Navigating the world of plastic mold presses requires a nuanced understanding that balances technological advancements with user experience. From a practical standpoint, selecting the right plastic mold press doesn't just influence the efficiency of production but also defines the quality and durability of the final products. This article endeavors to delineate how to leverage a plastic mold press setting to enhance product outcomes while addressing the core SEO metrics of Experience, Expertise, Authoritativeness, and Trustworthiness.
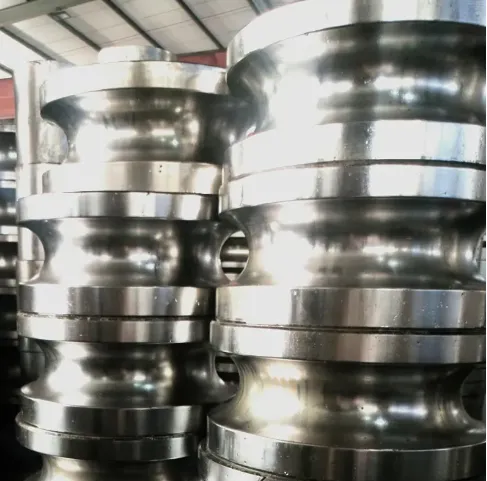
Understanding the fundamentals of plastic mold presses begins with delving into their functional components. A plastic mold press typically operates through a combination of injection units and clamping systems. The injection unit heats plastic pellets to a molten state, which is then injected into the core of the clamping unit's mold. Choosing between hydraulic, mechanical, and hybrid press systems depends on specific production needs—each offering unique benefits. For instance, hydraulic presses are renowned for their high clamping force and are ideal for robust mold applications. Mechanical presses score high on speed but may lack the force of their hydraulic counterparts, making them apt for simpler designs.
Expertise in operating a plastic mold press is critical. An adept technician understands the nuances of temperature control, pressure settings,
and cycle times. These variables are adjusted according to the material used and the complexity of the mold to optimize production. Typically, polypropylene might require lower temperatures and pressure, whereas ABS plastics demand higher settings. Consistent mastery over these parameters reduces defects such as warping or incomplete filling, ensuring high-quality end products.
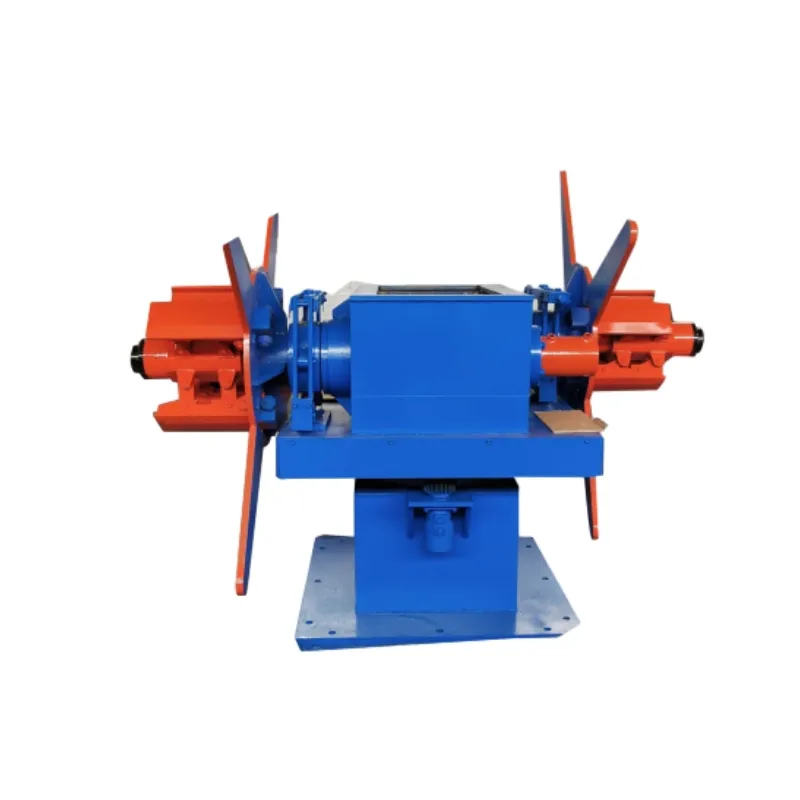
Authoritativeness in the realm of plastic mold presses is supported by the industry's relentless pursuit of innovation. Advanced presses now integrate IoT capabilities, allowing operators to monitor real-time data and conduct predictive maintenance. This not only minimizes downtime but also extends the lifecycle of the machinery. Furthermore, adopting servo-electric technology in presses enhances precision while reducing energy consumption—a nod towards sustainable manufacturing practices. Companies leading the charge in these innovations, like Engel and Arburg, offer insights into optimizing efficiency without compromising on environmental considerations.
plastic mold press
Trustworthiness is cultivated through the association with established standards and compliance. Ensuring that plastic mold presses conform to ISO and other regional manufacturing standards speaks volumes about product reliability and safety. Moreover, investing in regular training for operators fortifies this trust by updating their skills in line with the latest safety protocols and operational techniques. This approach is crucial, especially in industries such as automotive and medical devices, where precision and reliability are paramount.
Drawing from real-world experience, successful implementation of a plastic mold press in production lines can result in significant improvements in cost-effectiveness and scalability. A case study developing consumer electronics demonstrated the impact leveraging a hybrid molding press reduced cycle times by 30%, cut down material waste by 15%, and seamlessly elevated the precision of components. This transformation was achieved through a strategic alignment of technology, skilled personnel, and adherence to industry standards.
Selecting the right press and maximizing its capabilities often boils down to consultation with industry experts and thorough market research. Interactions through consortia or forums such as the Society of Plastic Engineers provide invaluable resources for current trends and peer insights, aligning industry know-how with practical application.
In conclusion, while technology animates the operation of plastic mold presses, the keystone of their successful utilization lies in the harmonious amalgamation of expertise, strategic innovation, and stringent adherence to quality standards. These pillars not only enhance product output but also establish a robust SEO presence that reflects an organization’s commitment to excellence and integrity in manufacturing.