Electrical plastic molding is a transformative technology that has revolutionized the way electrical components are manufactured today. This process not only enhances the precision and efficiency of manufacturing but also ensures the durability and performance of the final products, making it a cornerstone in the production of electrical goods.
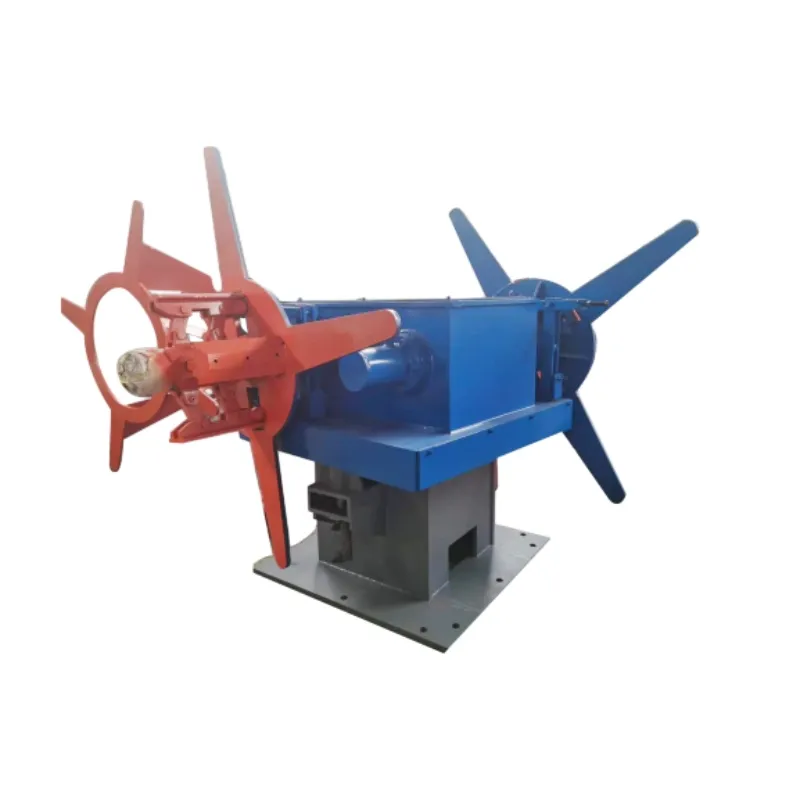
In the realm of electrical plastic molding, the blend of expertise and cutting-edge technology is critical. Professionals in this field bring years of honed skills and vast knowledge in materials science, polymer chemistry, and intricate design to the table. Their authoritative insight into how plastics behave under different conditions enables them to create parts that not only meet industry standards but surpass them in longevity and performance.
Experience plays a fundamental role in the refinement of the molding processes. Through trial, error, and triumphs in various projects, experts have developed proprietary techniques and methodologies that ensure optimal results. The confidence that comes from such extensive fieldwork is shared across teams, fostering an environment of continual learning and innovation. These experts often document their findings in reputable journals and contribute to seminars and conferences, further solidifying their authority in the industry.
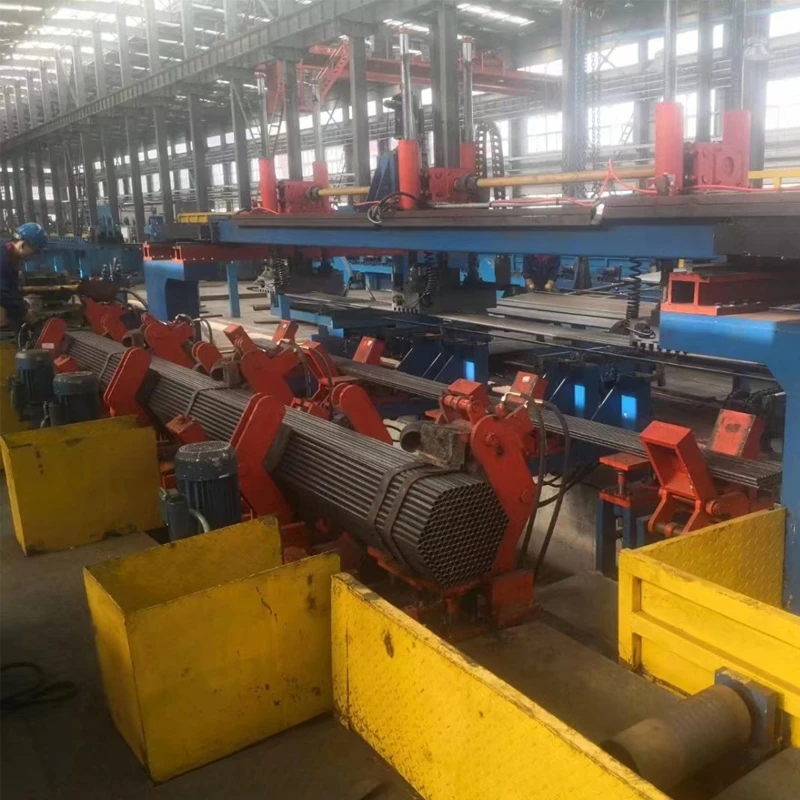
The expertise in electrical plastic molding extends beyond the technical know-how to include a comprehensive understanding of industry standards and regulations. Professionals stay updated with advancements in plastic materials and molding technologies, applying this knowledge to achieve compliance with international safety and quality certifications. Their thorough understanding of regulations such as REACH, RoHS, and UL standards ensures that products are safe, sustainable, and ready for global markets.
When considering trustworthiness, it’s important to look at the partnerships and collaborations that companies build in the electrical plastic molding sector. The trust gained through successful projects with leading electronics brands highlights the reliability of their processes and products. Furthermore, many companies invest heavily in quality assurance, implementing rigorous testing and inspection procedures to ensure that each component meets the stringent requirements before it reaches the customer.
electrical plastic molding
The insightful application of electrical plastic molding techniques is reshaping product development across industries. The technology allows for reduced material waste, faster production cycles, and exceptional precision in creating complex geometries. Such advantages lend themselves to greater innovation in product design, enabling engineers to push boundaries and meet consumer demands for smaller, more efficient gadgets.
Another significant benefit is the sustainability aspect of electrical plastic molding. With the growing emphasis on green manufacturing, the process is designed to minimize environmental impact. Reusable molds, biodegradable materials, and energy-efficient machinery are deployed to lessen the carbon footprint. This commitment to sustainability not only enhances the brand image but also aligns with the global shift towards eco-conscious production.
As the demand for high-quality electrical components continues to grow, the role of electrical plastic molding becomes even more pivotal. It supports the creation of products that are not only functional but also reliable and durable, ensuring high performance throughout their lifecycle. This consistent quality assurance strengthens consumer confidence, making molded components a preferred choice for manufacturers looking to differentiate their products in a competitive market.
In conclusion, electrical plastic molding stands as a testament to what can be achieved through a synergy of experience, expertise, authority, and trust. Companies leveraging this technology can produce electrical components that set new standards in quality and innovation, catering to an ever-evolving market. By prioritizing these core values, they continue to lead the way in electrical manufacturing, influencing both present and future trends in the industry.