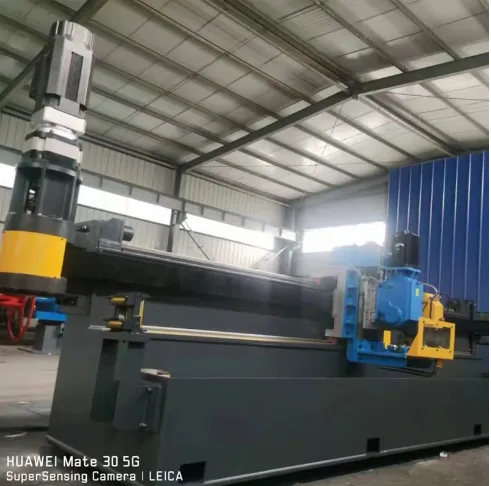
From a technical standpoint, expertise with square pipe cutting machines requires a detailed understanding of different blade types and their application. The choice between abrasive blades for harder metals and toothed blades for softer materials can drastically affect the quality of the cut and the machine's performance. Operators with substantial experience in machine settings can outperform others by optimizing blade speed, feed rate, and minimizing downtime during bit or blade changes, showcasing an appreciable level of expertise.
square pipe cutting machine
The integration of these machines also speaks to an authoritative grasp of industry standards. Manufacturers and workshop managers who regularly employ square pipe cutting machines often report on the significant reduction in material waste. This not only aligns with ecological standards and sustainability goals but also confers a competitive edge by lowering production costs. By implementing precision cutting technology, firms can confidently claim compliance with both local and international production standards, further cementing their authority in the marketplace.
Trust in these machines is often reflected in their robust design and the warranties provided by leading manufacturers. Long-term users frequently cite the heavy-duty nature of the construction, which promises durability and reliability even under consistent high-volume use. Moreover, companies that invest in regular training sessions for their operators on the latest machine updates and maintenance tips tend to experience fewer breakdowns, suggesting a direct correlation between operator knowledge and machine trustworthiness.
Selecting the right square pipe cutting machine also requires a nuanced understanding of available features and customizable options. Many reputable suppliers offer machines with easy-to-use interfaces that simplify the process of inputting measurements and selecting cutting styles. Wireless connectivity in advanced models allows for seamless software updates, ensuring users always have access to the latest technological advancements. Additionally, some brands offer tailored machine configurations to address specific industrial challenges, enabling users to select features that best align with their operational needs.
To conclude, the square pipe cutting machine represents more than just a tool; it is a pivotal asset in the pursuit of manufacturing excellence. Its precision, adaptability, and reliability highlight why it is favored by experts seeking to maintain competitive advantage in fast-paced production environments. When properly integrated and maintained, these machines offer unrivaled opportunities to enhance both the quality and efficiency of metalworking processes, establishing an irreplaceable role in modern industry operations.