ERW (Electric Resistance Welding) welding machines have revolutionized the manufacturing and production industries by offering an efficient and reliable method for joining metal pipes and tubes. These machines utilize the principle of electric resistance to generate heat and fuse materials, ensuring a seamless and durable bond. As the demand for high-quality welded products continues to rise, understanding the intricacies of ERW welding machines becomes imperative for businesses aiming to optimize their production processes.
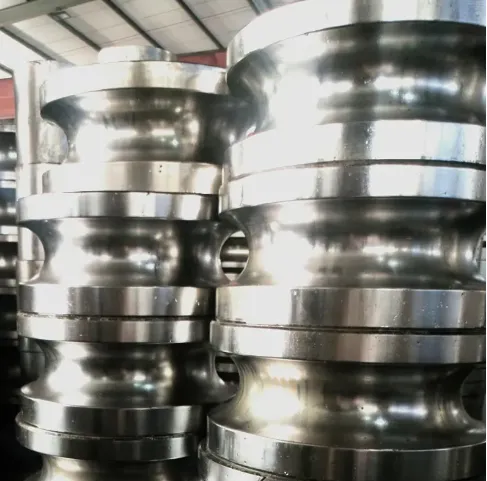
One of the standout features of ERW welding machines is their ability to produce high-quality welds at a relatively low cost. This makes them an attractive option for industries that require large-scale production without compromising on quality. Unlike traditional welding methods that can be labor-intensive and time-consuming, ERW machines offer a streamlined process where metal pieces are fed into the machine, welded, and formed rapidly. This efficiency not only boosts production rates but also translates into cost savings for manufacturers.
In terms of expertise, it is essential to recognize the technical aspects that contribute to the superior performance of ERW welding machines. The process involves passing an electric current through metal components that are pressed together. The resistance to the current generates heat, causing the edges of the metal to melt and fuse. This creates a bond that is as strong as—or in some cases, stronger than—the base materials. The expertise required to operate these machines effectively includes understanding the electrical parameters, such as current, voltage, and pressure, which are crucial in achieving optimal weld quality.
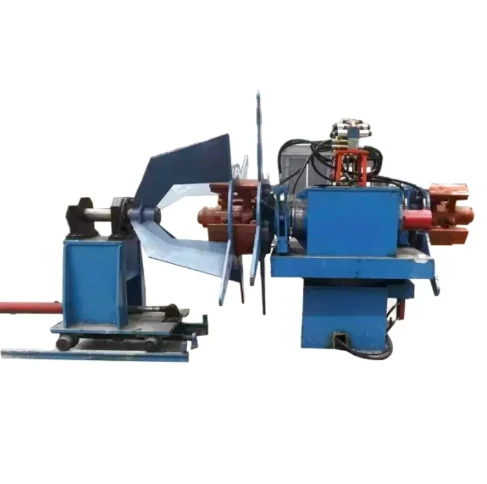
The authority of ERW welding machines in the welding industry is undeniable, especially when considering their application across various sectors such as automotive, construction, and infrastructure development. Many leading manufacturers rely on ERW technology for producing structural tubes, pipes for oil and gas pipelines, and components for automotive frames. These applications demonstrate the machines' versatility and the trust that industry leaders place in ERW technology.
When discussing trustworthiness, it is vital to highlight the safety and reliability of ERW welding machines. Modern machines are equipped with advanced features such as real-time monitoring systems and automated controls, which enhance precision and reduce the likelihood of human error. Moreover, many machines adhere to international safety standards, ensuring their operation poses minimal risk to operators. The emphasis on safety and precision further cements the trust that manufacturers have in ERW machines, knowing they can consistently produce high-quality welds while safeguarding their workforce.
erw welding machine
In addition to the core benefits, it is worth exploring the innovative advancements in ERW welding technology that propel its status in the industry. Recent developments have focused on increasing the efficiency of the machines through automation and digital integration. For instance, the incorporation of IoT (Internet of Things) technologies allows for predictive maintenance, where the machine's performance is continuously analyzed to anticipate and address potential issues before they disrupt production. This proactive approach not only minimizes downtime but also extends the lifespan of the machines.
Furthermore, the ecological impact of manufacturing processes is a growing concern, and ERW welding machines offer an environmentally friendly solution. Since the welding process is highly efficient and generates minimal waste, it aligns with sustainable manufacturing practices. Additionally, the machines' energy consumption is optimized to reduce the carbon footprint, making them a responsible choice for companies committed to green initiatives.
For businesses considering investing in ERW welding machines, it is advisable to engage with reputable suppliers and manufacturers who can provide comprehensive support and training. Understanding the specific needs of your production line and selecting machines tailored to those requirements can significantly enhance operational efficiency. Moreover, staying informed about the latest technological advancements in ERW welding will ensure that your business remains competitive in an ever-evolving industry landscape.
In conclusion,
ERW welding machines stand out as a pillar of modern welding technology. Their ability to deliver cost-effective, high-quality, and reliable welds positions them as an indispensable asset for industries that prioritize efficiency and sustainability. By leveraging the expertise of skilled operators and the authority of well-established manufacturers, businesses can harness the full potential of ERW technology, ensuring long-term success and growth.