C channel roll forming machines have rapidly become a cornerstone of modern construction and manufacturing industries. As industries depend more on automated processes, these machines offer precision, efficiency, and cost-effectiveness in fabricating steel C-channels. To provide a unique overview, let’s delve deep into the realm of these machines, exploring their features, benefits, and what makes them indispensable for industrial applications.
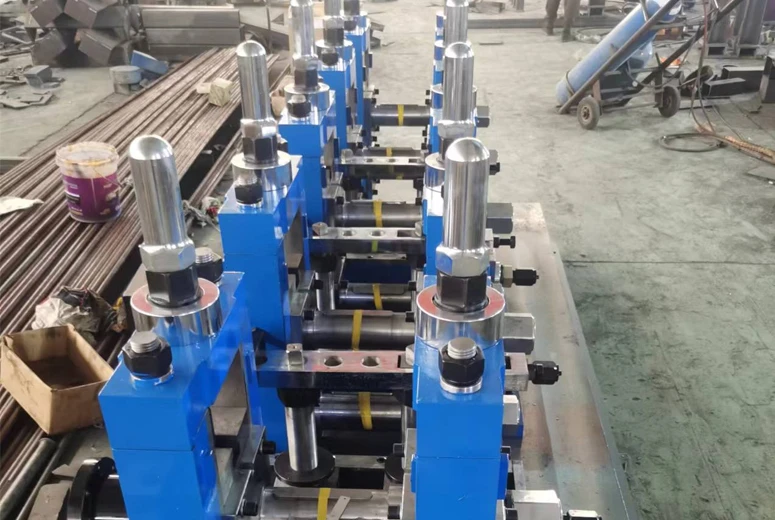
C channel roll forming machines are designed to transform metal coils into C-shaped channels through a continuous bending operation. The design and engineering of these machines allow for consistent quality and precision which are crucial in construction applications where these channels often serve as structural elements.
One of the key features that set these machines apart is their advanced roll forming capabilities. They can handle a variety of metals, including steel, aluminum, and copper, providing versatility in applications. This versatility is further amplified by their ability to produce channels of varying sizes and thicknesses, adapting to specific project requirements without compromising on precision.
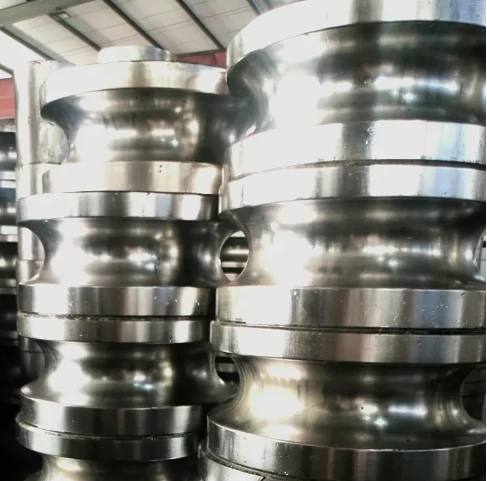
When discussing experience, companies that have integrated C channel roll forming machines into their production lines report significant improvements in efficiency and product consistency. The automation of these machines reduces the need for manual interventions, thereby minimizing human error and accelerating the manufacturing process. This automation is complemented by advanced control systems that ensure precise measurements and cuts, resulting in uniform product output and reduced wastage of raw materials.
From an expertise perspective, understanding the intricacies of setting up and maintaining these machines is essential. Professionals in the field emphasize the importance of regular maintenance checks and calibration to ensure optimal machine performance. Moreover, the integration of modern technologies like CNC (Computer Numerical Control) in these machines allows for greater flexibility and accuracy in production, facilitating complex design implementations.
c channel roll forming machine
In terms of authoritativeness, manufacturers of C channel roll forming machines are typically well-established entities with decades of experience in the metalworking industry. These manufacturers invest heavily in research and development to enhance the functionality and efficiency of their machines, ensuring they remain at the forefront of technological advances. Their commitment to innovation not only speaks to their expertise but also solidifies their position as industry leaders.
Trustworthiness is another critical factor when considering the adoption of roll forming technology. Reputable manufacturers provide comprehensive warranties and after-sales support, which are indispensable when investing in high-value machinery. Customers consistently express confidence in these machines due to their robust build quality, user-friendly interfaces, and the reliability of the manufacturers' service networks.
Furthermore,
safety is a top priority with C channel roll forming machines. Modern safety features, such as emergency stop buttons and automated shutdown protocols, are standard, ensuring that operators are protected against accidents. This focus on safety not only protects workers but also enhances the machine’s reliability and operational lifespan.
In conclusion, C channel roll forming machines represent a blend of traditional manufacturing principles with modern technological advancements. Their ability to consistently produce high-quality C-channels efficiently makes them a valuable asset across multiple industries. As the demand for sustainable and cost-effective manufacturing solutions continues to grow, these machines are poised to play a pivotal role in shaping the future of metal fabrication. By leveraging their inherent advantages, businesses can enhance their productivity, reduce operational costs, and maintain a competitive edge in the market.