In the world of industrial manufacturing and metalworking, hydraulic plate cutting machines have become indispensable tools, offering precision, efficiency, and versatility. These machines are designed for cutting heavy metal sheets with minimal effort and maximum accuracy. As a seasoned industrial expert, I provide insights into the capabilities, applications, and advantages of hydraulic plate cutting machines, highlighting their pivotal role in modern metalworking.
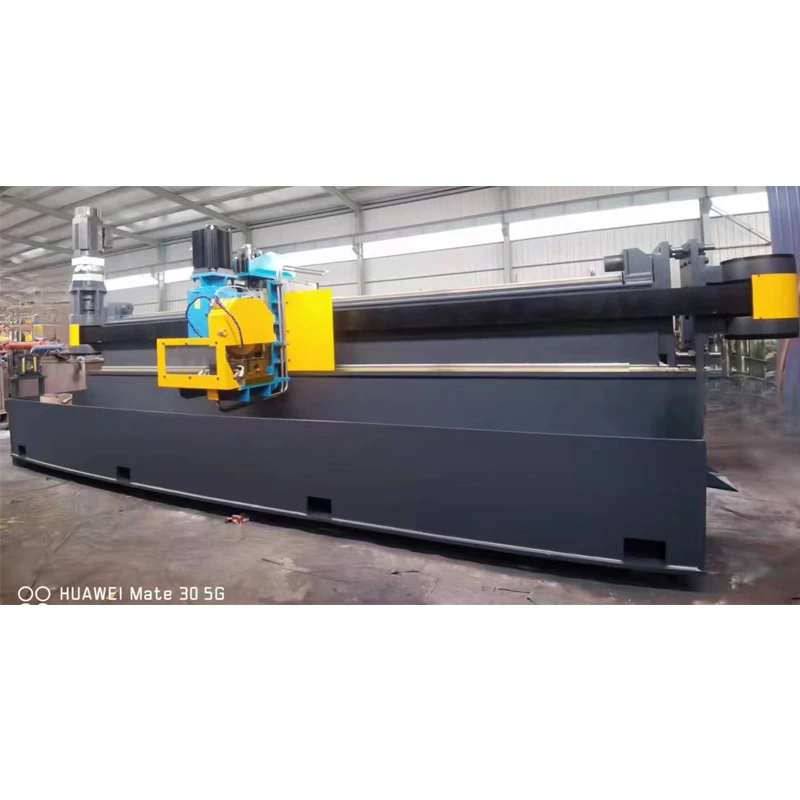
Hydraulic plate cutting machines are engineered for heavy-duty operations, leveraging hydraulic power to exert immense force on metal sheets. Unlike traditional mechanical cutters, hydraulic systems use fluid pressure to enhance cutting efficiency, offering smooth operations with minimal maintenance requirements. The seamless integration of hydraulic technology ensures consistent precision even with thick metal plates, optimizing production processes while reducing waste.
The versatility of hydraulic plate cutting machines is critical in a variety of industries, including automotive, aerospace, construction, and shipbuilding. These machines facilitate intricate cutting tasks, allowing manufacturers to produce components with complex geometries and tight tolerances. In automotive and aerospace industries, where precision is crucial, hydraulic machines ensure that each cut meets stringent quality standards, thereby enhancing the performance and safety of the final products.
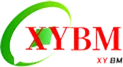
One of the significant advantages of hydraulic plate cutting machines is their adaptability. These machines can handle diverse materials ranging from mild steel to stainless steel, and even non-ferrous metals like aluminum and copper. This adaptability makes them a valuable asset for manufacturers dealing with different metal types and thicknesses. By adjusting the machine's settings, operators can achieve optimal cutting conditions tailored to specific material properties, thus ensuring efficient production workflows.
hydraulic plate cutting machine
Expertise in using hydraulic plate cutting machines can significantly impact an organization’s manufacturing capabilities. Operators need to be well-trained in machine handling, understanding hydraulic principles, and safety protocols to avoid accidents. Knowledge of maintenance procedures is equally important to extend the machine's lifecycle and maintain peak performance. Regular inspections and timely interventions can prevent hydraulic fluid leaks and ensure all components function correctly, preserving the machine's reliability and precision.
From an authority and trustworthiness perspective, investing in high-quality hydraulic plate cutting machines from reputable manufacturers is crucial. Renowned brands are more likely to offer robust machines backed by comprehensive warranties and customer support. Verified certifications and compliance with international standards serve as indicators of the machine's quality and safety. Manufacturers that provide training and after-sales service further establish trust, ensuring that clients can maximize the benefits of their investment.
In conclusion, hydraulic plate cutting machines represent a vital component in the arsenal of modern manufacturers. With their ability to deliver precision cuts efficiently, they empower industries to innovate and improve product quality. By leveraging expertise in operating these machines and choosing reputable manufacturers, businesses can enhance their production capabilities, ensuring long-term success in a competitive marketplace. The combination of precision, versatility, and reliability makes hydraulic plate cutting machines indispensable in today’s metalworking landscape.