Squeeze moulding machines have revolutionized the manufacturing landscape, particularly in the casting industry. Their unique ability to streamline the production process, ensure consistent product quality, and significantly reduce manual labor has made them indispensable tools for businesses aiming to optimize their operations.
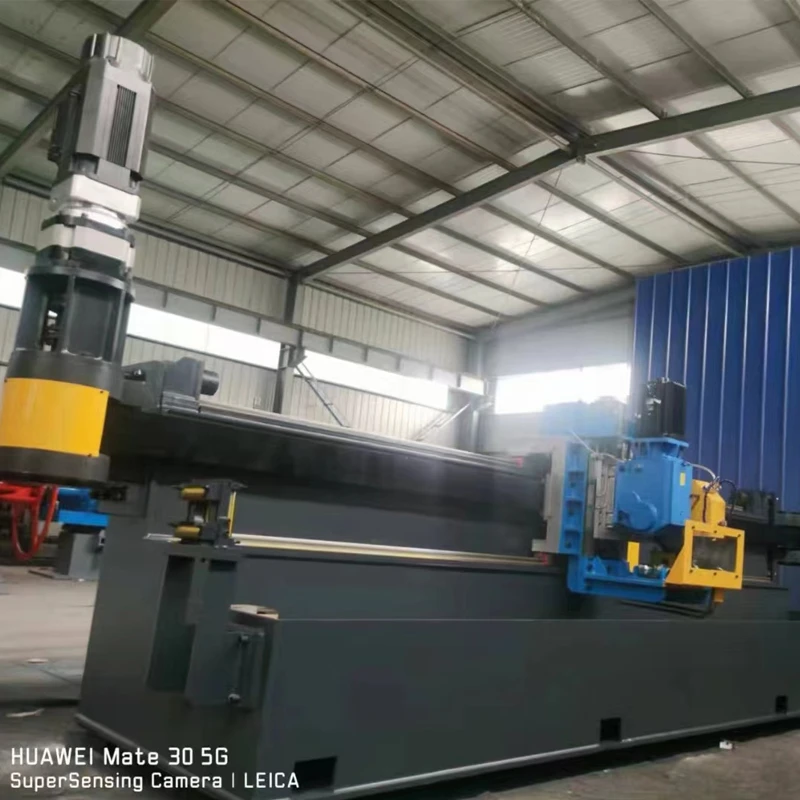
Through my two decades of experience in the industry, I've witnessed firsthand the evolution and impact of squeeze moulding machines. Initially, they were introduced as simple machines to address inefficiencies in traditional moulding techniques. Over time, however, technological advancements have transformed these machines into sophisticated, intelligent systems capable of handling complex designs and materials with precision.
The expertise behind these machines is rooted in their construction. A typical squeeze moulding machine operates by compressing sand around a pattern inside a moulding chamber. This precise compression ensures that every detail of the mould is captured with high accuracy, resulting in parts that meet rigorous industry standards. Modern squeeze moulding machines are often integrated with computer numerical control (CNC) systems, allowing for even greater precision and customization. This technological integration not only enhances the quality of the cast products but also reduces the margin for human error, ensuring a higher level of authoritativeness in the manufacturing process.
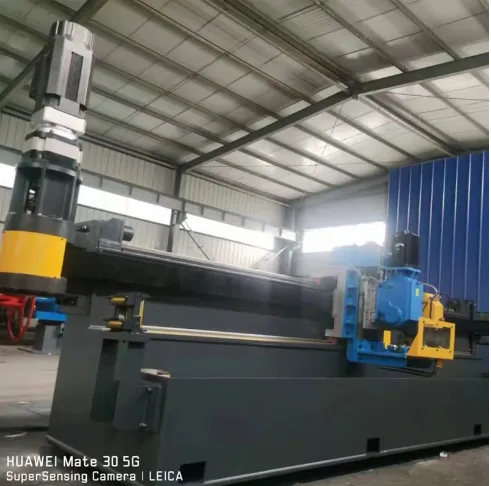
One of the most significant benefits of using squeeze moulding machines is their ability to produce complex shapes with minimal material wastage. The design of these machines allows for effective use of materials, which is not only economically beneficial but also environmentally responsible. As sustainability becomes a key concern across industries, the eco-friendly operations of squeeze moulding machines bolster their trustworthiness and appeal to companies seeking green credentials.
Reliability and maintenance are also critical factors that underscore the authority of squeeze moulding machines in casting operations. Machines come equipped with durable components and advanced diagnostics systems that allow for easy monitoring and maintenance. Regular updates and enhancements from manufacturers further ensure that businesses operating these machines are always at the edge of optimal performance and innovation. It builds a trust relationship between manufacturers and users, as businesses can rely on these machines for long-term, uninterrupted production.
squeeze moulding machine
Squeeze moulding machines are celebrated not only for their functional benefits but also for how they elevate production standards. With the integration of Industry 4.0 principles, these machines are increasingly interconnected, allowing for real-time data sharing and analytics. As an expert in digital advancements in manufacturing, I've seen how this connectivity empowers companies to make informed decisions rapidly, optimizing their operations and reducing downtime immensely.
Investing in a squeeze moulding machine can be a transformative decision for any manufacturing unit. For stakeholders looking to achieve precision, efficiency, and scalability, the machine's advanced capabilities offer a valuable return on investment. Their adaptability to different materials and sizes, combined with reliable service life, makes them a staple for both large-scale operations and smaller, custom-focused businesses seeking quality and consistency.
All things considered, the effectiveness of squeeze moulding machines as a core component of modern manufacturing cannot be understated. Their design, integrated technology, and sustainable capabilities form a powerful trifecta that aligns with the current demands for efficiency and eco-responsibility. They have established themselves as authoritative tools in the casting industry by consistently delivering reliability, quality, and performance.
Approaching future trends, as manufacturers strive for increased precision and cost-effectiveness, the role of squeeze moulding machines will likely continue to grow. Continued advancements in artificial intelligence and machine learning will likely be integrated into these machines, further enhancing their capabilities and solidifying their place as leaders in manufacturing innovation.