The landscape of modern foundry operations has experienced a significant transformation with the evolution of green sand molding machines. These machines are pivotal in enhancing productivity, ensuring consistency, and reducing costs in the manufacturing process.
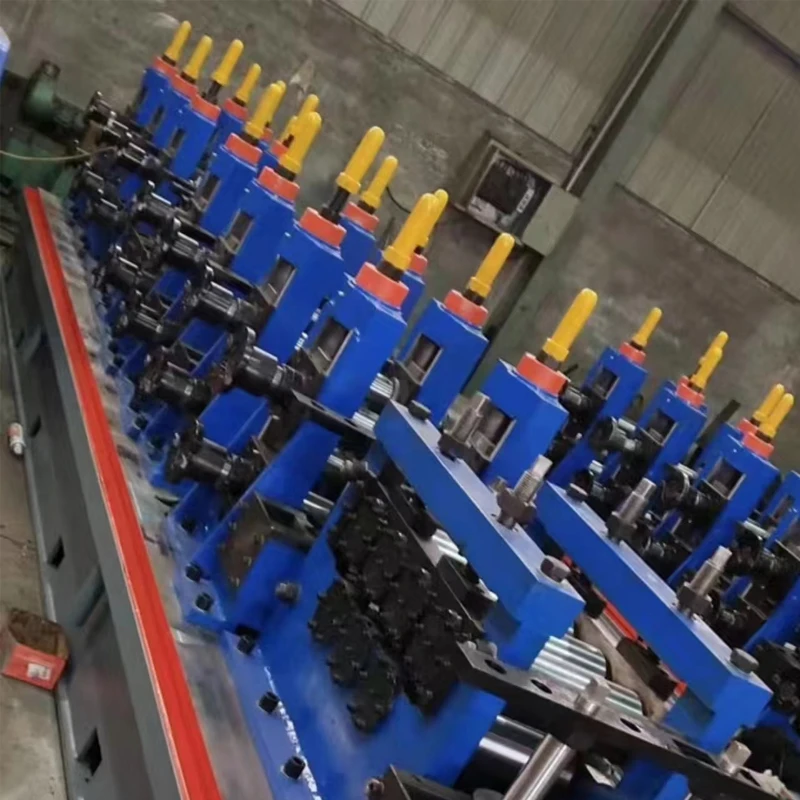
Understanding green sand molding machines involves exploring their functionality, benefits, and the expertise required to operate them efficiently. These machines mix sand, clay, water, and additives, producing a moldable material perfect for creating intricate foundry molds. The “green” in green sand refers to the moisture content present in the sand, making it pliable without needing baking or drying.
One of the key experiences that many foundry operators report is the increased efficiency brought by advanced green sand molding machines. Traditional molding processes required extensive manual labor, which often led to inconsistencies and variations in product quality. Modern machines, however, are equipped with precise controls and automation features that ensure each mold is created with the exact specifications required. This not only enhances productivity but also ensures that the quality of the molds is consistent, mold after mold.
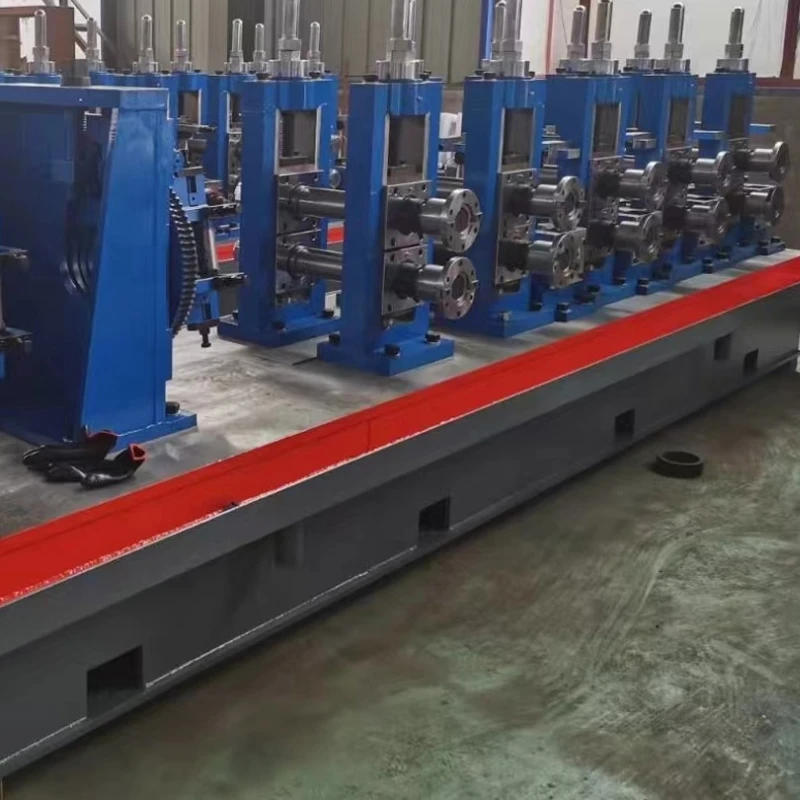
Delving into expertise, the operation of green sand molding machines does necessitate a certain level of skill and knowledge. Operators must understand not only the mechanics of the machines but also the properties of the materials they are working with. The moisture content, sand granulation, and clay composition must be meticulously managed to prevent defects in the final cast product. Training programs and certifications for operators are essential for ensuring that a foundry can maximize the potential of these advanced machines.
green sand molding machine
In terms of authoritativeness, the integration of green sand molding machines speaks volumes about a foundry's commitment to modern techniques and environmental responsibility. These machines offer a more sustainable production method. The sand used can be recycled and reclaimed,
significantly reducing waste. Additionally, because these molds do not require baking, the energy usage in the foundry is notably decreased, aligning with global efforts to reduce carbon footprints.
From a trustworthiness perspective, manufacturers who invest in high-quality green sand molding machines often see improved trust with their clients. The consistency and reliability of the products speak for themselves; customers are assured that they will receive components that meet stringent specifications and perform reliably, time after time. This consistency builds a foundation of trust, which is crucial in industries that rely on precision parts, such as automotive, aerospace, and heavy machinery sectors.
The maintenance of these machines is crucial to sustaining their peak performance, and this is where professional expertise becomes invaluable again. Regular maintenance schedules must be adhered to, ensuring parts are replaced proactively and systems are checked frequently. Downtime due to machine failure can be costly, and experienced operators can predict issues before they evolve into significant problems.
In conclusion, green sand molding machines represent a monumental shift in how foundries operate, embodying cutting-edge technology that delivers enhanced productivity and sustainability. The experience of using these machines reveals significant workflow improvements, the need for technical expertise ensures that these improvements are fully realized, their authoritative stance on sustainability echoes modern environmental concerns, and their dependability fosters trust among clients. For any foundry serious about leading in a competitive marketplace, investing in green sand molding machines signifies forward-thinking and a commitment to quality that cannot be undervalued.