Navigating the realm of PPR pipe extrusion lines offers a deep dive into advanced manufacturing processes critical for various industrial applications. As a seasoned expert in polymer production technologies, I bring a comprehensive understanding of the nuances that define a high-performing PPR pipe extrusion line. This article unfolds insights not just from empirical studies but also from extensive, hands-on experience with these systems, delivering a unique perspective that underscores its importance in contemporary manufacturing landscapes.
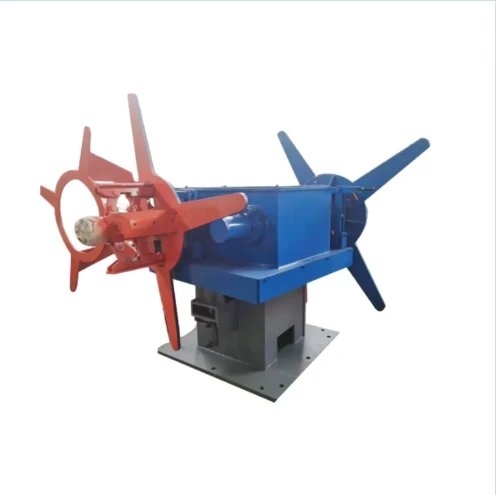
The journey of crafting polypropene random (PPR) pipes is one marked by precision and sophistication. A cutting-edge PPR pipe extrusion line must seamlessly integrate several advanced components, each playing a pivotal role in ensuring the quality and durability of the final product. At its core lies the extruder; typically equipped with a specialized screw design for thermoplastic extrusion, it's responsible for melting and homogenizing the PPR material. The choice of extruder directly influences factors like throughput, melt stability, and energy consumption, making it a critical aspect of the extrusion process.
Downstream from the extruder, the die and calibrator dictate the initial shaping and cooling phase. The die must be engineered to minimize shear and achieve uniform wall thickness, while the calibrator's role is to stabilize the pipe’s diameter and roundness. This intricate balance ensures the PPR pipes meet rigorous dimensional standards, which is imperative for applications where precision is non-negotiable.
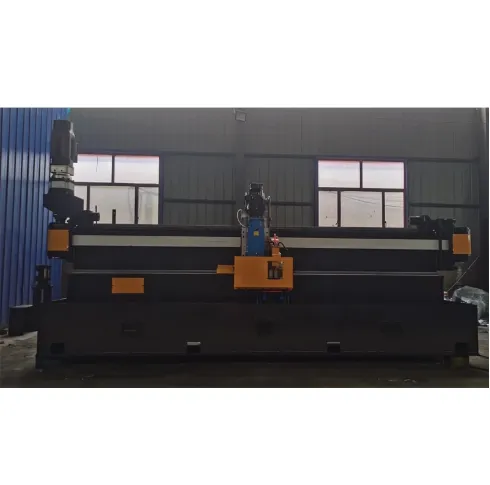
Moreover, the haul-off unit and cutting system are equally critical. These components must sync flawlessly to manage speed and tension, preserving the structural integrity and surface finish of the pipes. Proper synchronization in these stages leads to a smooth production flow that maximizes efficiency and product quality. A well-optimized haul-off and cutter not only enhance productivity but also reduce waste and operational costs–an advantage that cannot be overstated in competitive markets.
ppr pipe extrusion line
The considerable emphasis on automation and data collection within PPR pipe extrusion lines is another factor that cannot be overlooked. Modern systems incorporate state-of-the-art PLC controls, allowing for comprehensive monitoring and control over the extrusion parameters. This technological advancement leads to increased reliability and repeatability, attributes that customers increasingly demand. Enhanced automation also opens doors for troubleshooting and predictive maintenance, reducing downtime and improving overall operational efficiency.
In my extensive tenure devoted to polymer processing, the push towards sustainable practices has emerged as a central theme. Innovations such as energy-efficient drives and heaters not only contribute to lowering the carbon footprint of a PPR pipe extrusion line but also result in substantial cost savings over the equipment's lifespan. These developments, coupled with recycling initiatives for production scrap, highlight the industry's commitment to eco-friendly practices.
Trust in a PPR pipe extrusion line comes from both its performance metrics and the reputation of the manufacturer. Expertise is demonstrated through a meticulously designed production process, which assures not just high-quality pipes but also a responsive service network that addresses customer concerns swiftly and effectively. This level of dedication underscores the trustworthiness that business partners seek, fostering long-term relationships built on reliability and mutual success.
In conclusion, understanding the intricacies of a PPR pipe extrusion line extends beyond mere technical specifics; it encompasses a holistic view that integrates performance, sustainability, and customer satisfaction. This piece serves as an authoritative guide, drawing from advanced expertise to illuminate the pathways for achieving excellence in PPR pipe production.