A metal tube cutting machine is an essential tool in various industries, from automotive and aviation to construction and manufacturing. These machines have become increasingly sophisticated, incorporating advanced technology to improve efficiency, accuracy, and safety in metal cutting processes. For businesses looking to invest in a metal tube cutting machine, understanding the capabilities and specifications of different models is crucial. This article provides expert insights into selecting and maximizing the use of metal tube cutting machines, ensuring you get the best value for your investment.
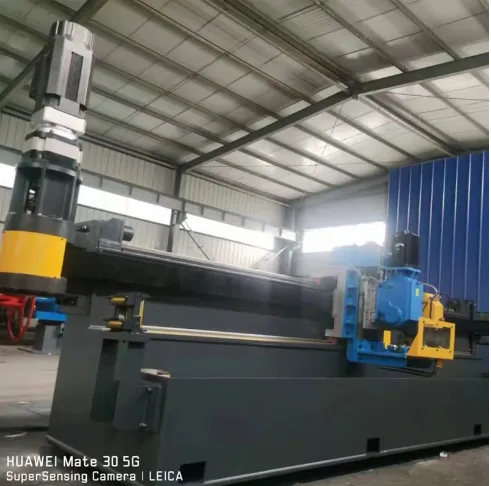
High Precision and Efficiency One of the primary benefits of modern metal tube cutting machines is their ability to deliver high precision cuts consistently. Equipped with CNC (Computer Numerical Control) technology, these machines can execute complex patterns and designs with minimal manual intervention, significantly reducing the margin for error. The precision offered by these machines ensures that every cut is exact, minimizing waste and optimizing material usage—a significant advantage in cost efficiency and resource management for any manufacturing process.
Advanced Technology Integration Today's metal tube cutting machines come integrated with cutting-edge technology, such as laser cutting, plasma cutting, and waterjet cutting. Each of these technologies offers distinct advantages depending on the material and the specific requirements of the project. Laser cutting, for instance, is known for its high precision and speed, making it perfect for delicate or intricate designs. Plasma cutting is ideal for thicker metal tubes where speed is a priority, while waterjet cutting offers versatility, capable of cutting through metal without compromising structural integrity by avoiding heat deformation.
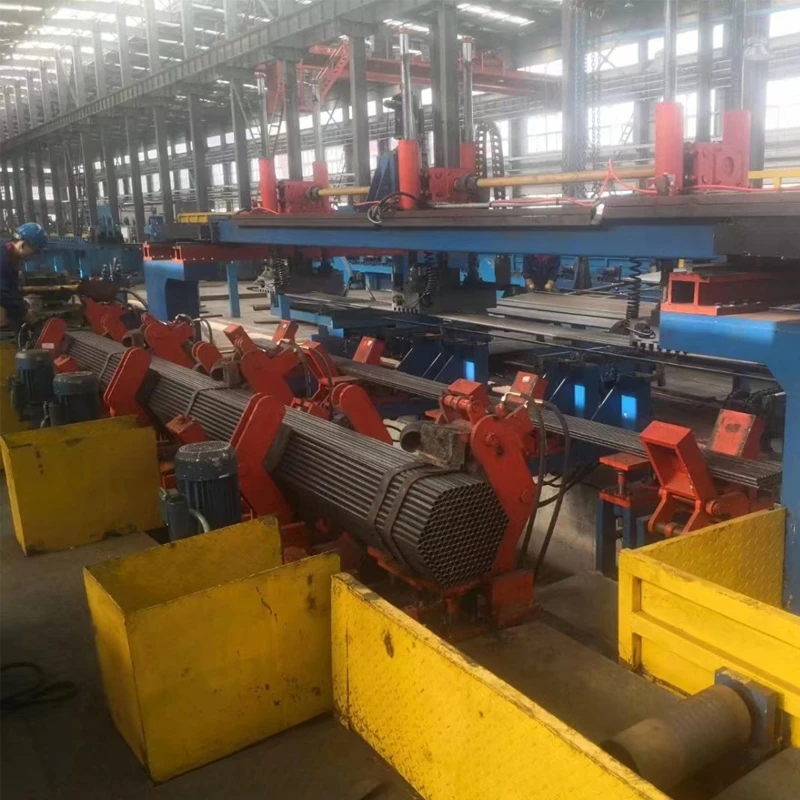
Durability and Longevity Investing in a durable metal tube cutting machine ensures long-term operational reliability. High-quality machines made from robust materials can withstand rigorous use and harsh industrial environments. Manufacturers often offer warranties and are open for annual maintenance contracts to ensure that the machines operate at optimal efficiency over the years. A properly maintained machine reduces downtime, thereby increasing productivity and profitability for businesses relying heavily on timely project delivery.
Safety and User-Friendliness Safety is paramount in any industrial setup, and metal tube cutting machines are designed with features that prioritize the well-being of the operator. Automatic shut-off systems, safety shields, and user-friendly interfaces are incorporated to minimize the risk of accidents. In addition to built-in safety mechanisms, manufacturers often provide comprehensive training for operators, ensuring that the workforce is well-versed in handling the equipment safely.
metal tube cutting machine
Cost Considerations and ROI The initial cost of a metal tube cutting machine can be substantial, but the long-term return on investment (ROI) makes it worthwhile for businesses engaged in regular metal fabrication. By improving overall efficiency, reducing material wastage, and enhancing the quality of the finished product, these machines enable businesses to meet client demands promptly and effectively. Additionally, the versatility of these machines allows companies to expand their service offerings, potentially opening up new revenue streams.
Environmental Considerations In an era where sustainability is a key business consideration, metal tube cutting machines are designed to minimize environmental impact. Technologies like laser cutting and waterjet cutting are energy-efficient and produce minimal waste, aligning with green manufacturing practices. Companies that prioritize such technologies can enhance their sustainability credentials, appealing to environmentally-conscious clients and stakeholders.
Customization and Scalability Metal tube cutting machines offer a high degree of customization, allowing businesses to tailor them according to their specific needs. Whether it's adjusting the machine's software to handle different materials or incorporating additional features for specific production requirements, customization ensures that the machine grows with the business. This scalability is particularly advantageous for small to medium enterprises experiencing growth, as it allows them to expand their capabilities without significant additional investment.
In conclusion, choosing the right metal tube cutting machine involves careful consideration of various factors including precision, technology integration, durability, and cost-effectiveness. By prioritizing these elements and selecting a machine that aligns with your specific production needs, you can enhance operational efficiency, ensure safety, and achieve significant long-term savings. As the industry continues to evolve with technological advancements, staying informed and adaptable is key to maintaining a competitive edge in the metal fabrication marketplace.