Aluminium cold rolling mills, integral to the production of high-quality aluminium products, are an impressive feat of modern engineering. These mills represent the pinnacle of precision manufacturing, ensuring both the durability and versatility of one of the world’s most important metals. As the demand for aluminium continues to climb due to its lightweight and anti-corrosive properties, the significance of advanced cold rolling technologies cannot be understated.
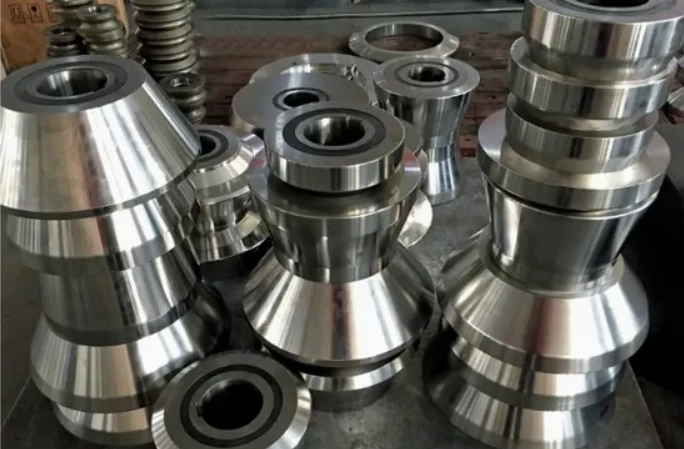
In the realm of aluminium production, cold rolling is pivotal as it enhances the metal's mechanical properties and surface quality. This process occurs at or near room temperature, unlike hot rolling that involves high temperatures. Cold rolling mills operate with immense accuracy, allowing for the consistent reproduction of thin and uniform aluminium sheets, which are fundamental in sectors ranging from automotive to aerospace and packaging.
Expert engineers design these mills with cutting-edge technology that optimizes material handling and energy use. This requires a comprehensive understanding of material science, as the properties of aluminium, including its formability and ductility, must be meticulously controlled throughout the rolling process. The expertise inherent in running these sophisticated machines is crucial. Operators must be adept in managing variables such as pressure, speed, and temperature, which directly influence the final product's quality.
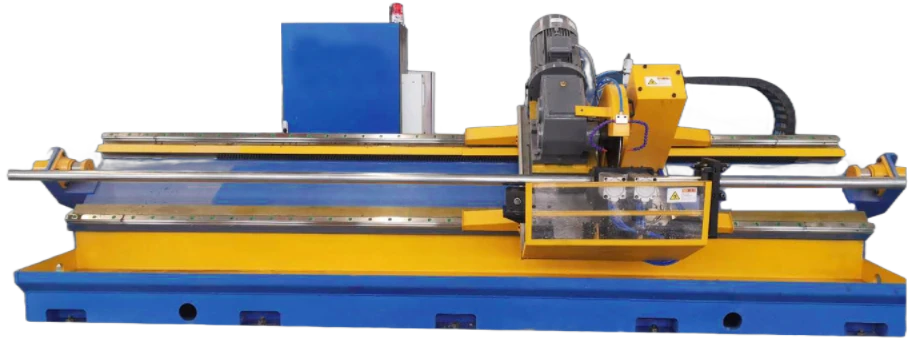
Furthermore, the machinery is equipped with advanced sensors and automation technologies, offering real-time feedback and adjustments. This aspect underscores the authoritativeness of manufacturers who invest in such innovative solutions, showcasing a commitment to precision and efficiency. Incorporating Artificial Intelligence (AI) in modern cold rolling mills is becoming increasingly common, thereby improving operational efficiency through predictive maintenance and energy management.
aluminium cold rolling mill
Trustworthiness in aluminium cold rolling is paramount for both producers and consumers. Companies that operate these mills must adhere to strict industry standards to ensure that the aluminium products meet global quality benchmarks. This involves regular audits, certifications, and compliance with environmental regulations, demonstrating a responsible approach to manufacturing processes. By employing sustainable practices and reducing energy consumption, these mills contribute to greener production methods, enhancing their reputability.
Product quality is another facet where trust is built. The surface finish and the mechanical properties of rolled aluminium are vital for downstream industries that depend on the material's reliability and performance. Whether for constructing automotive body panels or high-rise building facades, the consistency of high-quality rolled aluminium boosts consumer confidence.
Customization potential of cold rolling mills also adds to the industry’s expertise. Manufacturers offer tailored solutions to meet specific client needs, accommodating various alloy compositions and thickness requirements. This flexibility enables producers to serve a wider array of applications and innovate product lines, maintaining a competitive edge in the market.
In summary, aluminium cold rolling mills represent a confluence of engineering expertise, technological authority, and industry trust. These machines not only fulfill a critical role in the global aluminium supply chain but also exemplify how advanced manufacturing practices can drive industry standards. For companies seeking superior aluminium products, investing in or sourcing from reliable cold rolling operations is indispensable, promising quality assurance, efficiency, and sustainable production methods. As the drive for innovation and eco-conscious manufacturing intensifies, the role of cold rolling mills becomes even more central to the global industrial landscape.