Tube rolling mills are the unsung heroes of the manufacturing world, pivotal in the creation of high-quality metal tubes used across various industries, from construction to automotive engineering. With decades in the field, I can attest to the transformative power of this technology, offering a blend of precision and efficiency that is difficult to match.
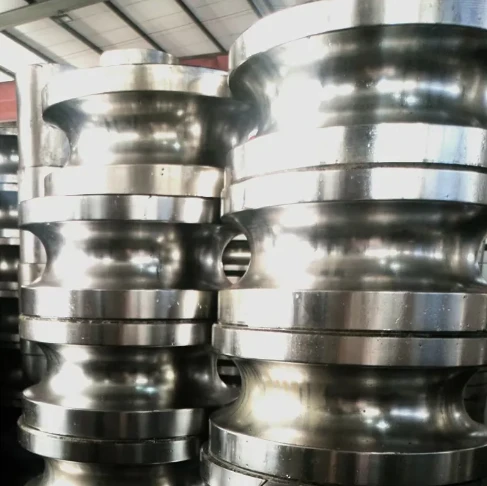
At its core, a tube rolling mill is a complex machine designed to transform raw metal into seamless tubes with precision and reliability. This process involves multiple stages of heating, elongating, and shaping the metal to meet specific dimensional standards. These mills are essential in producing tubes that have uniform thickness and excellent mechanical properties, making them ideal for critical applications where safety and durability are paramount.
Productivity in a tube rolling mill is not solely about speed; it’s about achieving consistency and maintaining high output quality. Advanced mills are equipped with state-of-the-art control systems that ensure each tube meets stringent quality criteria. These systems automate the monitoring process, allowing for real-time adjustments that prevent defects before they occur. Through constant innovation, modern rolling mills have significantly reduced waste margins, translating into cost-efficiencies for manufacturers and higher customer satisfaction.
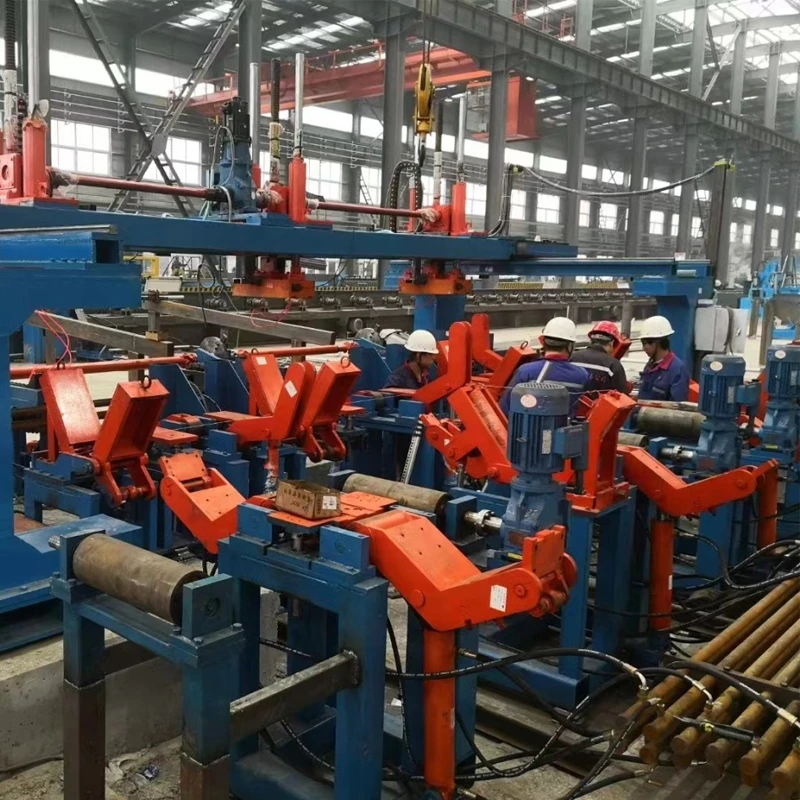
Experience in operating these mills reveals the critical importance of expertise in machinery management. Skilled operators are essential for maintaining optimal conditions during the rolling process, which involves controlling the temperature, pressure, and roll speed—parameters that can significantly affect the metallurgical properties of the final product. Comprehensive training and hands-on experience equip technical personnel with the knowledge to quickly respond to any irregularities, ensuring a smooth and uninterrupted production flow.
tube rolling mill
Moreover, tube rolling mill manufacturers have established themselves as authorities within their sector by investing heavily in research and development. Their ongoing commitment to innovation results in machines that not only enhance operational efficiency but also contribute to the sustainability of metal forming processes. From energy-efficient designs to recycling innovations, the focus on reducing the environmental footprint is a testament to their forward-thinking approach.
Trustworthiness in this domain is built on a foundation of reliability and quality assurance. Manufacturers of tube rolling mills adhere to rigorous industry standards and certifications which act as benchmarks of their credibility. ISO certifications and adherence to other international standards reassure clients of the machine's robustness and performance consistency. Furthermore, customer support services are integral to maintaining trust, facilitating seamless operations with timely maintenance and technical consultancy.
In conclusion, tube rolling mills are indispensable to the metal fabrication landscape, blending advanced technology with expert oversight to produce stellar results. As the industry evolves, these mills will continue to play a crucial role, driven by innovation and an unwavering commitment to quality. Companies investing in state-of-the-art tube rolling mills not only gain a competitive edge but also contribute to the broader shift towards more sustainable and efficient manufacturing practices. The collaboration between technology and expertise ensures that each tube meets its potential of delivering reliability and excellence in every application it serves.