The straightening press is a crucial piece of equipment in industries where precision and accuracy are non-negotiable. From automotive to aerospace applications, these presses play a vital role in ensuring that metal components meet strict dimensional standards. This article delves into the importance of straightening presses, drawing on expert knowledge to highlight their advantages and authority in manufacturing processes.
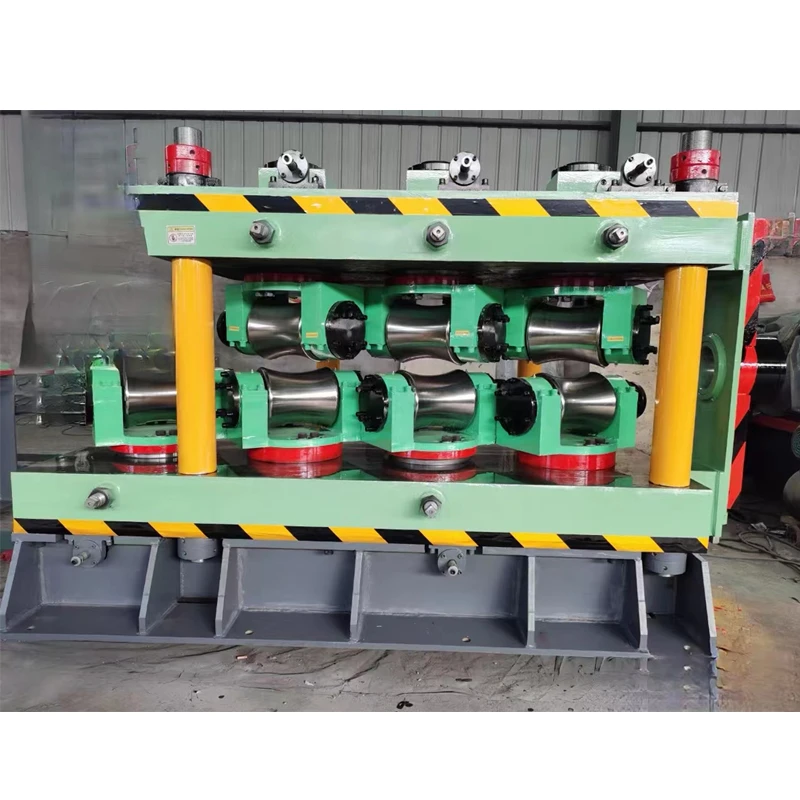
Straightening presses are primarily used to correct deformations in metal components. During the manufacturing process, metal parts can become slightly distorted due to stresses induced during machining, cutting, or welding. A straightening press applies a controlled amount of pressure to these parts, bringing them back to their precise, intended shapes. This ability to rectify imperfections boosts the reliability and performance of the final product, especially in applications where even minimal deviations can lead to significant issues.
A significant advantage of straightening presses is their adaptability. They are versatile machines that come in various sizes and specifications to accommodate different shapes, materials, and levels of deformation correction. For example, in the rail industry, large straightening presses are employed to correct the alignment of rails, ensuring the safety and smoothness of train operations. Meanwhile, smaller presses are used in the manufacturing of precision tools and components for high-end electronics, where minute accuracy is paramount.
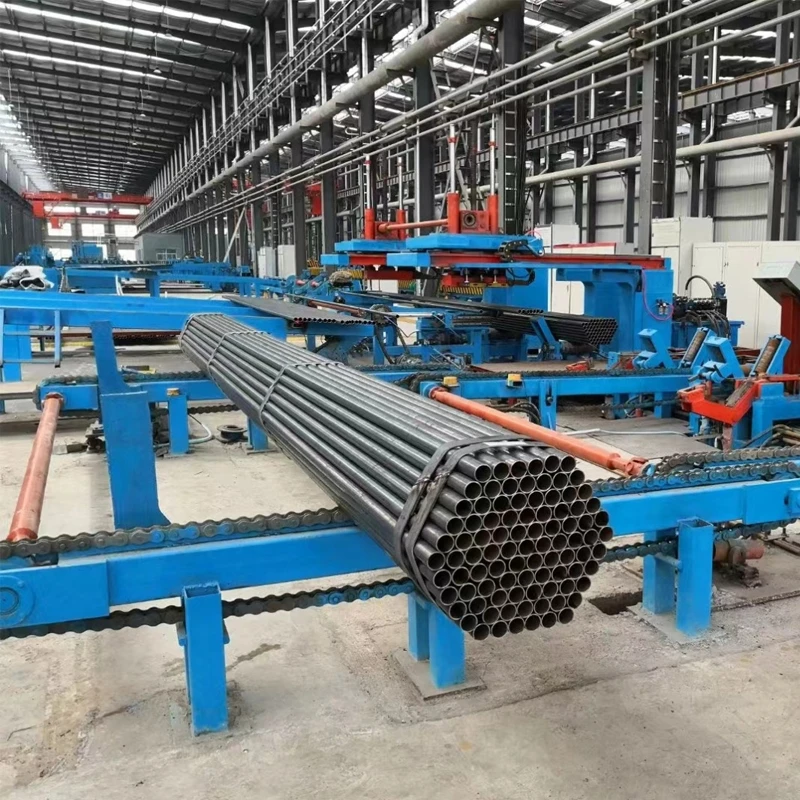
From an expertise standpoint, understanding the operation of a straightening press requires in-depth knowledge of materials science and mechanical engineering. Professionals working with these presses must be able to assess the nature of deformations and determine the appropriate level of pressure and technique to apply. This delicate balancing act is critical, as improper use could either fail to correct the defect or worse, exacerbate the distortion or even damage the part.
straightening press
The authority of manufacturers and suppliers of straightening presses stems from their continuous innovation and adherence to industry standards. Established companies are often at the forefront of technological advancements, integrating digital controls, and automation features that increase precision and efficiency. They frequently invest in R&D to improve machine capabilities, ensuring they meet the evolving demands of modern manufacturing techniques.
In demonstrating trustworthiness, reputable suppliers provide comprehensive training and support to their clients, ensuring that their machines are operated correctly and safely. They also offer full maintenance and service packages, which are critical for maintaining the longevity and performance of these high-precision machines. Additionally, the use of high-quality materials in the construction of straightening presses further enhances their durability and reliability, making them a worthwhile investment for industries that cannot afford downtime or production errors.
As global manufacturing standards tighten and the push for higher quality products intensifies, the importance of reliable straightening processes becomes even more pronounced. By investing in a high-quality straightening press, manufacturers can significantly reduce material waste, enhance product quality, and ultimately, increase customer satisfaction.
In conclusion, the straightening press is more than just a piece of industrial equipment; it is an embodiment of precision engineering. With its ability to deliver unparalleled accuracy and efficiency, it stands as a testament to the advancements in modern manufacturing technologies. Companies that prioritize quality and accuracy in their production processes will find straightening presses to be indispensable assets, ensuring their products not only meet but exceed industry expectations.