The 4 high rolling mill is a sophisticated equipment designed for precision and efficiency. This piece of machinery is essential in the industrial process of metalworking, particularly in the manufacturing of flat products. Comprising four rolls — two working rolls and two backup rolls — this mill is specifically devised to ensure material strength and consistency, making it an indispensable tool in creating high-quality sheet metals.
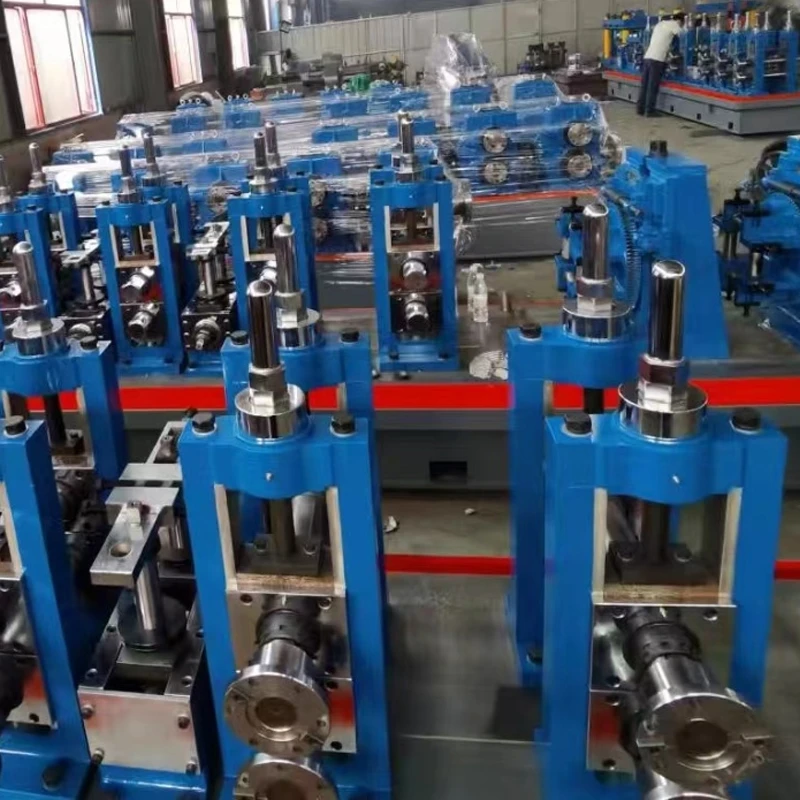
When understanding the significance of the 4 high rolling mill, one must consider its technological advancement compared to traditional mills. In essence, the 4 high configuration enhances the mill's capability to produce sheets with minimal thickness variations, ensuring high precision and tight tolerances. The key reason behind this advantage is the separation of the working and backup rolls, where the latter are substantially larger in diameter. This design counteracts the deflection of the working rolls, offering higher rigidity and enabling the production of thinner gauges without compromising the mechanical properties of the materials.
From an expert's perspective, the use of a 4 high rolling mill also provides economic benefits. By allowing for tight control over the material thickness, manufacturers are able to produce products with a consistent quality, reducing material waste. This precision not only improves the yield of the production process but also enhances the surface quality of the final product. With the rolling process being a significant cost factor in metal manufacturing, the efficiency and reduced waste associated with the 4 high rolling mill translate into noticeable cost savings and increased competitive advantage.
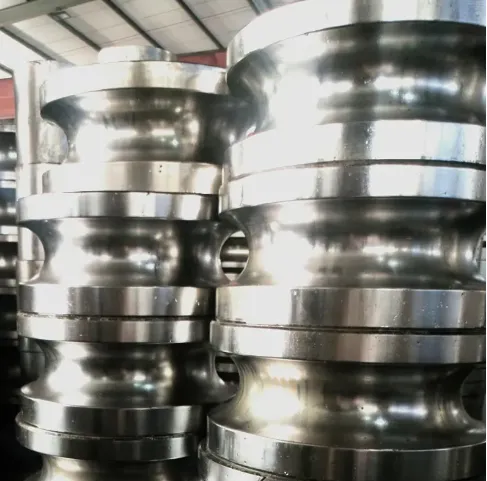
Furthermore, the versatility of the 4 high rolling mill is one of its notable attributes. This machine is not limited to producing flat products like coils and strips but is also utilized in a variety of sectors including automotive, aerospace, and electronics, where specific material characteristics — such as high surface finish and precise dimensional specifications — are paramount. The adaptability of this equipment allows it to process different types of metals, including stainless steel, aluminum, and copper, thereby meeting the diverse needs of various industries.
4 hi rolling mill
Authoritatively, the design and operation of a 4 high rolling mill demand a profound understanding of metallurgy and materials engineering. Operators and engineers must have a strong grasp of the principles of rolling, material behavior under stress, and the dynamics of heat treatment processes, which are integral to optimizing the mill's settings for specific materials and desired end-product properties. Continuous developments in materials science and engineering ensure the mill remains at the cutting-edge, with improvements in roll design and materials further enhancing its performance and durability.
Trust in the operation and outcomes of the 4 high rolling mill is critical, particularly with its widespread application in high-stakes industries. Regular maintenance, coupled with technological upgrades such as automation and process control software, improve its reliability and operational safety. Companies that invest in the latest 4 high rolling mill technology often gain a competitive edge, as they are able to guarantee the quality and conformity of their products to international standards.
To conclude, the 4 high rolling mill is a crucial component in the field of manufacturing, setting the benchmark for quality and precision in metal processing. Its expert design transcends traditional rolling capabilities, meeting the stringent demands for thin, highly uniform sheets and strips that are essential in numerous high-tech applications. Holding expertise in operating this technology confers manufacturers with enhanced process efficiencies, cost savings, and the ability to produce superior products, fostering trust and authority in their end markets.