The tandem rolling mill process is a sophisticated and intricate procedure integral to modern metalworking, particularly in producing sheets, wires, and other products requiring uniform thickness and superior surface quality. This process's efficacy stems from its unique ability to continuously roll metal through a series of linearly arranged rolls, enhancing both efficiency and precision.
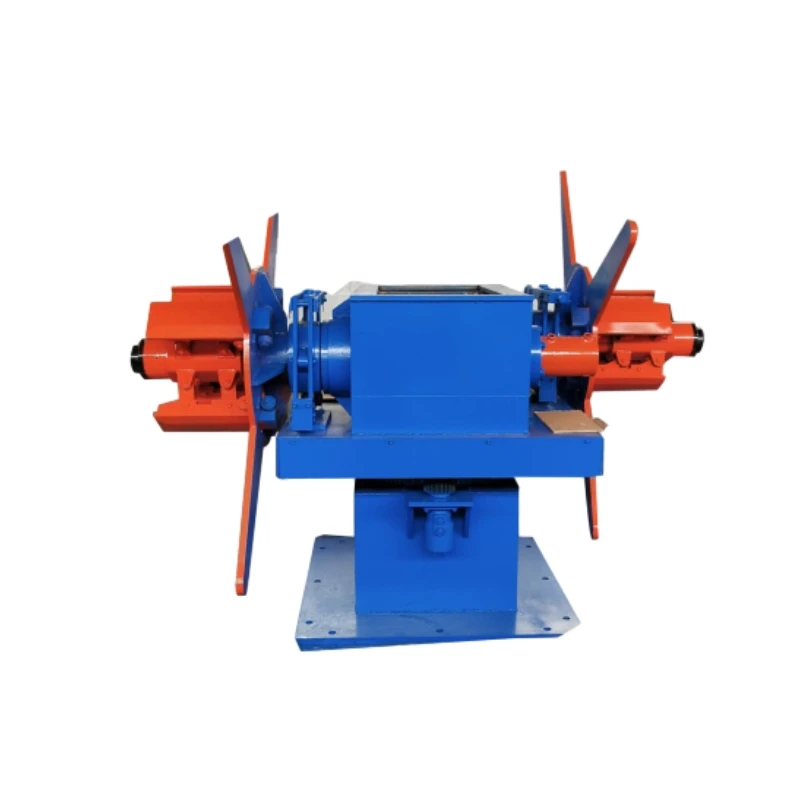
At the heart of the tandem rolling mill process is its capacity to transform raw metal into a final product that meets precise specifications. This transformation is achieved through a series of synchronized mills, often encompassing four to six or more pairs of work rolls. Each rolling stage reduces thickness while elongating the material, maintaining a consistent tension across the entire line. The key advantage here is the continuous nature of the process, allowing high productivity rates and uniformity in the final output.
Experience in operating tandem rolling mills reveals how essential maintaining perfect synchronization across all rolling stages is. Any misalignment can lead to significant quality defects in the rolled products, such as thickness variation or surface irregularities. Operators must possess acute attention to minute details, regularly adjusting roll gaps and speeds to ensure optimal results. This careful calibration ensures that the tremendous pressures exerted on the metal distribute evenly without introducing unwanted deformations.
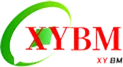
Specialists engaged in the tandem rolling mill process emphasize the necessity of in-depth knowledge on material properties. Different metals and alloys respond uniquely to the rolling process; understanding these nuances is critical for adjusting the process parameters—such as roll pressure, temperature, and speed—to achieve the desired mechanical properties and surface finish. Advanced software tools now aid operators in simulating different rolling scenarios, predicting the outcomes, and reducing costly trial-and-error experiments.
tandem rolling mill process
Authoritative knowledge in metallurgy combines with expertise in mechanical engineering to address the common challenges faced during tandem rolling. The interaction between the rolls and the metal surface can lead to issues such as wear and tear of the rolls themselves. To combat this, engineers have designed rolls with durable coatings or incorporated hardening techniques to extend their lifespan, thereby ensuring continuous operation with minimal disruptions. Furthermore, cooling systems are integrated within the rolling mills to dissipate the considerable heat generated during the process, protecting both the equipment and the quality of the product.
Trust plays a crucial role in the tandem rolling mill process, particularly between manufacturers and clients. Meeting the stringent standards required by industries such as automotive, aerospace, and construction demands not only technical precision but also transparency in process execution. Accurate, real-time monitoring systems have become an industry standard, ensuring that every roll, every batch, conforms to a set quality benchmark.
Additionally, sustainability has emerged as a critical focus in optimizing the tandem rolling mill process. The industry is making significant strides in reducing energy consumption and minimizing waste. By implementing advanced control technologies, including IoT and AI-driven analytics, manufacturers can optimize energy use, thus reducing their carbon footprint and operational costs in the long run. Recycling initiatives further align the tandem rolling mill process with global environmental goals, particularly in industries that re-process scrap metal into new high-quality products.
In essence, the tandem rolling mill process stands as a testament to the integration of engineering prowess with practical, hands-on expertise. Its development reflects not only the industrial demand for high-efficiency production techniques but also the continuous push towards innovation, sustainability, and reliability in metal manufacturing. As technology advances, the process continues to evolve, promising even greater precision, productivity, and environmental stewardship. Harmonic concert between human expertise and technological advancements will likely play a crucial role in shaping the future of metalworking through tandem rolling mill processes.