Metal roll formers are indispensable machines in the sheet metal fabrication industry. These machines are designed to shape metal sheets into various profiles and forms through a continuous rolling process. The demand for these machines, including roll formers for sale, has grown significantly due to their efficiency, precision, and versatility. This article provides insights into metal roll formers, their applications, and their benefits for industrial use.
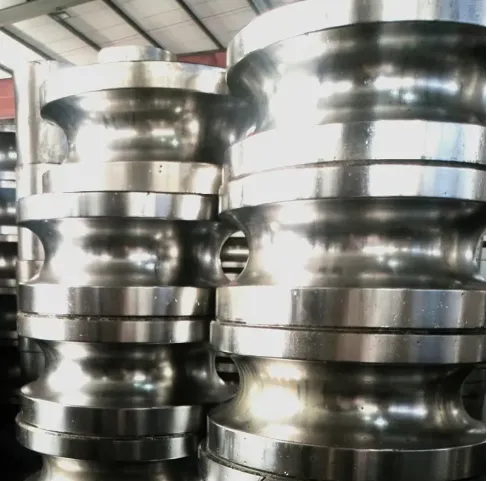
What is a Metal Roll Former?
A metal roll former is a machine used in the metalworking industry to bend and shape metal sheets into desired profiles. Unlike traditional forming methods, roll formers utilize multiple sets of rollers to gradually shape the material. This process ensures consistency and high-quality results, making them essential for producing parts like roofing sheets, door frames, and structural beams.
Types of Metal Roll Formers
Single-Sided Roll Formers
- Suitable for straightforward profiles like U-channels or C-sections.
Double-Sided Roll Formers
- Allows production of different profiles using the same machine, enhancing versatility.
Portable Roll Formers
- Compact and easy to transport, ideal for on-site operations.
Custom Roll Formers
- Designed to meet specific industrial requirements, such as unique profiles or materials.
Applications of Roll Formers
Construction Industry
- Used for producing roofing sheets, wall panels, and structural supports.
Automotive Manufacturing
- Forms parts like door panels, fenders, and chassis components.
Aerospace and Shipbuilding
- Shapes lightweight yet strong components for high-performance applications.
Furniture Manufacturing
- Produces metal profiles for tables, chairs, and shelving units.
Energy Sector
- Creates solar panel frames, wind turbine components, and cable trays.
Advantages of Metal Roll Formers
Precision and Consistency
- Produces uniform profiles with tight tolerances, ensuring high-quality output.
Cost-Effective Production
- Reduces material waste and labor costs compared to other forming methods.
High Efficiency
- Capable of processing large volumes of metal sheets in a short time.
Customizability
- Adaptable to produce various shapes and profiles depending on industrial needs.
Durability
- Built to handle heavy-duty applications, ensuring long-term performance.
Factors to Consider When Buying Roll Formers
Material Compatibility
- Ensure the machine is suitable for the type of metal (e.g., steel, aluminum, copper).
Production Volume
- Choose a machine that aligns with your required output capacity.
Profile Design
- Look for roll formers capable of producing the specific shapes you need.
Automation Features
- Advanced machines with automation reduce manual labor and enhance precision.
After-Sales Support
- Opt for suppliers offering training, maintenance, and spare parts.
Trends in the Roll Forming Industry
Integration of Automation
- Modern roll formers come with programmable logic controllers (PLCs) for automated operations.
Sustainability Focus
- Machines are being designed to minimize energy consumption and waste.
Advanced Materials
- Compatibility with high-strength and lightweight alloys to meet modern industrial demands.
Compact Designs
- Portable roll formers are becoming more popular for on-site and small-scale operations.
A metal roll former is an essential investment for industries requiring precise and efficient metal forming. Whether purchasing roll formers for sale or exploring advanced customization options, businesses can benefit significantly from these machines. As technology evolves, roll formers continue to offer improved performance, sustainability, and adaptability, making them a cornerstone in modern manufacturing processes.