Sheet roll forming stands out as an essential manufacturing process that has continually evolved to meet the demands of various industries. At its core, this technique involves the continuous bending of a long strip of sheet metal (typically coiled steel) into a predetermined cross-section. The subtlety and precision of this process have made it indispensable in the production of uniform parts, which are crucial for industries ranging from automotive to construction.
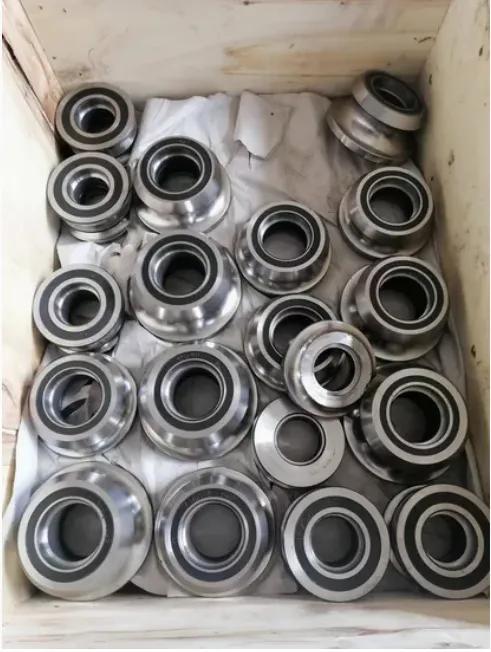
One of the most compelling aspects of sheet roll forming is its ability to produce consistent, high-quality results at an impressively fast rate. Manufacturers need not worry about the uniformity of their products when employing this technique, as it guarantees precise duplication from the first item to the millionth. This consistency significantly reduces the risk of product failure, enhancing both the safety and durability of the finished goods.
The expertise required in sheet roll forming is monumental. Unlike other manufacturing processes, it demands a deep understanding of metallurgical behaviors and mechanical principles.
This is where the expertise of a skilled roll former becomes apparent. A seasoned professional can adjust the rolling process parameters to accommodate different metal thicknesses and compositions, ensuring that the end product meets strict specifications for strength, flexibility, and appearance. For instance, producing components for the automotive industry with intricate profiles requires not only specialized machinery but also the know-how to prevent defects such as warping or surface imperfections.
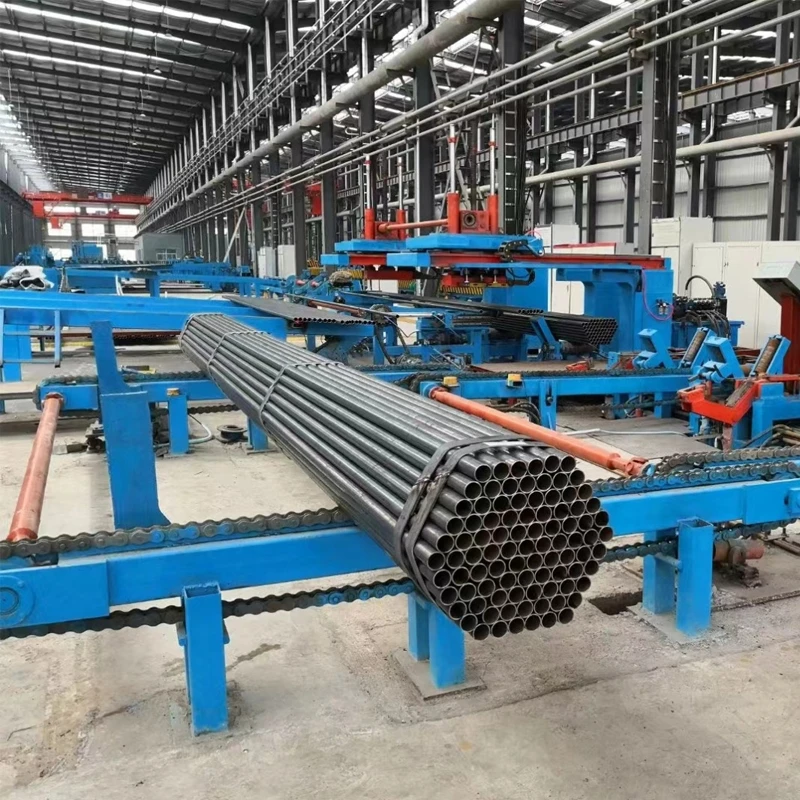
Authoritativeness in the field is bolstered by the advancements in technology that accompany sheet roll forming. Modern roll forming machines are equipped with cutting-edge technology, such as computer numerical control (CNC) systems, that allow for intricate designs and precise cuts. Manufacturers who invest in such technology are considered industry leaders, setting benchmarks for quality and efficiency. These technological advancements also permit on-the-fly adjustments during production, enhancing flexibility and reducing downtime.
sheet roll form
Beyond the technological prowess and expert skill involved, trustworthiness in sheet roll forming is achieved through rigorous quality assurance processes. Manufacturers employ a series of tests and inspections at various stages of the roll forming process to ensure that each component not only meets but often exceeds industry standards. This meticulous attention to detail is what gives clients the confidence that they are receiving products that are as reliable as they are innovative.
Real-world experiences further illustrate the benefits of sheet roll forming. Consider a case where a construction company required a large quantity of roofing sheets with an exacting profile to fit a new architectural design. By collaborating with a roll forming manufacturer, they received custom-designed sheets that seamlessly integrated into the building structure. The precision and speed of delivery were vital to keeping the project on schedule and within budget, highlighting the process's adaptability and reliability.
These experiences, combined with the specialized expertise in the domain, establish sheet roll forming as not only a manufacturing process but as a cornerstone of modern industrial capability. Its ability to disrupt traditional manufacturing limitations by offering fast, accurate, and versatile production solutions ensures its ongoing relevance in a rapidly evolving market landscape.
In conclusion, sheet roll forming is a shining example of how expert knowledge, technological advancement, and rigorous quality control come together to forge a trustworthy and authoritative manufacturing solution. It serves as a testament to the innovative spirit that drives industries forward, ensuring that they are equipped to meet both current and future demands.