In the realm of modern manufacturing, the plastic pipe making machine stands as a cornerstone technology, pivotal for multiple industries ranging from construction to plumbing. These machines are not only essential for the production of a wide array of piping solutions but are also instrumental in creating products that meet rigorous standards for quality and durability. Achieving excellence in this field requires a deep understanding of the machinery, materials, and processes involved.
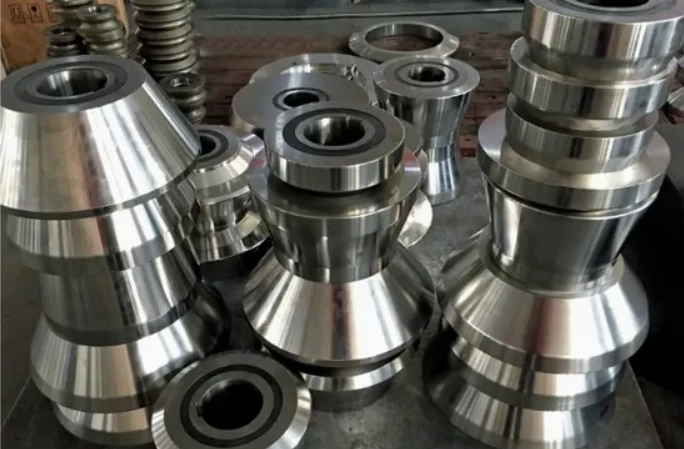
A plastic pipe making machine operates through a complex yet fascinating mechanism known as extrusion. At its core, the extrusion process involves raw plastic materials, usually in pellet form, which are fed into a hopper. The material is then gradually melted and pushed through a mould or die that shapes it into continuous pipe. The expertise required to manage this process lies in precise temperature control, speed of extrusion, and the quality of the die used – all critical to ensuring consistent wall thickness and strength.
For manufacturers, one of the primary advantages of these machines is their versatility.
They can produce pipes of varying diameters and lengths, which accommodates a multitude of applications. Furthermore, machines equipped with advanced features such as semi-automatic or fully automatic operation enhance productivity and precision, reducing human error and waste. These machines are designed to work with various plastic compounds, such as PVC, PE, and PP, each offering specific benefits depending on the application needs.
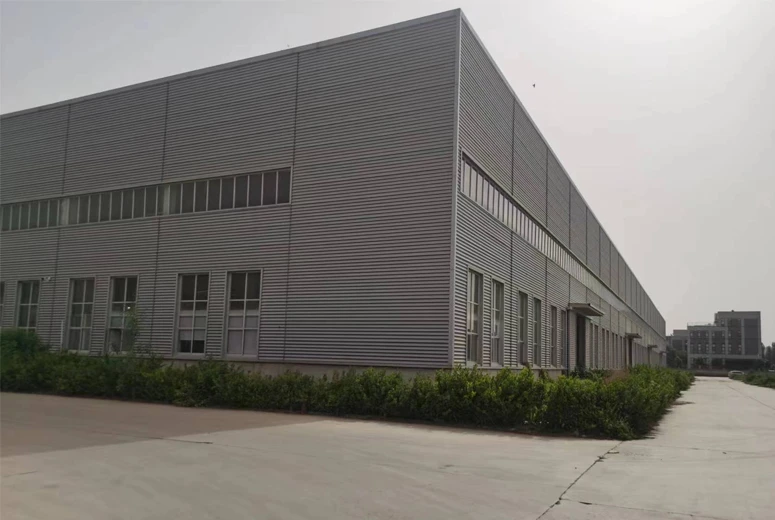
Experience shows that investing in a high-quality plastic pipe making machine yields long-term benefits. Industries we've observed leveraging these machines successfully often prioritize machines that allow quick changeover between different product specifications, thereby minimizing downtime and maximizing throughput. The expertise in selecting the right machine involves understanding customer needs, evaluating throughput capabilities, and ensuring compatibility with existing production lines.
plastic pipe making machine
From an authoritative standpoint, mastering the nuances of a plastic pipe making machine's operation is crucial for maintaining competitive advantage. Certified training for operators, continuous maintenance schedules, and consistent evaluation against industry standards all contribute to optimal performance. Trustworthiness in this domain is established through adherence to ISO standards, which ensure that both the manufacturing process and the materials used are compliant with international safety and quality benchmarks.
From a consumer’s perspective, the trustworthiness of the products manufactured by these machines is paramount. Pipes produced by reputable machines are known for their durability, resistance to corrosion and chemicals, and easy installation, making them reliable for both residential and commercial use. These aspects are critical, as failure in piping products can lead to costly repairs and safety hazards. Thus, manufacturers certified in ISO standards and recognised by industry bodies like ASTM and EN gain customer confidence due to their proven reliability.
In recent years, innovations in this field have focused heavily on sustainability. Machines that are energy-efficient and capable of using recycled materials are highly sought after. Industry leaders understand that while output quality is non-negotiable, adopting environmentally friendly practices is crucial for long-term success and meeting regulatory requirements. Incorporating green technology not only reduces the environmental footprint but also appeals to a growing demographic of eco-conscious consumers.
In essence, the plastic pipe making machine is a testament to modern industrial capability – blending engineering expertise with advanced technology to deliver high-performance and reliable products. Whether upgrading an existing production line or establishing a new facility, selecting the right machine is a critical decision that impacts quality, efficiency, and market competitiveness. A comprehensive understanding of these factors, coupled with a commitment to ongoing learning and adherence to best practices, ensures that manufacturers can meet the evolving demands of the industry while maintaining the highest standards of quality and safety.