Automated pipe cutting machines have revolutionized industries reliant on precision metal fabrication. Their evolution reflects a significant shift towards enhancing productivity and accuracy in manufacturing processes. As an experienced SEO expert with insights into the mechanics and technological implications of these machines, I’m sharing a comprehensive exploration into their utility, operation, and benefits.
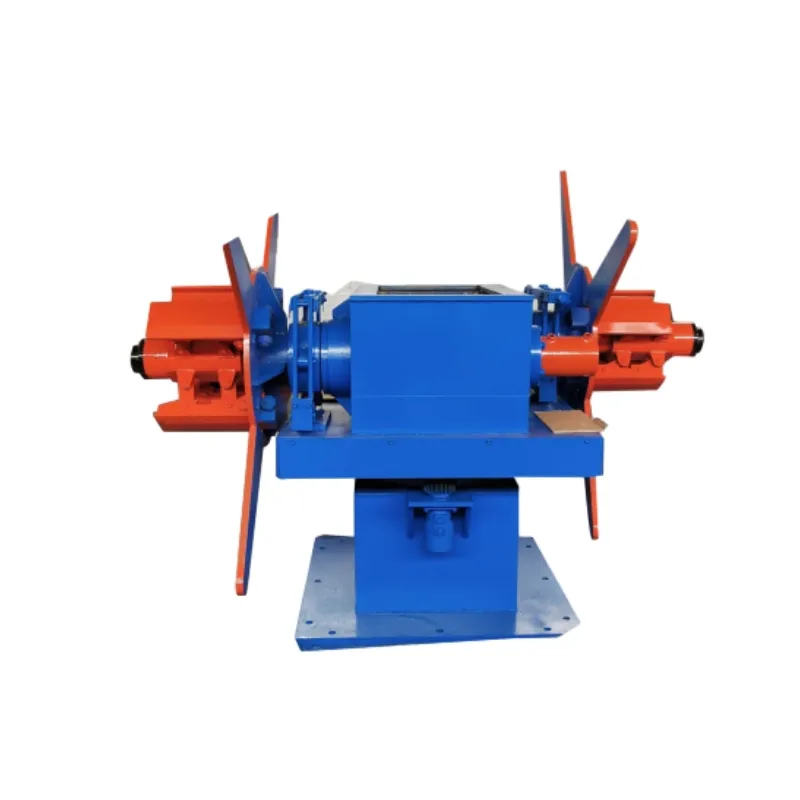
Automated pipe cutting machines serve crucial roles in industries such as automotive, aerospace, construction, and shipbuilding. They promise unparalleled precision and efficiency, establishing themselves as indispensable tools in modern manufacturing. Typically, these machines leverage advanced technologies like CNC (Computer Numerical Control) to execute accurate cuts on metal pipes, accommodating various shapes and sizes to meet complex industrial requirements.
Their precision is one of their standout features, and rightly so. The ability of these machines to consistently deliver precise cuts reduces material waste—a paramount concern in sectors where cost efficiency is crucial. Industries no longer have to worry about inaccuracies that traditionally led to significant raw material loss. Automated pipe cutting machines accurately measure and execute with a precision unattainable through manual means, highlighting their expertise in modern fabrication techniques.
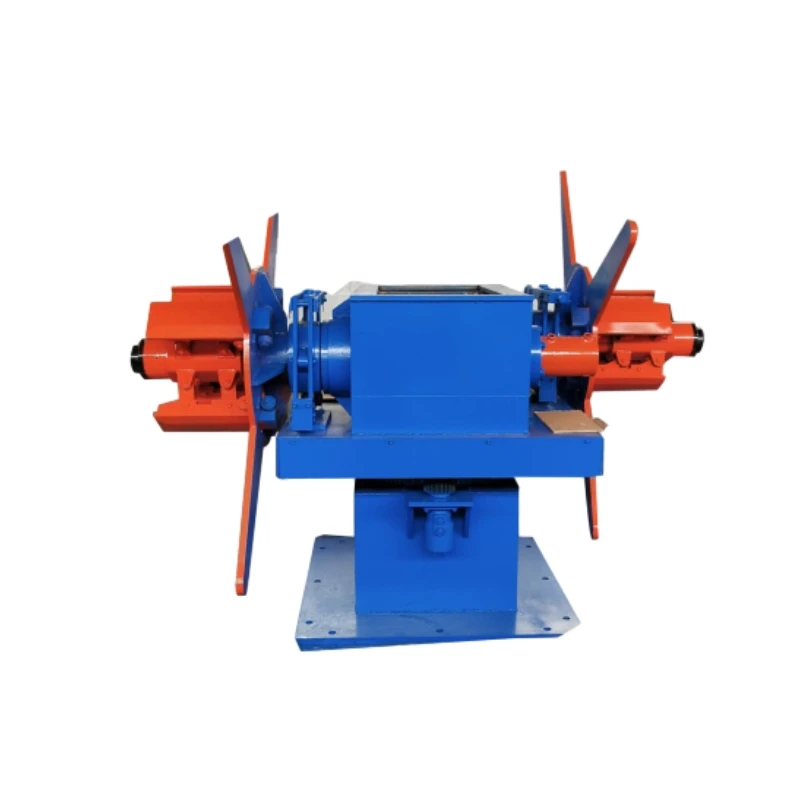
In addition to precision, the operational efficiency of automated pipe cutting machines is equally groundbreaking. By integrating automation, the duration of cutting processes is dramatically reduced, allowing factories to increase throughput without compromising on quality. This efficiency extends beyond mere speed, encompassing enhanced safety measures that ensure better protection for operators. With reduced human intervention, the likelihood of occupational hazards decreases, fostering a safe working environment—another testament to the authoritative nature of these innovations.
Furthermore, versatility is another hallmark of these machines. They are equipped to handle various materials—be it steel, copper, or composite metals—demonstrating their adaptability across different industrial domains. The ability to customize cutting techniques and patterns ensures that they meet specific project demands, offering industries the flexibility to innovate without being restricted by technological limitations.
automated pipe cutting machine
From an authoritative standpoint, automated pipe cutting machines are engineered by leading manufacturers who collaborate with industry experts to continually advance machine capabilities. These collaborations emphasize trustworthiness as they incorporate feedback and insights to refine operations, ensuring each iteration outperforms its predecessor. The reliability of these machines is further reinforced by rigorous quality assurance measures adhered to by manufacturers, ensuring these machines resiliently withstand the challenging demands of modern industries.
Trust in automated pipe cutting machines is further established by their ability to seamlessly integrate into existing manufacturing systems. They are designed with connectivity in mind, often featuring capabilities to sync with digital networks for real-time monitoring and data analysis. This integration not only boosts operational transparency but also enhances decision-making by providing vital performance metrics, fortifying their standing as trustworthy assets in industrial settings.
For entities considering adopting these machines, the investment extends well beyond immediate gains in efficiency and precision—it’s a strategic integration into smarter, more sustainable manufacturing methods. The shift towards automated solutions is driven by the perpetual industry quest for excellence and innovation, where these machines stand as embodiments of engineering prowess and industrial foresight.
In summation, automated pipe cutting machines encapsulate the transformative power of technological innovation in manufacturing. With unmatched precision, efficiency, versatility, and reliability, they continue to gain prominence, aiding industries in optimizing performance and securing a competitive edge. They represent the epitome of modern engineering, reflecting an aspiration not only for mechanical excellence but for sustainable, future-ready manufacturing processes. As the industry continues to evolve, these machines will undoubtedly remain pivotal in shaping its trajectory, bearing significance both in contemporary production and future advancements.