Welded pipe production lines are essential in a variety of industries, from construction and transportation to oil and gas. The primary aim is to produce pipes that meet specific industrial standards with efficiency and precision. As the demand for welded pipes increases, understanding the intricate details of production lines becomes critical for manufacturers striving to maintain a competitive edge.
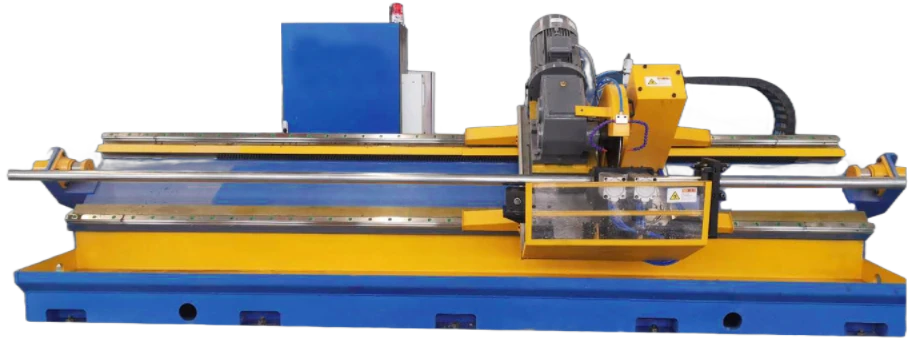
The first component of any successful welded pipe production line is the uncoiling section, which begins the transformation of raw material into a finished product. Raw metal strips—often sourced from reputable suppliers for quality assurance—are loaded onto a decoiler. This step is crucial as it ensures a continuous flow of material into the line without interruptions, thus optimizing productivity.
Next in the process is the leveling and trimming stage, where precision machines flatten and cut the edges of the strip, preparing it for welding. Modern production lines incorporate advanced leveling technology, reducing surface stresses and enhancing the structural integrity of the pipe. During this phase, trimming equipment uses high-precision blades to ensure the edges are perfectly aligned, a critical factor that influences the quality of the final weld.
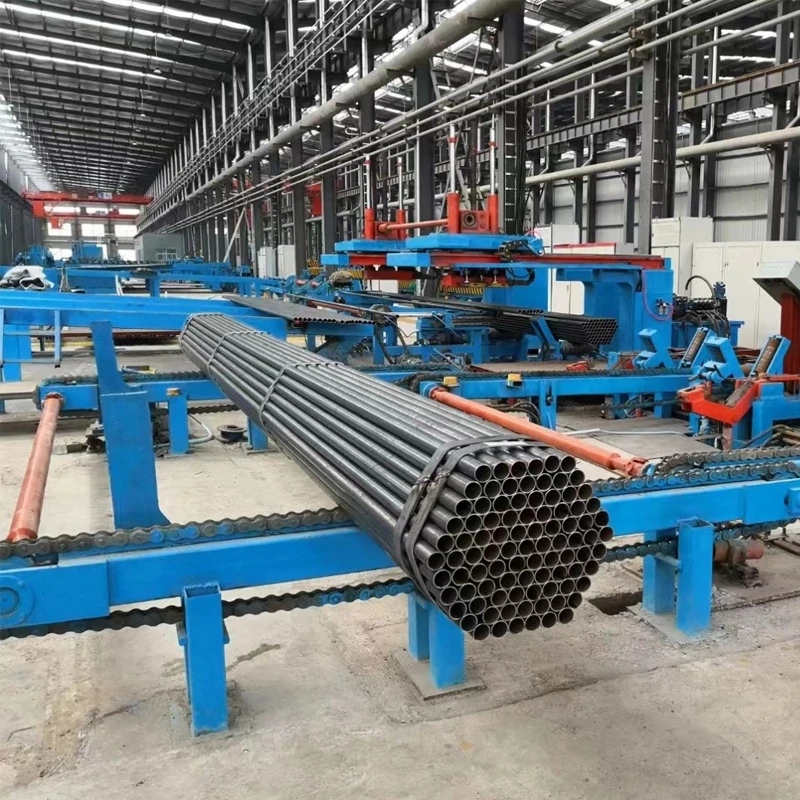
The heart of the welded pipe production line is the forming section, where the flat strip transforms into a tubular shape. This transition involves a series of carefully calibrated forming rollers, known as cages, which gradually bend the metal strip into a circular form. High precision in the design and operation of these rollers is crucial, as it directly affects the uniformity of the pipe width and the accuracy of its diameter.
Once the strip is successfully formed into a tube, the welding stage follows. Here, the seam of the pipe is welded using either High-Frequency Welding (HFW) or Electric Resistance Welding (ERW) technology. Both methods have their merits; however, HFW is often favored for its speed and the strength of the weld it produces. Thorough inspection systems are integrated into modern lines to detect any welding defects immediately, ensuring consistent product quality.
welded pipe production line
Post-welding,
the pipe undergoes sizing and straightening. Precision sizing rollers adjust the diameter of the pipe to exact specifications, while straightening machines guarantee the pipe's linearity. At this point, automated cut-off saws slice the pipe into predetermined lengths, readying them for further processing or immediate shipment.
Quality control is a continuous process on welded pipe production lines, not an afterthought. Advanced non-destructive testing methods, including ultrasonic and eddy current testing, scrutinize each meter of pipe for any defects in weld integrity or material consistency. These rigorous quality checks enhance the trustworthiness of the product, assuring customers of its reliability and safety.
Energy efficiency and sustainability have become indispensable aspects of modern welded pipe production lines. Innovations such as energy-efficient motors, heat recovery systems, and recyclable waste management systems not only reduce environmental impact but also cut operational costs, reflecting a commitment to sustainable manufacturing practices.
The expertise and authority of a welded pipe production line are demonstrated through its adaptability to produce various pipe specifications, meeting diverse industry standards. Standard Operating Procedures (SOPs) are meticulously documented and updated, ensuring a high level of operational knowledge among all personnel.
Ultimately, the credibility of a welded pipe production line is established through years of reliable performance and customer satisfaction. Manufacturers continuously invest in research and development to advance their production technologies, reinforce their reputation for excellence, and maintain industry leadership. By embracing advanced technology and sustainable practices, welded pipe production lines position themselves as indispensable assets in the industrial supply chain.