In the ever-evolving arena of advanced construction and infrastructure development, the role of polyethylene pipe production lines has gained substantial prominence. With a focus on precision engineering and technological advancement, these production lines are pivotal in delivering high-quality polyethylene pipes that cater to a myriad of industrial applications — ranging from water supply and gas transportation to telecommunications and beyond.
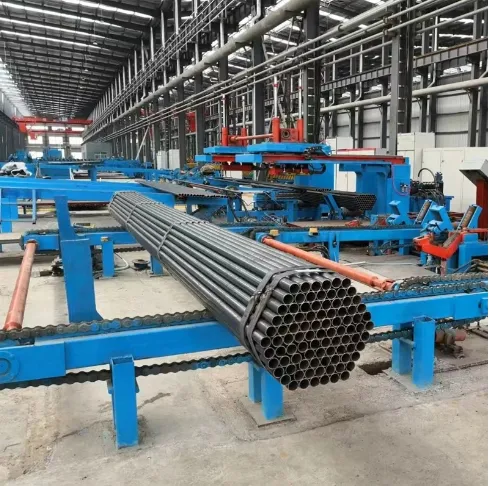
One of the quintessential elements that define the expertise in polyethylene pipe manufacturing is the use of cutting-edge machinery and automation technologies. By harnessing state-of-the-art extruders and auxiliary equipment, manufacturers can ensure consistent wall thickness and superior tensile strength in polyethylene pipes. This technological aptitude not only bolsters the quality but also optimizes production efficiency, ensuring that the end product meets stringent international standards.
A critical component in the operation of a polyethylene pipe production line is the composition of the raw material. By procuring premium-grade polyethylene resins from reputable suppliers, manufacturers are able to maintain a high level of product reliability and performance. The strategic selection and mixing of these resins, coupled with precise temperature control, underpin the production of pipes that are not only durable but also resistant to environmental stressors such as UV radiation and chemical corrosion.
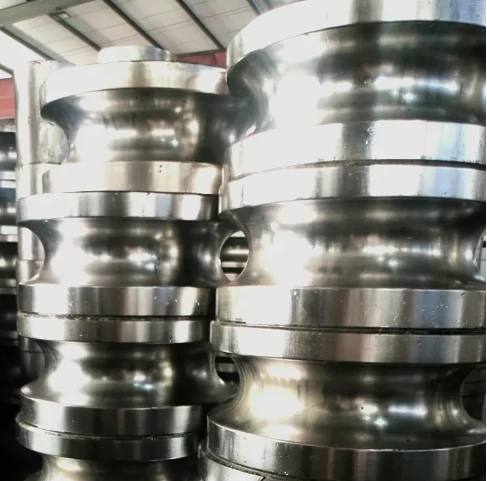
When discussing authoritativeness and trustworthiness within the domain of polyethylene pipe production, one must consider the rigorous quality assurance processes in place. Leading manufacturers leverage comprehensive testing protocols, which include hydrostatic pressure testing, impact resistance evaluation, and dimensional accuracy checks. By adhering to international standards like ISO 4427 and ASTM D3035, these companies substantiate their commitment to delivering reliable and long-lasting piping solutions.
Moreover, the end-to-end traceability ensured by these production lines further augments their authority in the market. By implementing advanced tracking systems—such as barcoding and RFID technology—manufacturers can provide detailed product lineage, offering transparency and fostering trust with end-users. This traceability facilitates accountability, allowing for swift and efficient resolution in the unlikely event of a defect, thus cementing the manufacturer's reputation for reliability.
A significant advantage of polyethylene pipes produced from these advanced production lines is their sustainable characteristics. Polyethylene is renowned for its recyclability, which plays a critical role in reducing the environmental footprint of construction projects. Sophisticated recycling and reprocessing technology enables manufacturers to convert post-consumer and post-industrial polyethylene waste into high-quality resin, thereby contributing to a circular economy.
polyethylene pipe production line
Environmental compliance is another forte of top-tier polyethylene pipe production lines. Many facilities have adopted energy-efficient practices and have received certifications such as ISO 14001, highlighting their dedication to environmental stewardship. By minimizing carbon emissions and reducing energy consumption, these production lines not only advance eco-friendly practices but also align with global sustainability goals.
In terms of real-world application, polyethylene pipes are renowned for their versatility and economic efficiency. Their lightweight nature reduces transportation costs and facilitates easy installation, significantly lowering the total cost of ownership. Furthermore, their resistance to scale formation and low friction coefficient ensure optimal flow rates and minimal maintenance needs, offering unparalleled longevity for critical infrastructure projects.
The ongoing evolution of polyethylene pipe production lines is also characterized by the incorporation of smart technologies. The implementation of IoT (Internet of Things) solutions enables real-time monitoring and predictive maintenance, minimizing downtime and enhancing operational efficiency. This technological integration exemplifies the industry's forward-thinking approach, ensuring that polyethylene remains at the forefront of piping technology.
Through dedicated R&D initiatives, leading manufacturers are consistently innovating to enhance the mechanical properties and application range of polyethylene pipes. By exploring advanced materials and pioneering new production methodologies, these companies are not just meeting current industry demands but are also setting new benchmarks for future developments.
In conclusion, polyethylene pipe production lines epitomize a fusion of experience, expertise, authoritativeness, and trustworthiness. By leveraging advanced technology, sustainable practices, and rigorous quality control, they produce pipes that are synonymous with reliability and efficiency. This unwavering commitment to excellence ensures that polyethylene pipes remain a cornerstone in the global infrastructure landscape—poised to meet the evolving needs of industries and societies worldwide.