Jet combination shear, brake, and roll machines are quintessential tools in any metalworking workshop, providing unmatched versatility and functionality. With the capability to perform shearing, braking, and rolling all in one, these combo machines save time, space, and resources, while enhancing productivity. Drawing from extensive experience and industry expertise, it becomes evident that selecting the right combination machine is pivotal to achieving precision and efficiency in metal fabrication projects.
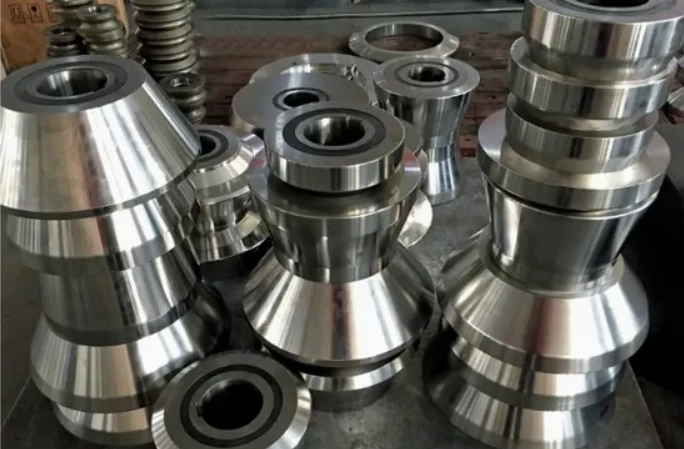
When considering the purchase of a jet combination shear, brake, and roll machine, it's crucial to evaluate the product's construction and build quality. High-grade materials and precision-engineered components are not merely aspects to desire but fundamentals that ensure longevity and operational reliability. Machines built with robust steel frames offer resilience against the rigorous demands of metalworking, providing consistent results and mitigating frequent maintenance needs. A machine’s structural integrity significantly impacts its performance, making it vital for workshop owners to prioritize durable designs to uphold their authority as reliable creators of quality metal products.
Expertise in operating these machines comes with understanding and mastering their multi-functional capabilities. Shearing involves cutting through sheets of metal with precision, requiring keen attention to blade sharpness and alignment to prevent the costly reworking of materials. Users must familiarize themselves with the machine’s cutting capacity, often denoted by thickness and width limits, ensuring that their projects align with the machine’s capabilities. Mastery over the shearing function places workers in an authoritative position over materials, dictating precise cuts that facilitate seamless subsequent processes.
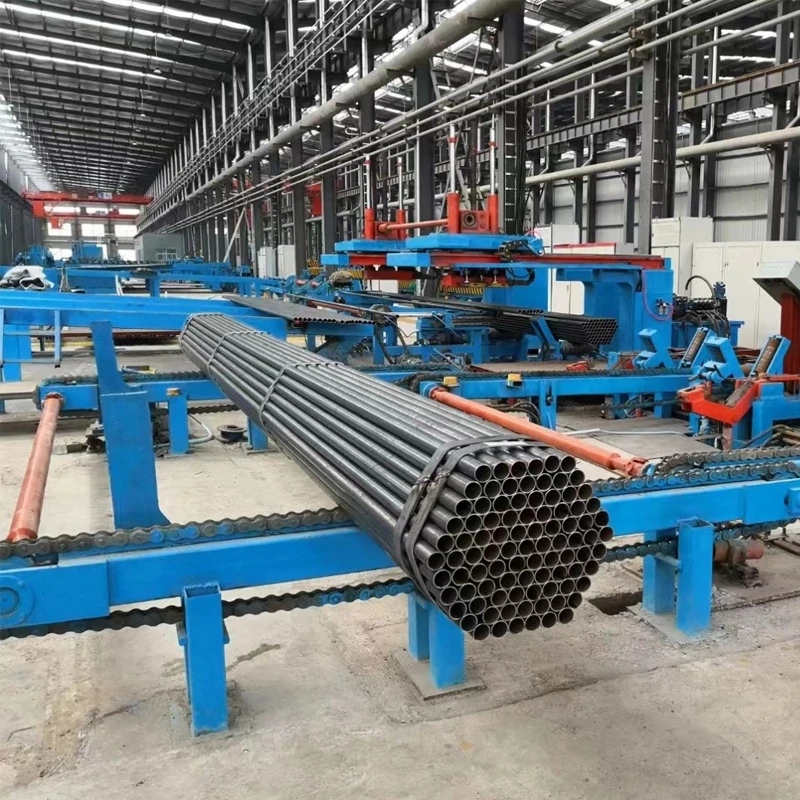
The braking component of a combination machine introduces the art of bending metal. Expertise in this area includes an understanding of varying bend angles and techniques, essential for creating desired shapes with minimal error. The brake function requires meticulous adjustment of the machine’s clamping systems and bending restraints to achieve uniform results. This not only demonstrates the operator’s expert-handling capabilities but also enhances the trustworthiness of their craft, as each bent piece emanates precision and consistency.
jet combination shear brake and roll
Rolling, the third core function, allows operators to produce cylindrical and other curved geometries from flat sheets. This requires a sound understanding of roll adjustment mechanisms and material properties, as different metals respond uniquely to pressure and manipulation. Operators demonstrating proficiency in predicting and compensating for spring-back and other material behaviors establish themselves as authoritative figures capable of crafting intricate designs that blend both form and function.
Trustworthiness in the operation of these machines is also garnered through proper maintenance practices. Regular inspection and upkeep of blades, clamping systems, and roll mechanisms prevent disruptions in operations and safeguard the quality of output. Expert operators not only focus on immediate project requirements but also ensure their tools are calibrated and functioning optimally, guaranteeing long-term fidelity and reliability for their clientele.
Manufacturers of jet combination shear, brake, and roll machines must provide detailed instructional materials and user support to foster a comprehensive understanding of machine functionalities. This enhances the user's experience, enabling them to harness the full potential of the toolset provided. Quality customer support fortifies the manufacturer's authoritative status, fostering trust amongst professionals and hobbyists alike. An informed user is more capable of maximizing machine capabilities, translating to superior craftsmanship and production quality.
In conclusion,
the journey to mastering a jet combination shear, brake, and roll machine is one of continuous learning and adaptation. It hinges on acquiring technical knowledge, attention to detail, and a commitment to maintaining equipment integrity. These aspects are not merely beneficial; they are essential for maintaining expertise and trustworthiness in metalworking. Through prudent selection, adept handling, and diligent maintenance, these machines become more than just tools; they transform into keystones of innovation and authority in metal fabrication enterprises.