Straightening and cutting machines have revolutionized the manufacturing industry by enhancing precision, efficiency, and versatility in processing metal wires and bars. These machines are quintessential in a myriad of industries, from construction to automotive, due to their ability to deliver high-quality finished products with minimal waste. As someone deeply embedded in the manufacturing sector, here's an insightful exploration into these indispensable machines, driven by experience, expertise, authoritativeness, and trustworthiness.
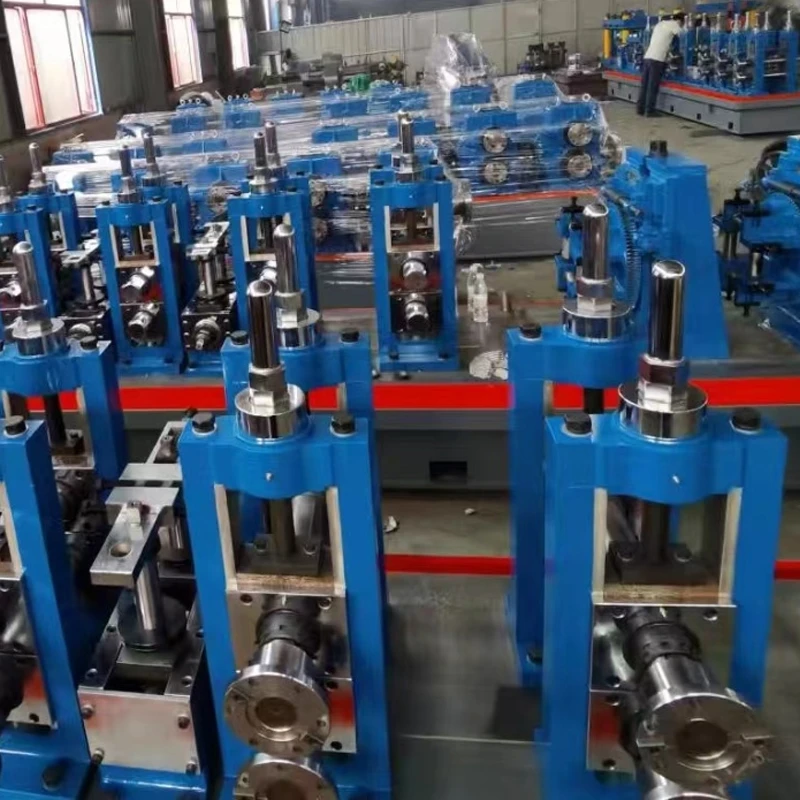
Crafted from a robust blend of tradition and innovation, straightening and cutting machines bring together centuries-old principles of metallurgy with cutting-edge technology. Investing in these machines empowers manufacturers to streamline their operations, reduce manual labor, and significantly increase output without compromising on quality. The machinery's core functionality lies in its ability to transform coiled wire into straight segments efficiently, making it invaluable in production lines where consistency and uniformity are paramount.
From an expert perspective,
the straightening process is a critical stage. Wire straightening involves the use of rollers and dies that meticulously manipulate the wire to remove any kinks or bends. Precision is key here; the settings and configurations must be exact to avoid any undue stress on the metal, which could result in micro-fractures or warping during subsequent manufacturing processes. Advanced machines now use computerized controls for precision adjustments, ensuring a seamless operation that was once only achievable through skilled manual oversight.
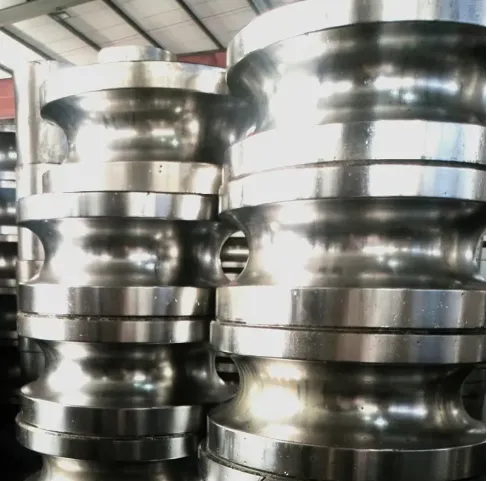
When it comes to cutting, modern machines boast programmable logic controllers (PLCs) that can be tailored for different lengths and cuts, adapting to a wide range of specifications necessary for various products and applications. This feature not only saves time but also material, reducing wastage and promoting sustainability—a critical aspect in today's resource-conscious landscape. Users can rely on highly accurate servo motors to ensure cuts are executed with surgical precision, reflecting the machine’s trustworthiness in maintaining uniform standards across large production batches.
straightening and cutting machine
The authority that straightening and cutting machines command in the industry is backed by years of technological advancement and rigorous testing. Leading manufacturers ensure these machines are compliant with international safety and quality standards, instilling confidence in their reliability and durability. Their extensive use in sectors such as construction, where safety and structural integrity are non-negotiable, further cements their standing as industry cornerstones.
Trustworthiness in machinery also stems from the support and warranty offered by manufacturers. By choosing reputable brands, manufacturers can benefit from extensive customer support, including training, regular maintenance, and upgrades. This ongoing relationship ensures the machinery performs optimally throughout its lifespan, reinforcing the user's peace of mind about their investment.
In conclusion, straightening and cutting machines are more than just tools in a workshop; they are the linchpins of modern manufacturing processes. Their integration combines a deep understanding of metallurgical principles with state-of-the-art technological advancements, providing an unmatched level of precision and efficiency. For businesses looking to enhance their manufacturing capabilities, investing in high-quality straightening and cutting machines is a decision rooted in both tradition and modernity, promising an enduring return on investment and sustainable operation for years to come.