Navigating the world of manufacturing requires a keen understanding of plastic injection molders, a pivotal component in the production of durable and reliable plastic parts. These molders serve as the backbone for industries ranging from automotive to consumer electronics, ensuring precision, consistency, and cost-effectiveness in high-volume production.
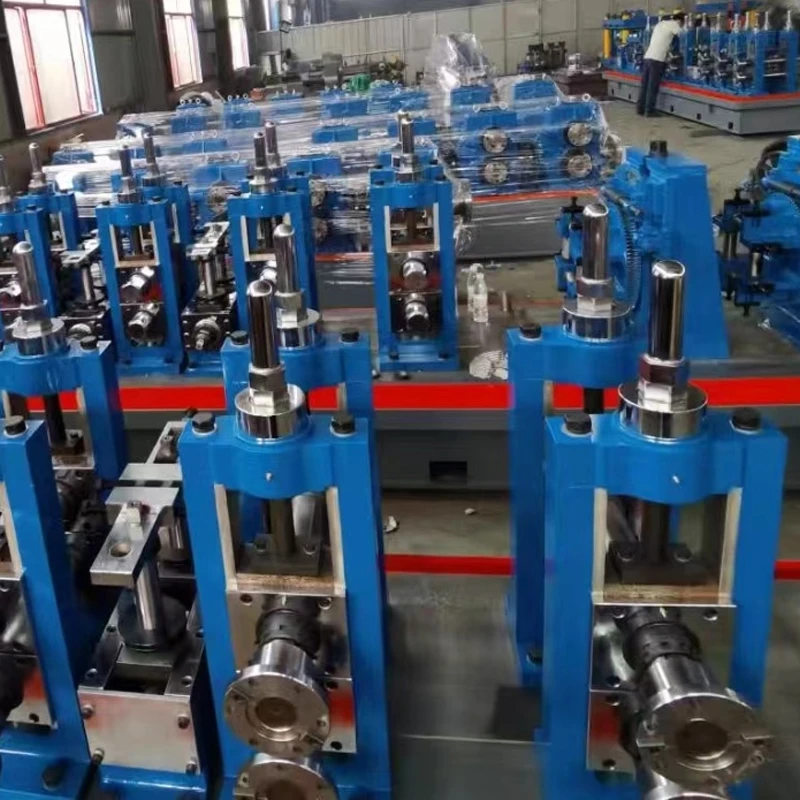
A seasoned engineer in the field of manufacturing will testify to the critical role played by plastic injection molders in streamlining operations. Their ability to produce complex shapes with impeccable accuracy makes them indispensable. With advancements geared towards efficiency and sustainability, injection molding technology has evolved significantly, ensuring that businesses stay competitive and environmentally responsible.
From an expert perspective, the process starts with the selection of materials, which varies depending on the desired properties of the final product. Typically,
thermoplastics are used for their versatility and recyclability. The molder must possess an in-depth understanding of material behavior, especially under varying temperatures and pressures. This expertise ensures that the end products meet stringent industry standards and customer specifications.
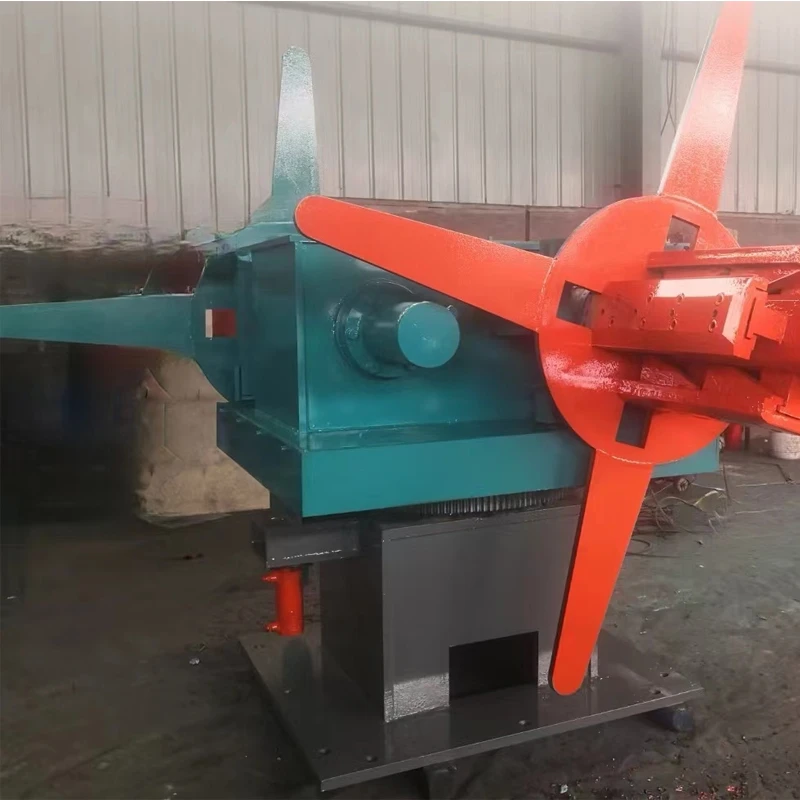
Expertise in tooling design is another area where plastic injection molders need to excel. The design of the mold impacts not only the quality of the product but also the efficiency of the manufacturing process. By leveraging advanced software tools, mold designers can simulate and optimize the injection molding process, predicting potential issues and rectifying them before the production begins. This proactive approach minimizes waste and reduces downtime, contributing to sustainable manufacturing practices.
plastic injection molders
The authority of plastic injection molders is further established by their commitment to innovation. Many leading manufacturers invest heavily in research and development to stay ahead of the curve. Innovations such as multi-material injection molding and micro-injection molding have opened new avenues for creating more complex and functional parts. Additionally, the integration of automation and real-time monitoring systems has enhanced the precision of the molding process, allowing for continuous improvement and adaptability to changing market demands.
Trustworthiness in plastic injection molders is built on a track record of delivering consistent quality and performance. Reputable molders adhere to international quality standards, such as ISO certifications, which provide assurance of their capabilities and dedication to quality control. Moreover, their focus on client collaboration throughout the design and production phases ensures that client needs are met with precision and adaptability, further building trust and long-term partnerships.
The journey of plastic injection molders from raw material selection to the finished product underscores a commitment to excellence and innovation. By combining expert knowledge, cutting-edge technology, and robust processes, they bridge the gap between conceptual ideas and tangible products. The forward-thinking approach adopted by industry leaders ensures that the benefits of plastic injection molding—such as efficiency, cost-effectiveness, and sustainability—are maximized for various applications across different sectors.
In conclusion, the impact of plastic injection molders extends beyond the manufacturing of plastic parts. These molders exemplify a blend of engineering expertise and technological innovation, essential for the modern world's demands. Their continued evolution and dedication to quality make them a trusted partner in manufacturing, offering solutions that meet the challenges of today and anticipate the needs of tomorrow. Businesses seeking to optimize their production processes should recognize the integral role of proficient plastic injection molders in achieving operational success.