In the realm of modern manufacturing, the cold rolling line stands out as an essential process, driving efficiency and precision in metal production. Cold rolling is a critical procedure employed to reduce the thickness of metal sheets while simultaneously enhancing their strength and surface finish. This sophisticated process plays a pivotal role in the production chain, ensuring that end-products meet specific industry standards and customer demands.
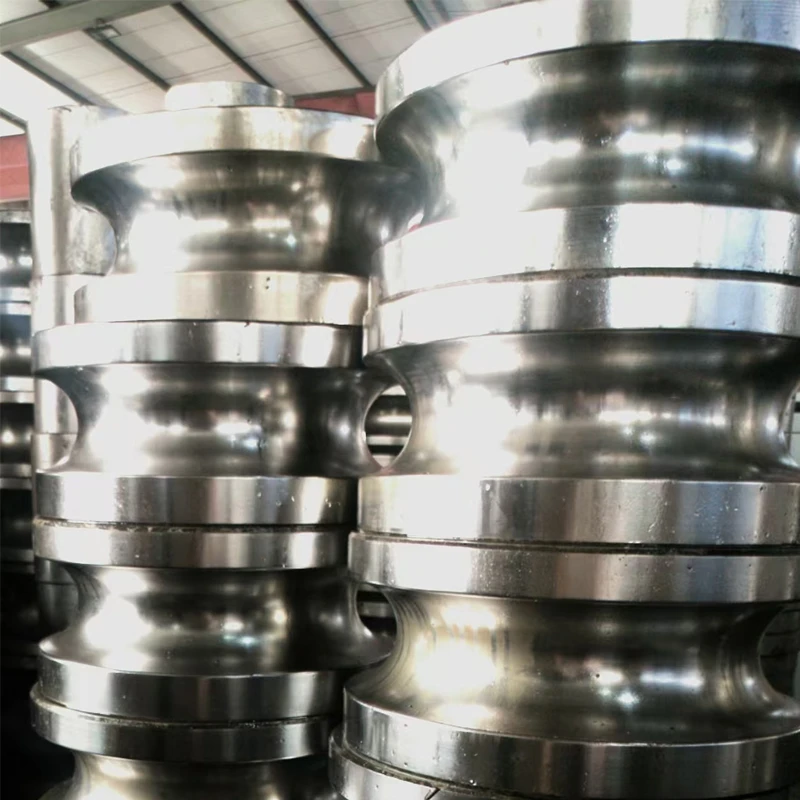
To understand the profound impact of cold rolling lines, one must delve into the nuances of their operation and the value they bring to the production process. At its core, a cold rolling line involves passing metal through a series of rollers at room temperature. This procedure increases the yield strength and hardness of the metal by inducing dislocations in its crystal structure, a phenomenon known as work hardening or strain hardening.
Companies utilizing cold rolling lines often tout the improved mechanical properties of their products. For instance, in the automotive industry, manufacturers favor cold-rolled steel for its high tensile strength, which ensures better performance and safety. Similarly, in the construction industry, cold-rolled products are preferred for their dimensional accuracy and excellent surface quality. These attributes are a testament to the expertise required to navigate and optimize cold rolling processes effectively.
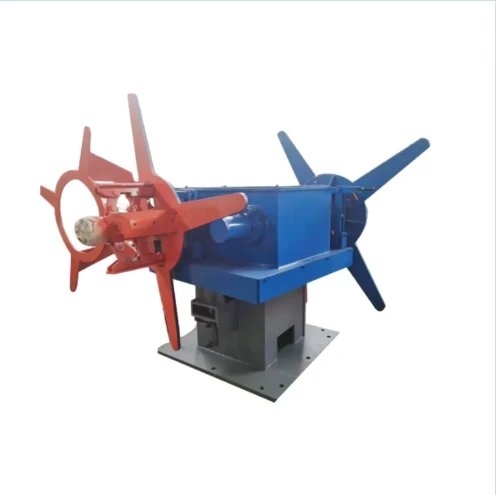
Cold rolling lines can be customized to suit a variety of materials, including steel, aluminum, copper, and brass. Each material involves a unique set of parameters to ensure the desired outcome with precision. Operators on a cold rolling line must possess a deep understanding of metallurgy and process dynamics, which are integral to achieving high-quality results. This level of expertise guarantees a reliable output of sheets, strips, and coils that are consistent with the stringent specifications demanded by technological advancements in various industries.
The authoritative nature of cold rolling lines in production settings often leads to transformational benefits. By minimizing material wastage and maximizing output uniformity, cold rolling not only contributes to economic efficiencies but also bolsters supply chain reliability. Moreover, the capability to produce thinner gauges of metals allows industries to innovate in product designs, promoting lightweight and durable outcomes that align with modern engineering trends.
cold rolling line
Trustworthiness is further cemented through rigorous quality control measures that are a staple of cold rolling line operations. Continuous monitoring, precise calibration of equipment, and adherence to international quality standards ensure that the products consistently meet necessary compliance requirements. Alongside technological proficiency, these practices form a trust-based relationship between manufacturers and their clients, establishing the cold rolling line as a credible and dependable component of the production ecosystem.
Investments in cold rolling technologies are substantiated by their ability to meet contemporary demands for sustainable production methods. The process minimizes energy consumption compared to traditional hot rolling,
reducing overall emissions. This shift represents a responsible approach to manufacturing, aligning with global calls for sustainable industrial practices.
Manufacturers implementing cold rolling lines often aim to deliver unparalleled product quality, highlighted by pristine surface finishes and precise dimensions. This superior finish not only enhances the aesthetic appeal of the final product but is often critical for industries such as electronics, where surface integrity can significantly affect performance and reliability.
In conclusion, cold rolling lines are indispensable assets within manufacturing, embodying a synthesis of experience, expertise, authoritativeness, and trustworthiness. Mastery over these lines allows manufacturers to innovate, perform consistently, and establish a competitive edge in the market. Industrial leaders have long recognized the strategic advantage that advanced cold rolling processes provide, underscoring a commitment to quality and excellence in every sheet they produce. As technology continues to evolve, the cold rolling line will remain a cornerstone of metal production, perpetually adapting to meet the ever-changing landscape of modern manufacturing needs.