Roll forming rollers are crucial components in the roll forming industry, facilitating the production of a myriad of metal components with precision and efficiency. This article delves into the vital role of roll forming rollers, underscoring their importance, applications, and the factors that contribute to their effectiveness in industrial settings.
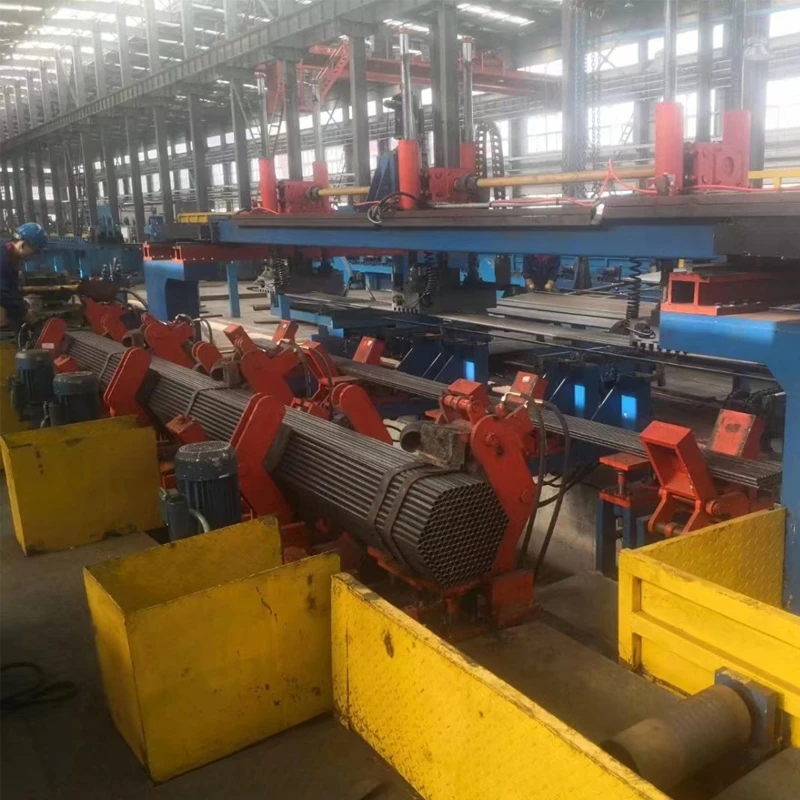
Roll forming is a continuous bending operation, during which a long strip of sheet metal is passed through sets of rolls for desired cross-sectional configurations. The rollers, designed meticulously for specific duties, are responsible for the accuracy and consistency of the final product. Understanding the dynamics at play in roll forming can elevate a manufacturer’s output quality and operational efficiency.
Expertise in designing and employing roll forming rollers stems from a blend of engineering insights and hands-on experience. Rollers function under significant stress and require materials that can withstand prolonged wear and tear. Typically constructed from high-quality steel, they undergo rigorous hardening processes to enhance durability. Certain applications might demand rollers with specialized coatings or made from unique alloys to handle specific industrial requirements such as corrosion resistance or high temperature performance.
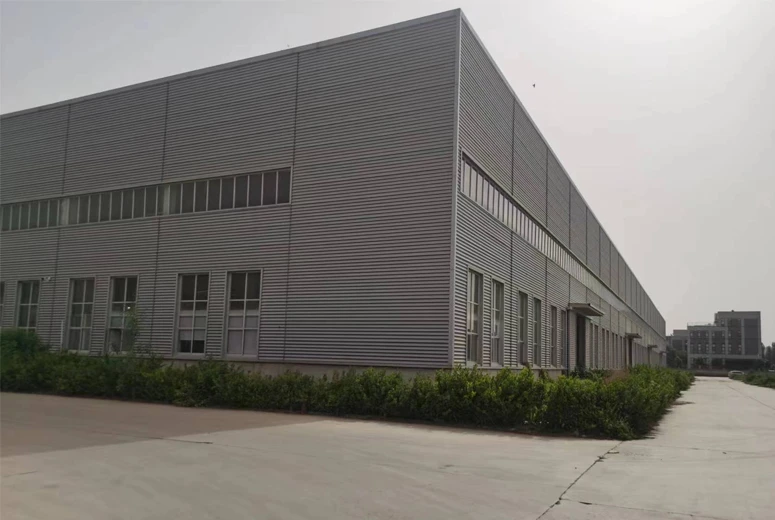
A key insight from industry veterans highlights how roller design directly affects the material handling process. The configuration of each roller set in a forming line must be optimized to ensure material flow without excess pressure or slippage which could lead to inaccuracies or deformities in the metal profile. The integration of precise calibrations and adjustments is vital, and continuous monitoring ensures alignment and pressure distribution remain within specified tolerances, thus guaranteeing product integrity.
From an operational perspective, the seamless cooperation between roll forming rollers and the machinery forms the backbone of product customization and production speed. In sectors ranging from automotive to construction, the demand for highly complex and customized profiles is ever-increasing.
Modern roll forming technology has evolved, offering programmable mechanisms able to adjust roll settings in real-time. This capability reduces downtime and the need for manual interventions, proving beneficial in industries pushing towards full automation.
roll forming rollers
To maintain confidence and trustworthiness in roll forming processes, rolling equipment must be routinely serviced and maintained. Industry recommendations emphasize the importance of regular inspections to assess roller condition, identify wear, and apply necessary restorative procedures. Documentation of maintenance practices not only upholds quality standards but also extends the longevity of the machinery, safeguarding investments and ensuring uninterrupted production timelines.
Authority in roll forming roller production lies with those manufacturers who are proactive in innovation and hold certifications attesting to their quality and reliability. Adopting cutting-edge technologies such as computer-aided design (CAD) and advanced testing facilities enable the production of rollers with unparalleled precision. Manufacturers that possess certification from recognized industry bodies further bolster client trust, showcasing adherence to stringent quality norms and industry best practices.
Trust in the roll forming environment translates to confidence in delivering parts that meet or exceed customer expectations consistently. Professionals within this domain continue to emphasize the importance of transparency and collaboration throughout the production cycle. By fostering close partnerships between product developers and clients, manufacturers can tailor solutions that best fit unique production challenges and specifications.
Ultimately, roll forming rollers are central to the efficiency and precision of metal forming operations. Supporting sophisticated and highly customized industrial needs, they remain a pivotal asset in the production chain, invariably influencing product quality and operational success. Expertise and trust in the components and processes ensure manufacturers can deliver superior results while embracing new technological advances and meeting market demands.