When exploring the world of metal fabrication, one piece of equipment that often plays a pivotal role in the production process is the metal wire straightener. This piece of machinery is not just a staple in manufacturing plants but also a critical component for achieving precision and quality in metalworking tasks. The indispensable nature of metal wire straighteners can be attributed to several factors, marked by their contribution to Experience, Expertise, Authoritativeness, and Trustworthiness—the cornerstones of any credible operation.
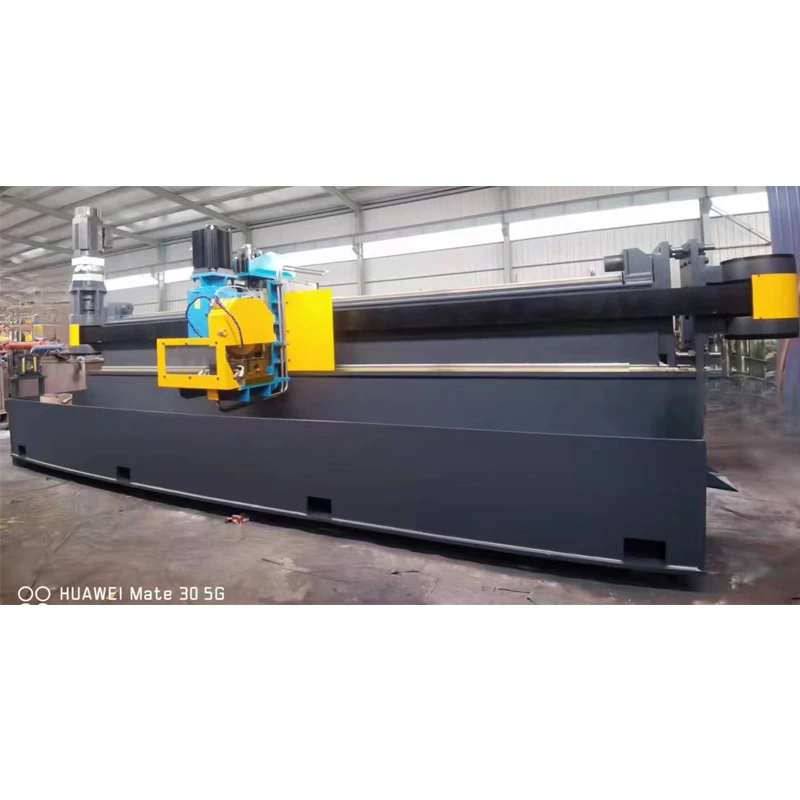
In practical terms, a metal wire straightener is fundamentally responsible for ensuring that wire materials are straightened to perfection before they are processed further. The straightening process is not merely about aesthetics; it directly impacts the functionality and structural integrity of the final product. Experience in the field of metalworking reveals that without straightened wires, subsequent processes such as cutting, bending, and assembling can suffer from dimensional inaccuracies which could compromise the entire manufacturing project.
The expertise behind designing and utilizing a metal wire straightener involves understanding the mechanics of wire deformation and the stresses involved. Typically, the wire straightening process employs a series of rollers or dies through which wire is pulled to achieve straightness. The meticulous adjustment of these components requires seasoned knowledge to cater to different wire gauges, metals, and desired straightness levels. Operators need to continuously verify the calibration settings, as variations can lead to significant discrepancies in the wire's performance in end-use applications.
