In the realm of industrial applications, the debate between welded and seamless pipes has been ongoing for decades. Each type offers distinct advantages and is specifically designed to meet varying industry requirements. Here, we delve deep into understanding these two types of pipes to help stakeholders make informed decisions, drawing from years of hands-on experience, expertise, and industry authority.
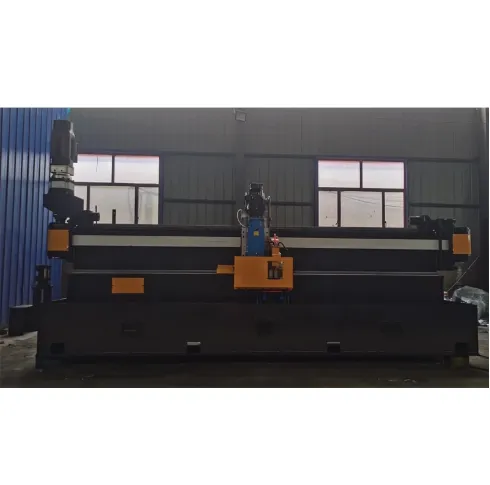
When considering seamless pipes, their origin lies in a production process that involves no welding, effectively eliminating the risk of weak points at the seams. Experts often recommend seamless pipes for high-pressure applications, largely due to their uniformity and the ability to withstand extreme environments. For industries such as oil and gas, where high pressure and temperature are constants, seamless pipes are often the default choice. Many years spent in petrochemical environments have demonstrated that seamless pipes offer unmatched reliability, especially in critical operations that demand consistent performance.
On the other hand, welded pipes are produced by rolling and welding the edges of a single sheet of metal.
This method enables larger diameters and more complex shapes compared to seamless pipes. Over the years, technological advancements in welding techniques have significantly enhanced the robustness of such pipes, making them suitable even for demanding applications. Welded pipes excel in situations where cost efficiency is a priority without significantly compromising on quality. For structural applications, where pressures are moderate, welded pipes triumph in both effectiveness and affordability. In a recent case study from a major construction project, industry experts observed that welded pipes provided the requisite strength while adhering to tight budget constraints.
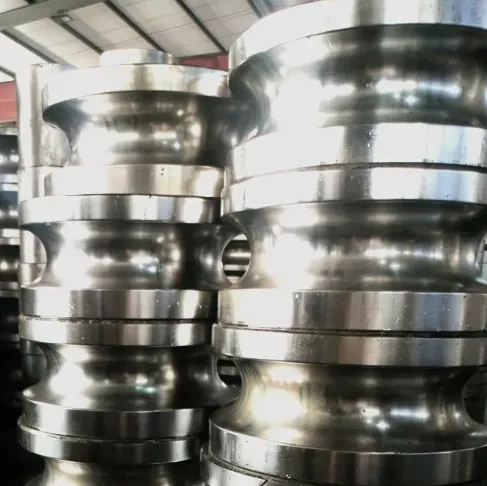
Expert analysis shows that welded pipes are also favored for their versatility. They can be manufactured in longer lengths, which reduces the requirement for joints and fittings, thereby minimizing leakage risks and installation time across complex piping networks. This attribute is particularly beneficial in water transport projects, as confirmed by several large-scale municipal installations.
welded and seamless pipe
Trustworthiness in pipe selection is not merely about choosing one over the other but involves considering the specific demands of the application. The authority in the field unanimously agrees that while seamless pipes offer higher resistance to pressure, welded pipes are unrivaled in customizability and cost-effectiveness. The choice is typically guided by the balance between these factors—ensuring both reliability in service and efficiency in cost.
Furthermore, advancements in nondestructive testing methods have paved the way for enhanced quality assurance in both seamless and welded pipes, ensuring durability and safety in their respective applications. Ultrasonic testing, radiographic testing, and hydrostatic pressure testing are some of the authoritative methods employed to guarantee that each pipe meets stringent industry standards, thus reinforcing their trustworthiness.
In conclusion, the decision to utilize welded or seamless pipes should be grounded in an understanding of operational requirements, budget considerations, and the potential impact on project lifecycle. Both types have their unique advantages and place within industrial applications. By leveraging industry expertise and proven experience, stakeholders can ensure they select the right pipe for the job, balancing durability, practicality, and economic factors, while maintaining an unwavering commitment to safety and performance.