In the ever-evolving world of industrial engineering, the automatic pipeline welding machine stands as a beacon of innovation and efficiency. Its creation has significantly transformed the landscape of welding, providing unprecedented advantages in terms of speed, precision, and consistency.
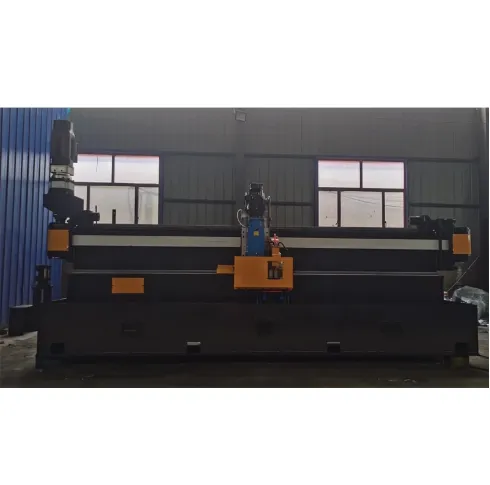
Industrial welding traditionally required a blend of meticulous skill and considerable time investment. Manual welding, while effective, often meant grappling with human error, inconsistency, and limited production pace. Enter the automatic pipeline welding machine—a tool that has not only streamlined operations but has set a new standard for quality and productivity in welding.
Automatic pipeline welding machines are engineered with advanced technology that ensures precision. These machines utilize pre-programmed procedures to execute welds with remarkable accuracy, which drastically reduces the margin for error compared to manual methods. By automating the weld path and parameters, these machines deliver uniform and high-quality welds, meeting the stringent standards set by industries such as oil and gas, construction, and shipbuilding.
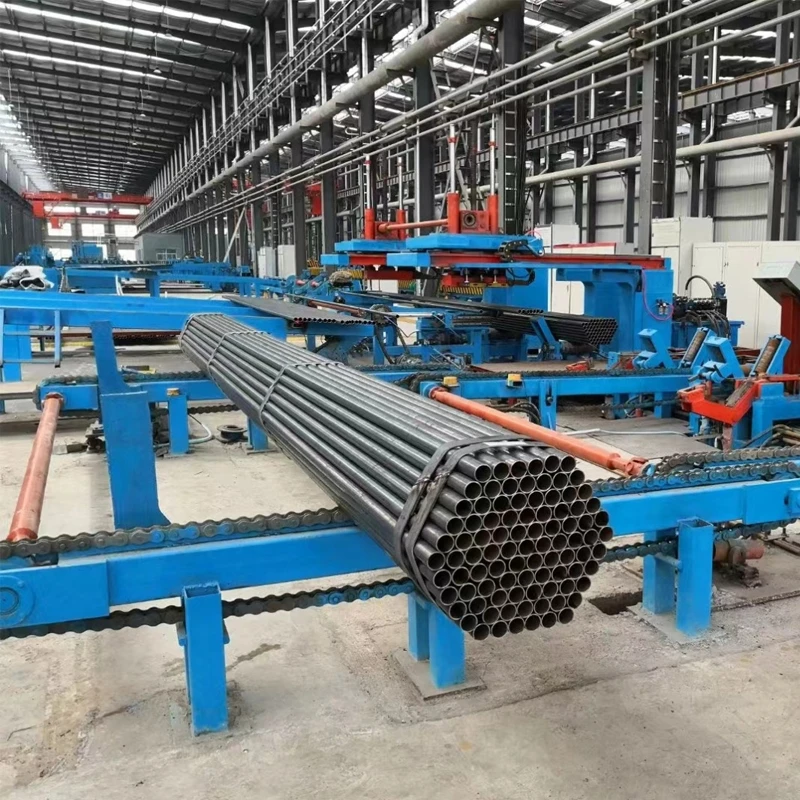
The expertise embedded in automatic pipeline welding machines is derived from years of technological advancements. These machines are equipped with sensors and exact alignment systems that adapt to the pipe's characteristics, whether it's in terms of size, shape, or material. This adaptability showcases an expert understanding of the diverse requirements present in pipeline construction. Engineers and technicians involved in developing these machines possess a deep mastery of metallurgy and robotics, contributing to their authority in the industry.
Authority in the field of automatic pipeline welding is further illustrated by the machine's capacity for real-time monitoring and data collection. This function not only ensures operational efficiency but also plays a critical role in maintaining safety standards. Data is collected throughout the welding process, allowing for comprehensive analysis and quick adjustments if anomalies arise. This continuous feedback loop affirms the manufacturer's authority but also makes these machines a trustworthy choice for large-scale projects where human oversight alone might not suffice.
automatic pipeline welding machine
Trustworthiness is a cornerstone of the automatic pipeline welding machine's design. Built with high-grade materials and subjected to rigorous testing environments, these machines are designed to withstand demanding conditions. The reliability of these machines is further endorsed by certifications from international standards organizations, bolstering their credibility for potential clients. Companies that choose to invest in automatic pipeline welding machines often benefit from reduced downtime, lower labor costs, and enhanced project timelines, which translates to a higher return on investment.
The experience of using an automatic pipeline welding machine could be likened to hiring a team of seasoned welders working in perfect harmony. The seamless operation of these machines results in significant time savings while maximizing output with minimal human intervention. Operators typically undergo specialized training to master the user interface, yet the learning curve is not steep due to the intuitive nature of modern machines.
As industries continue to grow more competitive, the demand for efficiency and precision in pipeline construction has never been higher.
Automatic pipeline welding machines represent a pivotal shift towards meeting these demands. Their integration into the industry not only highlights technological prowess but embodies a commitment to excellence, safety, and reliability.
In conclusion, the automatic pipeline welding machine is an indispensable tool in contemporary industrial processes, underpinned by expertise, authority, and trustworthiness. Its ability to enhance efficiency and maintain high standards makes it an essential piece of equipment in any ambitious operation. As technology continues to advance, these machines are set to become even more sophisticated, further solidifying their place at the forefront of industrial innovation.