Compression molding rubber stands as a pivotal process in the manufacturing of durable, high-quality rubber products. This technique offers unmatched versatility, allowing manufacturers to create a wide array of products ranging from gaskets and seals to complex automotive components. As an industry expert with years of experience, understanding the nuances of this process is crucial for producing superior products while staying competitive in an ever-evolving market.
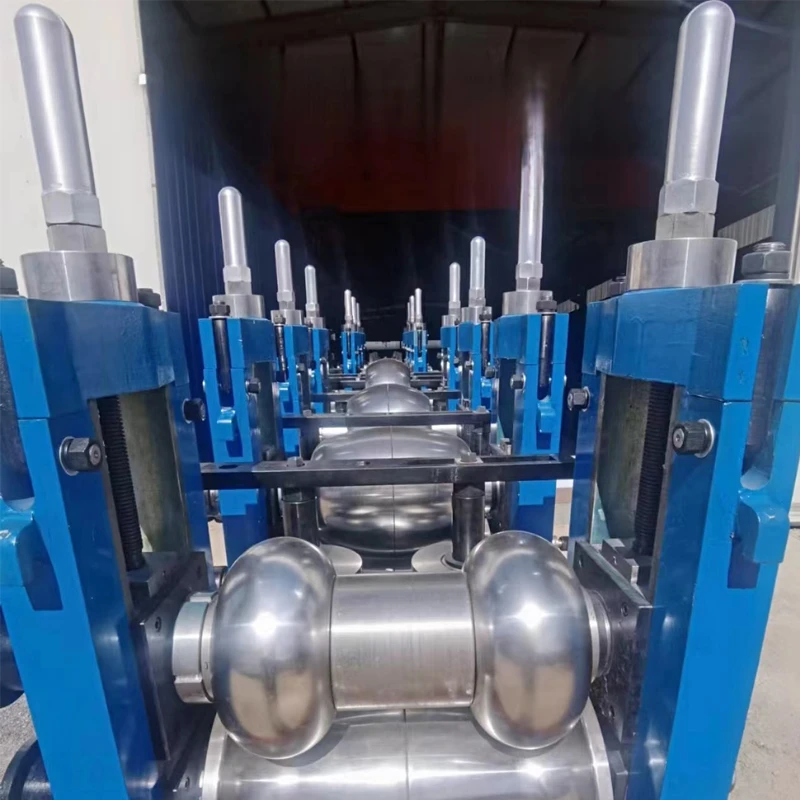
In the realm of rubber manufacturing, compression molding is often lauded for its efficiency and cost-effectiveness. The process begins with placing a pre-measured amount of rubber material into a heated mold cavity. The mold is then closed, applying significant pressure which forces the material to conform to the mold's shape. This combination of heat and pressure not only shapes the rubber but also facilitates vulcanization, a chemical process that enhances the durability and elasticity of the rubber.
One of the key advantages of compression molding is its ability to produce complex shapes and large parts that other molding processes might struggle with. This is particularly vital in the automotive industry, where components must meet stringent performance standards under varying environmental conditions. My professional expertise encompasses guiding manufacturers to select the right rubber compounds and mold designs that optimize the mechanical properties essential for automotive applications.
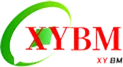
In addition to automotive, the electrical and electronic industry also benefits greatly from rubber components produced via compression molding. Rubber's insulating properties make it ideal for manufacturing components used in electronic devices, where it prevents electrical leaks and enhances safety. Through methodical testing and material selection, I've advised companies in minimizing material waste while maximizing the performance of their end products.
While compression molding offers numerous benefits, it requires precise control of process parameters to ensure product quality and consistency. Temperature, pressure, and curing time are all critical aspects that must be finely tuned. My extensive industry experience has shown that even slight deviations in these parameters can lead to defects such as bubble formation, uneven curing, or dimensional inaccuracies. To address these challenges, implementing stringent quality control measures and regular machinery maintenance is imperative.
compression molding rubber
Sustainability is another area where compression molding excels. The process allows for the reuse of waste rubber, which not only reduces material costs but also aligns with increasing environmental regulations. By integrating sustainable practices, manufacturers can not only reduce their carbon footprint but also appeal to environmentally conscious consumers. This dual benefit has proven to be a strategic advantage in maintaining a competitive edge.
Moreover, the development of advanced materials has broadened the horizons of what is achievable with compression molding. High-performance elastomers with enhanced chemical resistance, temperature stability, and mechanical strength are now readily available. As a consultant, I emphasize staying abreast of these material advancements to innovate and improve product offerings continuously.
Trustworthiness in this domain demands transparent communication and reliability. Providing clients with comprehensive reports on the molding process, material selection criteria, and expected performance outcomes fosters trust and establishes long-term relationships. In my practice, transparency transcends the client relation; it envelops every stage of production to ensure that stakeholders are informed and invested in the product's success.
In summary, the expertise and experience embedded in mastering compression molding rubber are indispensable assets for navigating the intricacies of modern manufacturing industries. By focusing on process optimization, quality assurance, and sustainable practices, manufacturers can harness the full potential of compression molded rubber products. The discipline not only reshapes materials into essential components but also molds the future of manufacturing with innovations that meet the demands of today and beyond.