Navigating the world of manufacturing, especially in metalworking, demands precision and efficiency—two characteristics epitomized by the CNC cold saw. This cutting-edge tool has reshaped how industries approach material sectioning, known for its meticulous cuts and robustness.
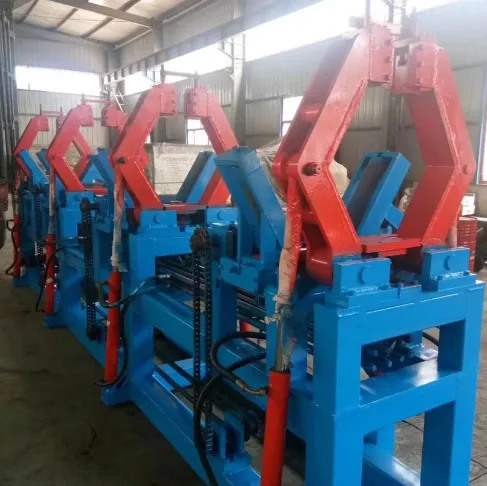
A CNC cold saw is more than just a powered circular saw used to cut metal; it represents a perfect amalgamation of technology and engineering. This advanced equipment utilizes a computer numeric control (CNC) system to dictate the blade's movements, providing unmatched precision in cutting metal materials. The cold saw got its name from its operation, where the cutting process exerts minimal heat on the blade and workpiece, contrary to the heat-producing conventional methods.
Drawing from real-world experiences within the manufacturing sphere, CNC cold saws have garnered a reputation for enhancing productivity and ensuring material integrity. A mid-sized automotive parts manufacturer reported a noticeable decline in material wastage after transitioning to a CNC cold saw. This transition was coupled with increased accuracy in their cuts, resulting in less material deformation and higher product consistency—an attribute critical in automotive manufacturing where precision is paramount.
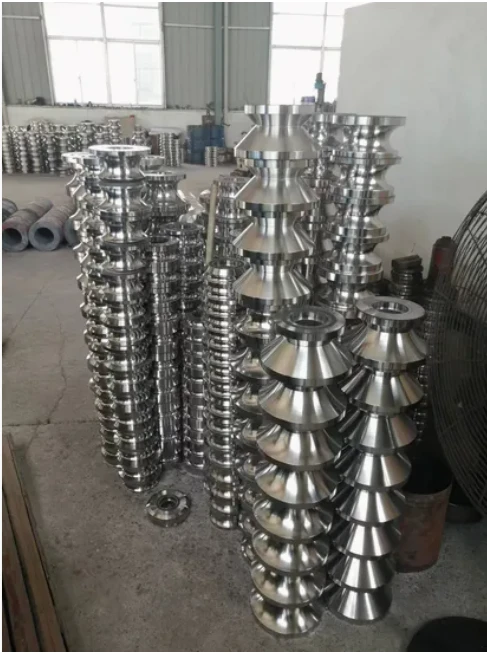
Expertise in operating CNC cold saws calls for a comprehensive understanding of the machine's intricacies. Operators must be adept at configuring the CNC software, calibrating it according to specific materials, and understanding the nuances of different blade types. Notably, the blades used in CNC cold saws vary immensely, tailored for distinct metal types, cutting speeds, and required finishes. A seasoned operator's proficiency directly correlates with optimal machine performance, extending the lifespan of the saw and minimizing downtime due to blade wear or mechanical failures.
cnc cold saw
The authority of CNC cold saws in the metalworking domain is underscored by their cost-effectiveness over time. While the initial investment might be substantial compared to traditional saws, the long-term savings paint a compelling picture. Their longevity, reduced material waste, and lowered energy consumption culminate in significant cost reductions. A large-scale construction company highlighted their transition to CNC cold saws as instrumental in trimming overhead costs, noting a 15% drop in their annual material and energy expenditures.
Trust in CNC cold saws derives from their consistent performance and the assurance they provide in quality and safety. Equipped with features such as automatic shutoffs, blade guards, and precision controls, these tools align with stringent industry safety standards, protecting operators while maintaining unparalleled accuracy. Their reliance on solid construction and top-tier materials further enhances trust, ensuring operational reliability in diverse industrial settings, from aerospace to heavy equipment manufacturing.
In conclusion, the CNC cold saw stands as a testament to modernization in the metalworking industry. Its ability to seamlessly blend precision with efficiency makes it an indispensable tool in modern manufacturing. Whether you're part of a small workshop or a colossal manufacturing plant, understanding and leveraging the potential of CNC cold saws can catalyze significant improvements in production quality and operational cost-efficiency. Investing time in mastering this tool can yield dividends in both product excellence and business profitability.