In the sprawling landscape of manufacturing, where precision and efficiency hold the key to success, the tube mill machine process stands as a testament to these principles. As an integral component in the production of pipes and tubes, its significance can't be overstated. From the vantage point of a seasoned expert in the field, let's delve into the intricacies of the tube mill machine process, offering invaluable insights that bolster both understanding and application.
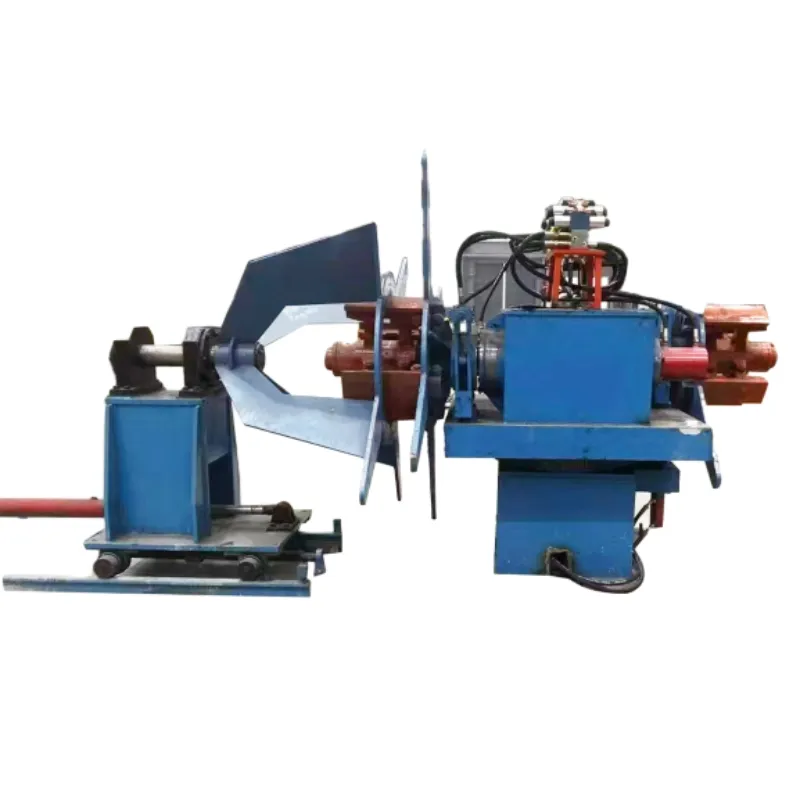
The tube mill machine process involves a series of meticulously coordinated steps, each contributing to the transformation of raw metal strips into seamless, robust tubes. Initially, the journey begins with uncoiling, where large metal strips are unwound and fed into the system. The expertise lies in ensuring the strips maintain their integrity, which is crucial for the final product's quality. This stage demands precise tension control and alignment, factors that experienced operators continuously monitor.
Moving forward, the strips undergo a forming stage, a critical point where the metal is gradually shaped into tubular form. This stage showcases the machinery's prowess as it balances force and finesse, guiding the metal without compromising its properties. Here, the operator's expertise ensures that the forming rolls and pressure settings align perfectly with the type of metal in use, a testament to the critical knowledge possessed by veterans in the industry.
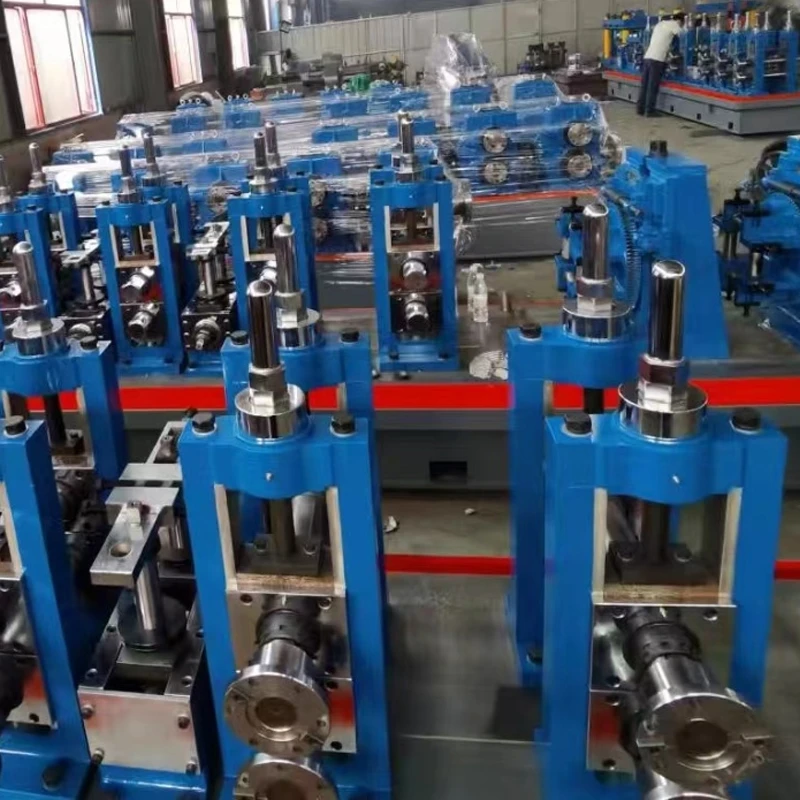
Welding,
the next phase, is where the process displays both art and science. The tube's edges are welded together using high-frequency electrical currents, culminating in a continuous seam. Mastery in this stage lies in maintaining the correct heat levels and speed, a balancing act critical to preventing defects or weaknesses in the seam. This phase underscores the authoritative knowledge required to operate modern tube mill machines, where even minute deviations can lead to significant inefficiencies.
tube mill machine process
Following welding, the tube undergoes cooling and sizing, steps designed to solidify its structure and refine its dimensions. Expert operators understand the subtleties of these phases, such as the importance of maintaining a consistent cooling rate to avoid structural imbalances. Sizing rolls are adjusted with precision to ensure the tube meets exact specifications, highlighting the trustworthiness required when ensuring the product meets stringent quality standards.
Lastly, cutting and packaging finalize the process, where the endless tube is sectioned into commercially viable lengths. The process demands accuracy and efficiency, attributes honed over years of experience. Trust is placed in operators to maintain the machinery's calibration, thereby ensuring each cut is pristine, further enhancing the product's reliability.
In essence, the tube mill machine process is not merely a sequence of mechanical steps; it’s a symphony conducted by skilled professionals whose expertise turns raw materials into vital components of industrial society. It's a domain where experience breeds insight, proficiency cultivates authority, and meticulous care nurtures trust. As industries evolve, the tube mill process remains a critical linchpin, bridging the gap between raw potential and functional reality, underscoring its timeless relevance in the world's industrial tapestry.