Punch and shear machines are indispensable tools in the metalworking industry, providing precise and efficient fabrication solutions. For those looking to purchase a punch and shear machine, understanding the intricacies of these complex devices can be both a rewarding and essential journey. This article delves into the vital aspects of purchasing a punch and shear machine, offering an authoritative guide rooted in real-world expertise and experience.
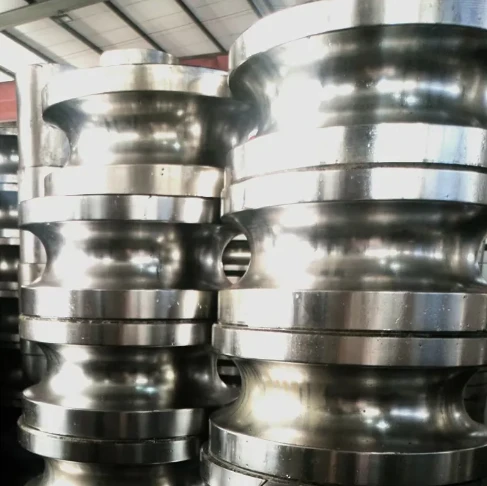
Punch and shear machines, commonly referred to as ironworkers, are multifaceted devices used to punch holes and shear metal sheets. These machines are beloved for their versatility and are ideal for manufacturing industries where precision, speed, and efficiency are paramount. Whether you are running a small workshop or a large industrial operation, selecting the right punch and shear machine is critical to optimizing your production processes.
When considering a purchase, one must first evaluate the specific needs of their operation. Not all punch and shear machines are created equal; they vary significantly in terms of capacity, size, and functionality. A thorough assessment of the materials being worked on, including thickness and type, alongside the anticipated volume of work, ensures that the machine aligns perfectly with operational goals.
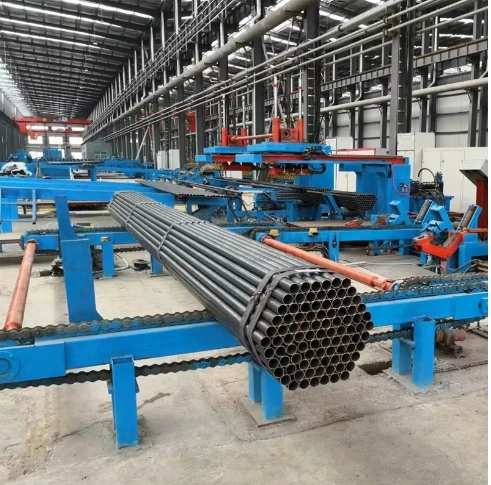
The expertise of the manufacturer is a crucial factor. Opting for a machine from a reputable company known for innovation and reliability can significantly impact the longevity and efficiency of the equipment. Companies that offer comprehensive support, including training and maintenance services, amplify the trustworthiness of the purchase, providing assurance that any operational hiccups can be swiftly addressed.
A sound investment is also contingent on the machine's safety features.
Reliable punch and shear machines are equipped with advanced safety mechanisms to protect operators. Look for features like emergency stops, protective guards, and intuitive control panels that not only enhance safety but also improve the user experience. Machines designed with operator ergonomics in mind can significantly reduce fatigue and increase productivity.
punch and shear machine for sale
The machines' adaptability to future technological advancements is another consideration. In the evolving landscape of metalworking, where digital integration and automation are becoming increasingly prevalent, selecting a machine that can be updated or adapted to future technologies can provide long-term value. Features such as programmable controllers or integration with fabrication software not only future-proof your investment but can also result in substantial efficiency gains.
Another critical factor is conducting a cost-benefit analysis. While upfront costs are a primary concern, the total cost of ownership, including maintenance, operational efficiency, and energy consumption, should not be overlooked. Machines that offer superior energy efficiency, lower maintenance requirements, and higher durability often translate to significant cost savings over their operational lifespan.
Consulting with industry peers and tapping into professional networks can also provide deeper insights and practical knowledge about specific punch and shear machines. Real-world testimonials and case studies add layers of credibility and trustworthiness to the decision-making process, offering invaluable perspectives that cannot be gleaned from manufacturer specifications alone.
In conclusion, acquiring a punch and shear machine is a significant investment that demands careful analysis and understanding. By focusing on the specific needs of your operation, evaluating the credibility of manufacturers, ensuring robust safety measures, considering adaptability, and conducting thorough cost analyses, you can secure a piece of equipment that not only meets but exceeds your operational expectations. This informed approach not only guarantees superior performance and productivity but also stands as a testament to the strategic acumen and professional expertise integral to thriving in the metalworking industry.