In the fast-paced world of metal processing, efficiency and precision are paramount. Enter the decoiler, an indispensable piece of machinery that plays a vital role in the production line. A decoiler, known for its simplicity and effectiveness, is engineered to uncoil metal sheets, preparing them for further processing tasks such as cutting, bending, and stamping. This article delves into the essentials of decoilers, shedding light on their functionality, types, and benefits, and explains why they are a cornerstone in the manufacturing industry.
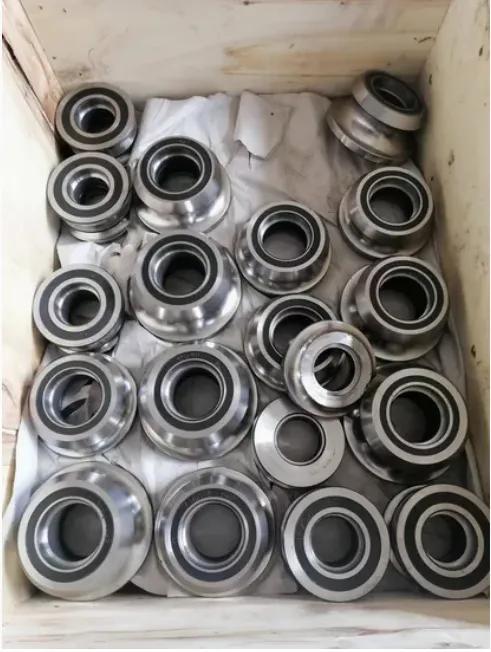
Decoilers come in various forms, tailored to meet the diverse needs of industries ranging from automotive to construction. The fundamental principle behind all decoilers is the unwinding of large rolls of metal while maintaining tension to prevent deformation. This capability ensures that the metal sheets are perfectly flattened and ready for the next stage of production. The design of a decoiler is crucial, as it needs to handle different thicknesses and widths of metal while maintaining consistent performance.
There are several types of decoilers, each suited to specific applications. The most common is the manual decoiler, which is typically used in small-scale operations. Manual decoilers require human intervention to operate, which makes them less suitable for high-speed production lines but offers flexibility for bespoke tasks. On the other hand, motorized decoilers are equipped with powered uncoiling systems, allowing for high-speed and continuous processing. These machines are highly efficient, reducing downtime and optimizing workflow, which is essential for large-scale manufacturing.
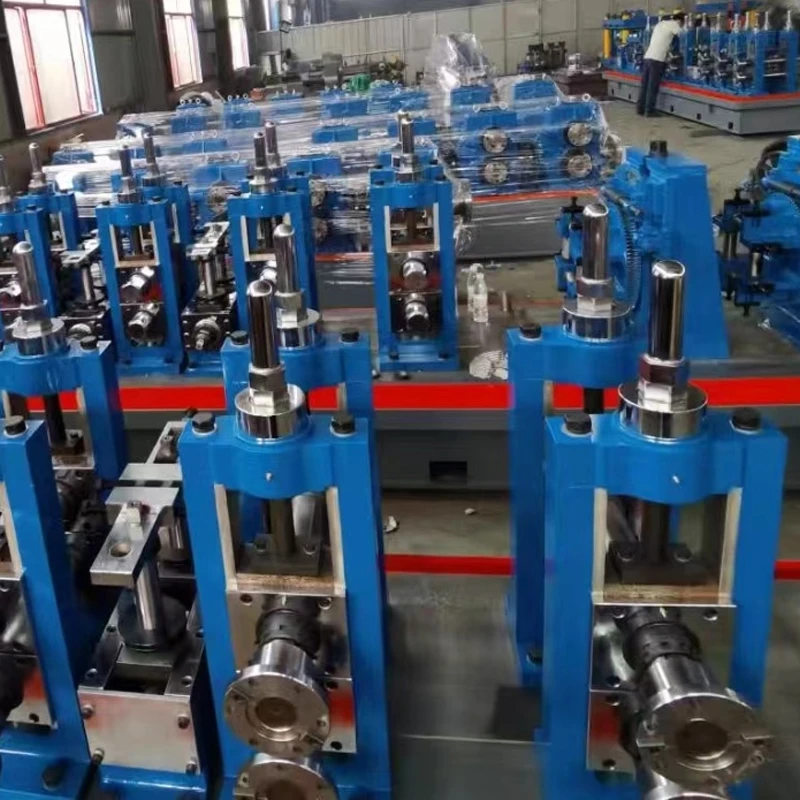
Hydraulic decoilers represent the next leap in decoiling technology. These machines utilize hydraulic systems for precise control of tension and speed, making them ideal for handling heavy-duty coils. The hydraulic decoiler’s ability to automate the adjustment of tension and uncoiling speed ensures uniformity and precision in metal processing, significantly reducing the likelihood of material waste.
Automatic decoilers take automation a step further by integrating advanced control systems, such as programmable logic controllers (PLCs). These systems offer unmatched precision in monitoring and adjusting operations, minimizing human intervention and maximizing throughput. As industries aim for higher efficiency and increased production capacity, automatic decoilers are becoming the go-to solution for manufacturers worldwide.
decoiler
The benefits of incorporating a decoiler into a production line extend beyond mere operational efficiency. They also enhance the quality of the final product. Proper tension and handling during the decoiling process prevent unwanted stress and strain on the metal sheets, which can lead to defects in the final product. This precision ensures that components fit together seamlessly during assembly, reducing the likelihood of errors and inconsistencies.
Moreover, decoilers contribute significantly to cost reduction. By minimizing material waste and optimizing the flow of metal through the production line, they lower the overall production costs. This efficiency, in turn, allows manufacturers to offer competitive pricing, a critical factor in a highly competitive market.
For businesses looking to invest in a decoiler, understanding the specific requirements of their production line is crucial. The choice between a manual, motorized, hydraulic, or automatic decoiler should be based on factors such as the volume of production, the type of metal used, and the budget. Moreover, working with reputable manufacturers and suppliers who offer quality assurance and after-sales support can enhance operational longevity and reliability.
With the continuous advancements in technology, the future of decoilers looks promising. Innovations such as the integration of smart sensors and artificial intelligence are set to revolutionize the efficiency and adaptability of decoilers. These advancements will not only improve operational performance but also expand the capabilities of decoilers, allowing them to handle a wider range of materials and complexities.
Decoilers are not just machines; they are a pivotal component of modern manufacturing processes. Their ability to streamline operations, enhance product quality, and reduce costs makes them indispensable in today’s industrial landscape. As industries evolve, the role of decoilers will only grow in importance, driving innovation and excellence in metal processing. Investing in a decoiler is not just an acquisition; it’s a strategic step toward achieving higher productivity and setting benchmarks in quality.