Cold pilger mills play a crucial role in the seamless tube manufacturing industry. With increasing demand for high-quality tubes, manufacturers are constantly seeking efficient solutions to optimize their production processes. A cold pilger mill stands out due to its unique capability to produce tubes with exceptional precision and outstanding surface finish.
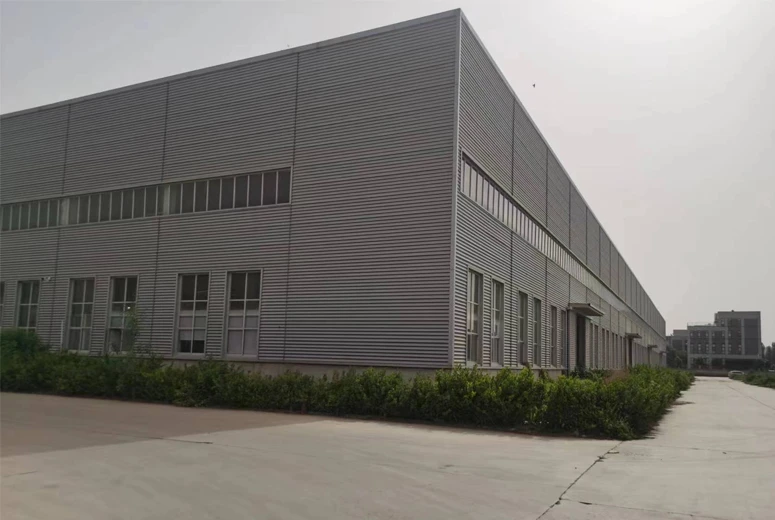
The cold pilger process involves using a specialized rolling mill that cold works the metal to obtain desired dimensions and properties. Unlike other tube forming methods, cold pilgering ensures minimal material wastage, making it an economical option for manufacturers. By incrementally shaping and reducing the diameter of the tube, this method achieves unparalleled accuracy and consistency in wall thickness, which is essential for industries like aerospace, oil and gas, and automotive, where precision is paramount.
One of the critical advantages of using a cold pilger mill is its ability to work with a wide range of metals, including stainless steel, titanium, and exotic alloys. This versatility is crucial for industries that require tubes with custom specifications and high-performance characteristics. The cold working process significantly improves the mechanical properties of the tubes, enhancing their durability and resistance to extreme conditions.
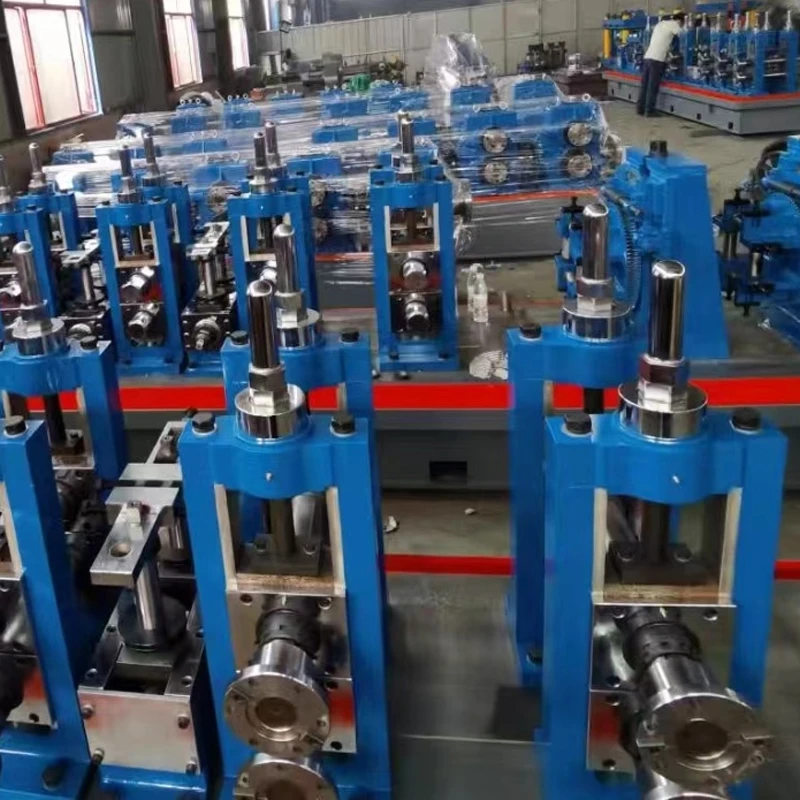
From a technical standpoint, operating a cold pilger mill requires expertise and meticulous attention to detail. Skilled operators ensure the mill settings are optimized for each specific material and tube size, taking into account factors such as feed rate, speed, and roll design. This expertise minimizes defects and enhances the quality of the final product.
cold pilger mill
Manufacturers who have integrated cold pilger mills into their production lines often report increased competitiveness in the marketplace. The advanced technology of these mills boosts productivity and reduces the cost per unit by streamlining the production process. Additionally, the consistency in product quality achieved with cold pilgering fortifies brand reliability and customer trust, as clients receive tubes that meet stringent industry standards.
To maintain the high performance of a cold pilger mill, regular maintenance and calibration are essential. Routine checks ensure the equipment functions at optimal efficiency and helps prevent costly downtimes. Investing in training for personnel to operate and maintain the machinery not only extends its lifespan but also leverages its full potential, contributing to overall operational success.
Finally, the adoption of cold pilger mills aligns with the growing emphasis on sustainability in manufacturing. The method’s efficiency in material usage and ability to produce longer-lasting products contribute to eco-friendly production processes. By reducing waste and energy consumption, manufacturers not only achieve cost savings but also support global efforts towards sustainability.
For companies aiming to elevate their production capabilities and meet the rigorous demands of modern industries, cold pilger mills represent a formidable technological advance. Their integration into the manufacturing process not only ensures superior quality and precision but also enhances operational efficiency, making them an invaluable asset in the competitive landscape of tube production.