In the dynamic realm of industrial manufacturing, cold rolling mill rolls hold a pivotal role in shaping the quality, efficiency, and longevity of metal products. These rolls are integral in the cold rolling process, which enhances the material properties of metals, lending them the desired specifications required for varied applications. As technology advances, investing in superior cold rolling mill rolls has become paramount not only for manufacturers but also for the entire supply chain.
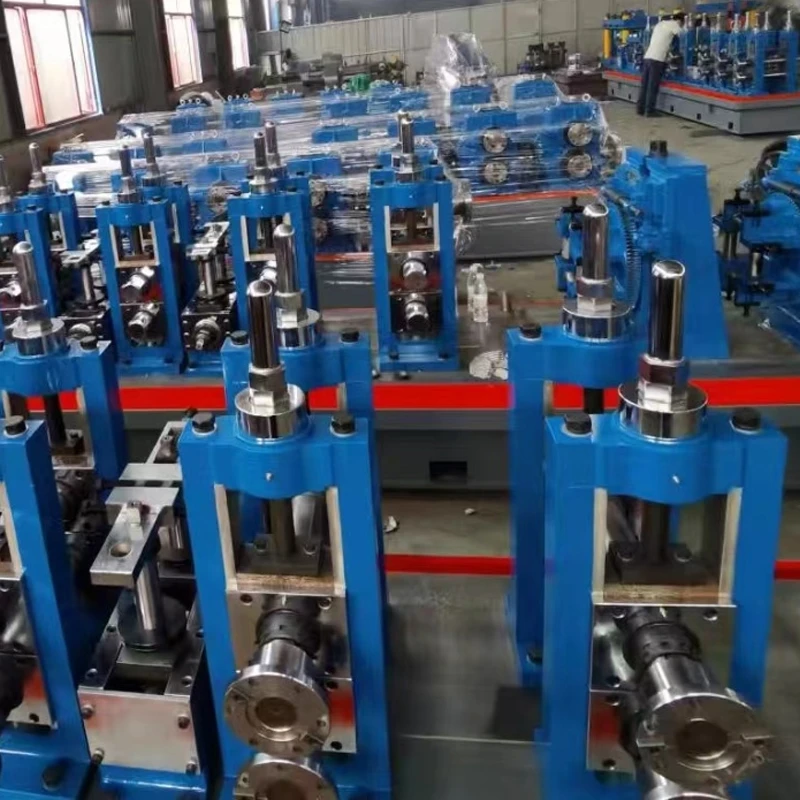
Cold rolling mill rolls are engineered for precision. They facilitate the process where metal sheets are passed between pairs of rolls to reduce thickness, improve surface finish, and ensure uniformity in the final output. This meticulous procedure significantly influences the durability and performance of metals used across automotive, construction, and consumer goods industries, among others.
For operational efficiency and cost-effectiveness, understanding the different types of cold rolling mill rolls is critical. Commonly, rolls are categorized into work rolls, backup rolls, and intermediate rolls. Work rolls directly contact the metal, necessitating properties such as high hardness and wear resistance. Backup rolls support the work rolls and are generally larger to distribute load more effectively, enhancing roll life while minimizing maintenance costs. Intermediate rolls, used predominantly in multi-roll mills, serve to amplify the reduction force without compromising the roll wear, offering a harmonious balance between force distribution and product quality.
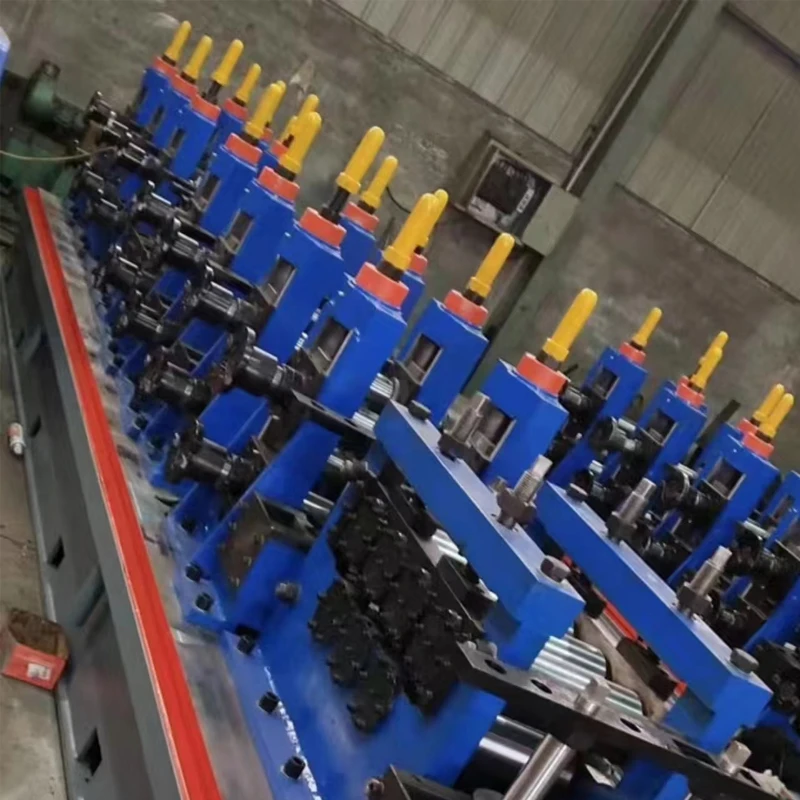
Expertise in material selection and roll design directly impacts the process outcomes. Modern manufacturing demands rolls made from robust materials such as hardened steel, high nickel alloys, or cast iron with specific treatments. The selection of materials like these aims to withstand mechanical stresses and thermal effects encountered during rolling. Beyond material composition, tailored roll surface treatments such as chromium plating or ceramic coatings can significantly extend service life and augment performance, reducing downtime and maintenance expenses.
cold rolling mill rolls
Incorporating innovative technologies in roll manufacturing has revolutionized the outcomes of cold rolling processes. Advanced simulation and modeling techniques allow manufacturers to predict roll behavior under extreme conditions, optimizing design before actual production. This proactive approach minimizes trial and error in the field, saving costly resources and time. In addition, the advent of smart manufacturing tools, such as embedded sensors and real-time monitoring, provides continuous insights into roll performance, enabling proactive maintenance schedules and reducing unscheduled downtimes.
Establishing a steadfast connection with reputable roll manufacturers is indispensable for any business aiming to gain a competitive edge. Such partnerships offer more than just products; they provide access to industry knowledge, reliability assurances, and innovative solutions tailored to specific operational requisites. A supplier’s track record, technical support capability, and commitment to research and development are crucial metrics when selecting a partner for cold rolling mill roll requirements.
Moreover, transparency and sustainable practices in roll manufacturing are gaining traction, enhancing trustworthiness within the market. Manufacturers who adopt environmentally conscious production methods not only contribute to sustainability but also align with broader corporate responsibility objectives of many businesses today. Eco-friendly roll solutions that reduce energy consumption and waste echo a commitment to sustainability, an increasingly significant consideration for stakeholders worldwide.
As industries continue to evolve, the role of cold rolling mill rolls remains central to achieving superior quality metal products. An astute focus on expertise, material excellence, and technological integration will harness the full potential of these components, driving efficiencies and elevating production standards. By adopting a forward-thinking approach, businesses can ensure that their cold rolling processes not only meet current demands but are also primed for future advancements. In this way, the cold rolling mill rolls form a cornerstone of modern manufacturing, underpinning excellence and sustainability in metal production.