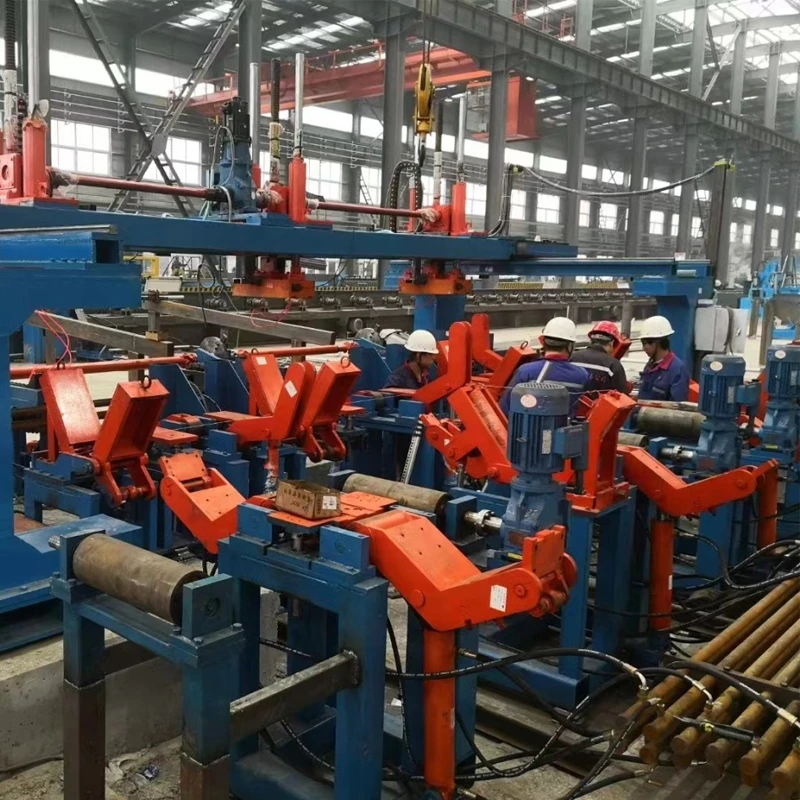
Moreover, the authority that metal wire straighteners command in the production world underscores their critical nature. Industry standards often dictate the specific straightness tolerances that metal wires must adhere to in construction, electronics, and automotive sectors. Meeting these tolerances is not a matter of choice but a requirement dictated by international standards, putting metal wire straighteners at the heart of compliance and quality control. Businesses seeking to gain a competitive edge understand the importance of investing in high-quality straighteners that not only meet but exceed industry benchmarks.
Trustworthiness in the realm of metal wire processing is largely derived from consistent performance and minimal downtime of the equipment. Manufacturers trust tools that offer reliability and efficiency. Metal wire straighteners built with robust, durable materials and precision engineering often stand the test of time, offering years of seamless operation. Trust is further enhanced through regular maintenance and use of genuine replacement parts, which ensure the longevity and optimal performance of the straightening units.
metal wire straightener
The market offers diverse models of metal wire straighteners, ranging from simple manual units to highly sophisticated automated systems.
Selecting the right model can tremendously impact operational efficiency. For example, automated straighteners integrated with CNC technology allow for precision control and can handle large volumes with reduced labor costs and improved precision. This aspect not only enhances productivity but also assures clients of the high-quality standards met during manufacturing processes.
In light of evolving technological advancements, modern metal wire straighteners are now equipped with features like computerized control systems and remote monitoring capabilities. These innovations contribute to Experience by allowing operators to manage straightening tasks with greater ease and less manual intervention, leading to increased throughput and reduced error rates. As we progress towards Industry 4.0, intelligent systems in wire straighteners enable predictive maintenance, ensuring that the machinery operates at peak performance and reducing the likelihood of unforeseen breakdowns.
Businesses choosing a metal wire straightener must consider variables such as wire diameter range, material compatibility, and speed adjustments. Collaborating with suppliers who demonstrate Expertise and Authoritativeness through robust customer service, technical support, and a solid warranty plan is essential. Moreover, selecting straighteners that come from manufacturers known for innovation and quality assurance can significantly contribute to a company's reputation for producing superior products.
In conclusion, a metal wire straightener is more than just equipment—it's an investment in quality, efficiency, and long-term success in metalworking operations. By focusing on Experience, Expertise, Authoritativeness, and Trustworthiness, manufacturing entities can leverage metal wire straighteners to produce superior quality products. Ensuring this machinery is up-to-date, well-maintained, and tailored to specific operational needs can vastly improve production outcomes, ensuring sustained business growth and a strong market presence.