The intricate art of metal rolling, an essential facet of the manufacturing process, enhances the versatility and quality of metal products. Metal rolling mills stand at the heart of this transformation, turning raw metal blocks into precision-shaped parts and components that drive industries from aerospace to construction. Understanding the importance of this process is crucial for stakeholders in industrial domains who aim to leverage its benefits for competitive advantage.
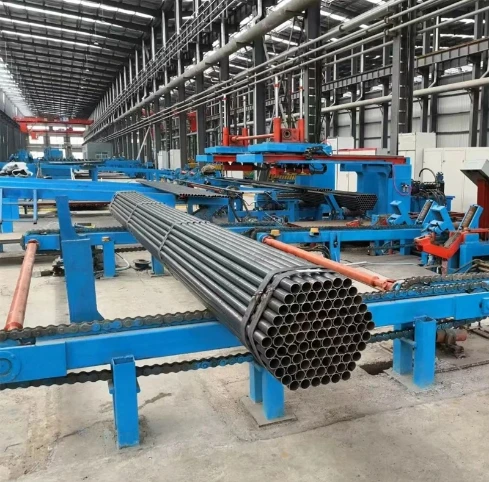
In a metal rolling mill, large sections of raw metal, often heated to high temperatures, undergo successive stages of compression through rollers. These enormous machines demand expertise not merely for operational efficiency but also to ensure seamless integration with existing industrial setups. The fundamental principle in metal rolling involves reducing the thickness of the material while maintaining its structural integrity—a delicate balance between force and finesse.
A well-maintained metal rolling mill is crucial for optimizing production outputs and enhancing the lifespan of the equipment. Regular calibration and sensitive monitoring are paramount as even minor deviations can lead to material inconsistencies. Industry professionals with extensive experience in managing these mills emphasize consistent performance checks and timely maintenance as pillars for operational success.
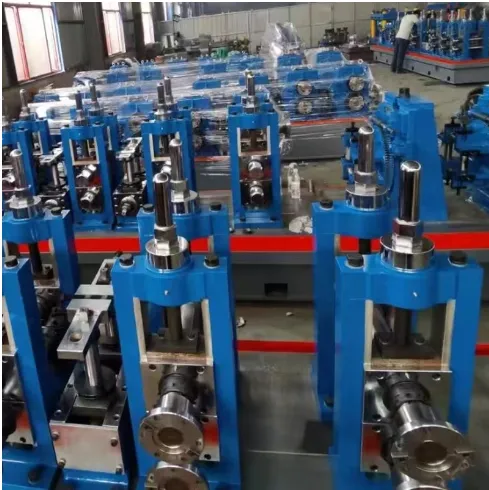
The role of a metal rolling mill extends far beyond mere reduction in thickness. It shapes the metal to meet exact specifications, improving its mechanical properties and eliminating defects such as porosity and inclusions. Advanced mills employ computer-controlled processes to achieve higher precision, thereby enhancing the quality and performance of the final products. This makes it indispensable for producing high-grade components required in demanding sectors such as automotive and aviation.
Noteworthy in the modern landscape is the drive towards eco-friendly operations. Metal rolling, due to its energy-intensive nature, faces scrutiny under environmental norms. However, technological advances have significantly reduced the ecological footprint of these processes. Innovative cooling and lubrication systems enhance efficiency and minimize waste, while the integration of renewable resources in powering these mills marks a significant stride towards sustainability.
metal rolling mill
The drive for innovation encourages a continuous evolution in metal rolling mill technologies. Experts in the field are increasingly focusing on digital twins—virtual models that replicate the physical production lines in real-time. This synergy of actual and virtual processes allows manufacturers to predict and rectify issues before they manifest, optimizing resource usage and reducing the need for costly interventions.
An authoritative foundation in metallurgy and engineering remains imperative for those involved in metal rolling operations. Professionals in this field contribute not just through expertise but through an authoritative approach that translates operational know-how into practical implications for product design and industrial standards. Their role ensures that product outcomes not only conform to existing standards but often exceed them, contributing to the advancement of manufacturing practices.
Safety remains a backbone of trust within metal rolling procedures. The high temperatures and colossal forces at play necessitate a rigorous focus on the safety of personnel and infrastructure. Implementation of state-of-the-art safety measures and consistent training underscore the commitment to trustworthiness, ensuring an accident-free environment. This trust extends to clients and stakeholders, underpinning long-term relationships built on reliability and quality assurance.
In conclusion, the significance of metal rolling mills transcends their primary function of shaping metal. They represent a confluence of engineering excellence, technological innovation, sustainability practices, and rigorous safety standards. As industry demands grow in complexity, these mills embody the adaptability and precision required to meet tomorrow's challenges. As experts continue to push boundaries, the future of metal rolling promises not just efficiency, but a holistic integration of technology and sustainability paving the way for progressive industrial practices.