Navigating the landscape of sheet metal roll forming technology can be an enriching journey for any industry expert. Roll forming is a continuous bending operation in which a long strip of metal, often coiled steel, is passed through sets of rolls, or stands, which progressively shape the metal into the desired cross-section. For those seeking cutting-edge solutions in metal fabrication, understanding the experience-driven and expert-backed innovations in sheet metal roll forming is essential.
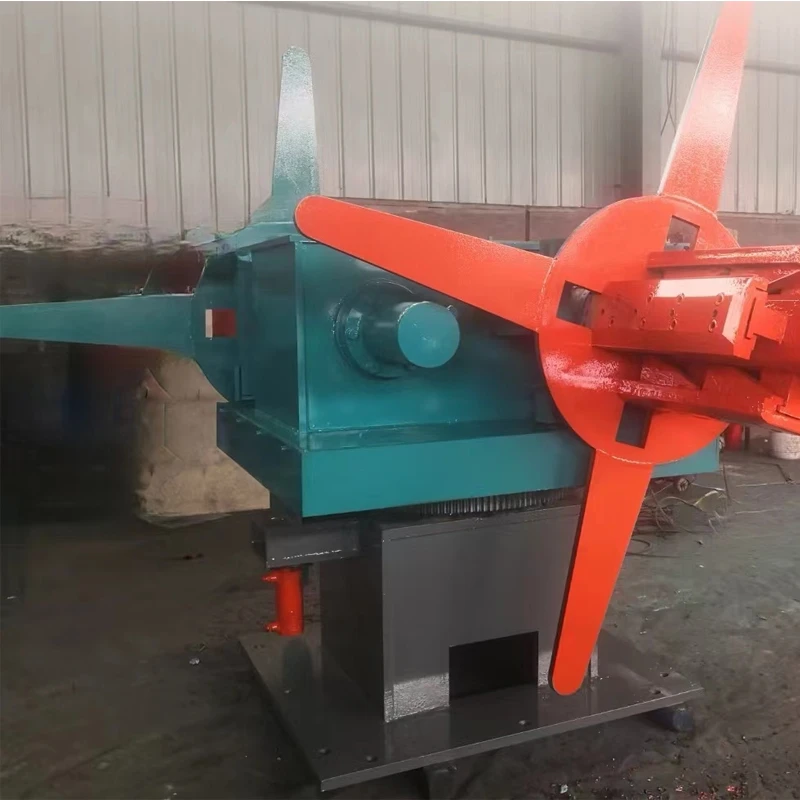
A profound experience in metal roll forming begins with recognizing the unique advantages this process offers over other metal shaping techniques. Unlike traditional stamping methods, roll forming reduces waste, optimizes material usage, and increases output efficiency. Experts in the field appreciate how the continuous nature of roll forming supports long production runs, crucial for meeting the demanding needs of automotive, construction, and appliance industries. Furthermore, the precision in achieving complex profiles makes it an invaluable technique for producing high-strength components with excellent finish quality.
Expertise in roll forming is characterized by an intimate knowledge of the process nuances, such as material properties, roll design, and machine control technologies. Materials used in roll forming, including aluminum, galvanized steel, stainless steel, and copper, each require different handling and machine settings. A true expert knows to tailor the machine settings to accommodate the material’s properties, ensuring durability and performance of the finished product. Moreover, designing the rolls with precision engineering is critical. The complexity of these rolls, which must consider the spring-back effect and profile defects, calls for a deep understanding of mechanical design and material science.
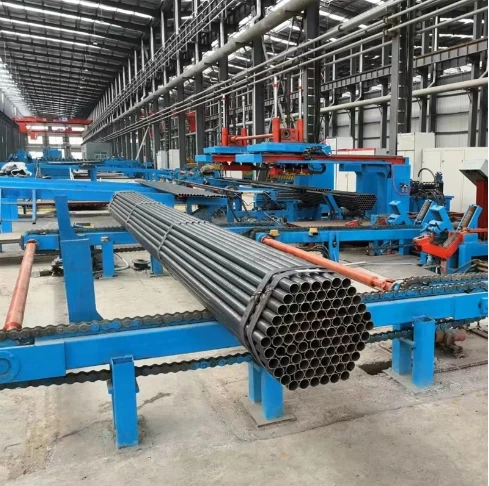
Authority in the sheet metal roll forming industry is earned by continuously pushing the boundaries of the technology. Innovators in this space are investing in computer-aided design (CAD) and computer-aided manufacturing (CAM) to create more precise modeling and simulations before the actual roll forming begins. This advancement minimizes trial and error on the production floor, reducing costs and enhancing speed to market. Additionally, integrating control systems that automate adjustments during the rolling process based on real-time data analytics exemplifies authority. These adjustments lead to consistent product quality and operational efficiency, hallmark traits of leaders in the field.
sheet metal roll former
Trustworthiness within the realm of roll forming not only originates from delivering durable and reliable products but also from fostering transparent relationships with clients. Companies with formidable reputations ensure their engineering teams collaborate closely with clients to understand specific requirements and customize solutions accordingly. Trust is also built through compliance with international standards and certifications, ensuring that all products meet stringent quality and safety benchmarks.
Product development in sheet metal roll forming is highly competitive, demanding continuous innovation and a keen understanding of market trends. A recent advancement includes the adoption of flexible roll forming technologies, which allow for variable profiles to be produced in a single run without changing rolls. This flexibility is particularly crucial in industries that require rapid design changes, providing a significant competitive edge.
The narrative around sheet metal roll forming is one of innovation, precision, and reliability—a narrative controlled by those with experience, expertise, authority, and trustworthiness. As industries evolve and demand higher levels of efficiency and precision, roll forming will undeniably continue to play a pivotal role, offering sustainable, cost-effective, and innovative solutions for metal component manufacturing. This convergence of tradition and technology solidifies the position of roll forming as an indispensable process within the modern manufacturing landscape.