Gantry straightening presses are pivotal in the world of industrial fabrication, offering precise and reliable solutions for straightening heavy and large-scale structures. These machines are engineered to achieve unparalleled accuracy and efficiency, making them essential tools for industries such as automotive manufacturing, shipbuilding, and railway engineering. The integration of advanced technology in gantry straightening presses ensures optimal performance, which enhances production capabilities significantly.
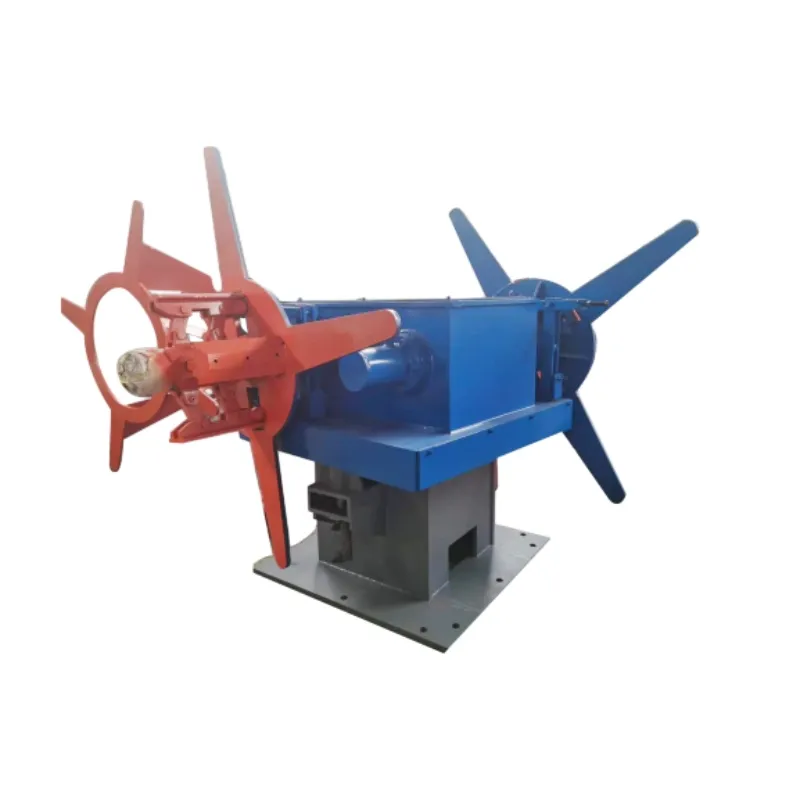
A standout feature of these machines is their adaptable design, tailored to handle a diverse range of materials and structural complexities. This flexibility allows operators to customize the press according to specific project requirements, ensuring that even the most challenging straightening tasks are addressed with ease and precision. The robust construction of gantry straightening presses contributes to their durability, providing long-term value and reliability in high-demand environments.
One of the critical components of a gantry straightening press is its hydraulic system, which is responsible for exerting controlled force to straighten materials. The hydraulic system is engineered to deliver consistent pressure, allowing for precise adjustments that cater to different material properties and thicknesses.
This capability not only improves the quality of the final product but also reduces the risk of material fatigue or damage during the straightening process.
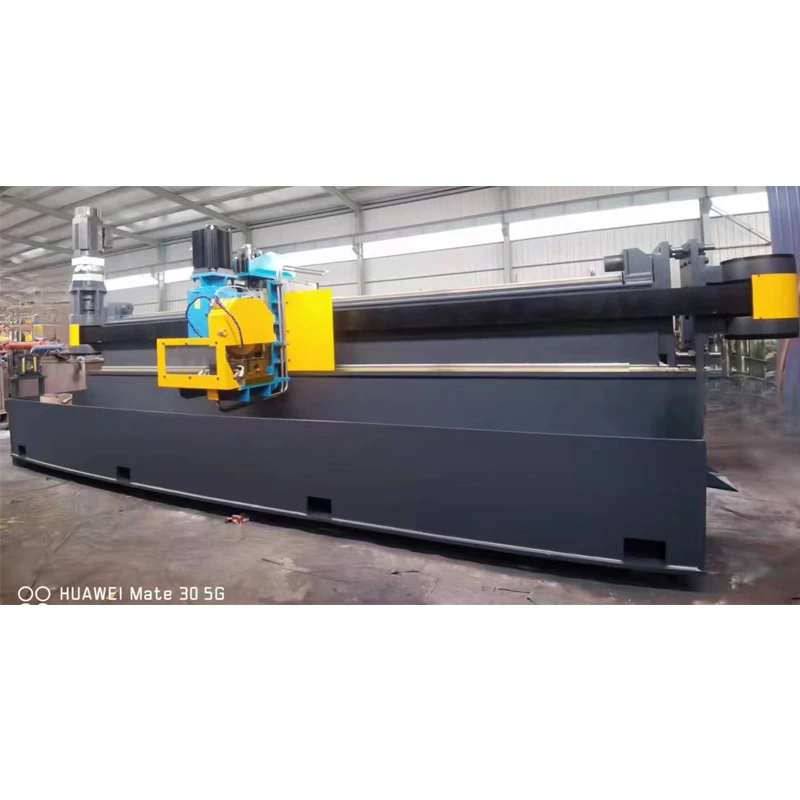
Moreover, the integration of digital controls and automated systems in modern gantry straightening presses enhances their effectiveness. Operators can use intuitive interfaces to monitor and adjust parameters in real-time, ensuring optimal alignment and consistency throughout the operation. This automation reduces the level of manual intervention required, minimizing the possibility of human error and increasing the overall efficiency of the production process.
gantry straightening press
In addition to their technical prowess, gantry straightening presses contribute significantly to workplace safety. The automated and enclosed designs of these machines reduce direct exposure to moving parts, protecting operators from potential injuries. Furthermore, the ergonomic layout ensures that all controls are easily accessible, facilitating safe and efficient operation while minimizing operator fatigue.
The expertise required to operate a gantry straightening press should not be understated. Proper training ensures that operators understand the intricacies of machine mechanics, hydraulic systems, and digital controls. This knowledge is essential for maintaining the press, ensuring its longevity, and achieving high-quality outputs. Companies often invest in ongoing training programs to keep operators abreast of technological advancements and industry best practices.
Trust in a gantry straightening press is built through the quality of its manufacturing and the reliability of its components. Leading manufacturers prioritize rigorous quality control processes and use premium materials to construct these machines, ensuring that they withstand the rigors of heavy industrial use. Reputable brands also offer comprehensive customer support and maintenance services, which are invaluable in maximizing the press's performance and lifespan.
In conclusion, gantry straightening presses are indispensable assets for industries needing precise alignment of large-scale materials. Their advanced technology, adaptability, and safety features make them a preferred choice for enhancing productivity and product quality. With proper operation and maintenance, these machines not only meet but exceed the demands of modern industrial fabrication, providing companies with a competitive edge in the global market. As technology continues to evolve, the capabilities of gantry straightening presses will undoubtedly expand, further cementing their role in shaping the future of manufacturing and engineering.