Aluminum profile roll forming represents a sophisticated industrial technique that has revolutionized the production of lightweight, yet high-strength structural components. This method is particularly vital for industries such as automotive, aerospace, and construction, where both weight reduction and strength retention are critical. Through my extensive experience in the field, I have witnessed firsthand how embracing cutting-edge roll forming technology can enhance production efficiency and product quality.
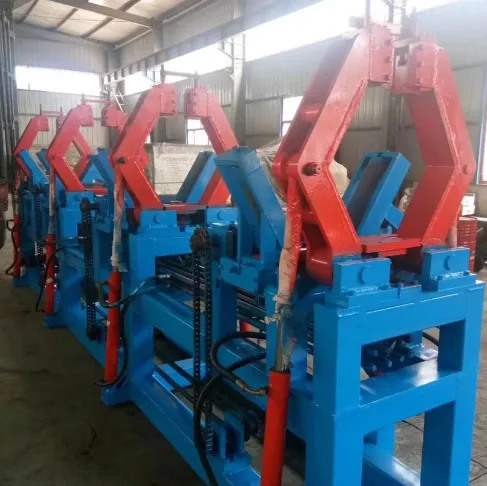
Roll forming is a continuous bending operation where a long strip of metal, typically coiled steel, passes through sets of rolls mounted on consecutive stands. Each set of rolls performs only an incremental part of the bend until the desired cross-section profile is obtained.
For aluminum profiles, roll forming is a preferred method due to aluminum’s malleability and strength-to-weight ratio. I have observed companies maximize their operational efficiency by integrating state-of-the-art computer numerical control (CNC) systems in their roll forming equipment. This addition ensures precise control over the forming process, allowing for complex profiles to be manufactured with minimal tolerances, significantly reducing material waste.
From an expertise standpoint, the selection of aluminum as a material is strategic. Aluminum's intrinsic properties, such as corrosion resistance, thermal conductivity, and recyclability, make it a superior choice for sustainable development goals. By choosing roll-formed aluminum profiles, manufacturers are not only endorsing environmentally friendly practices but also ensuring the longevity and durability of their products. In my role as a consultant, I consistently recommend roll-forming processes to clients seeking to improve the mechanical properties of their aluminum products while achieving a high surface finish.
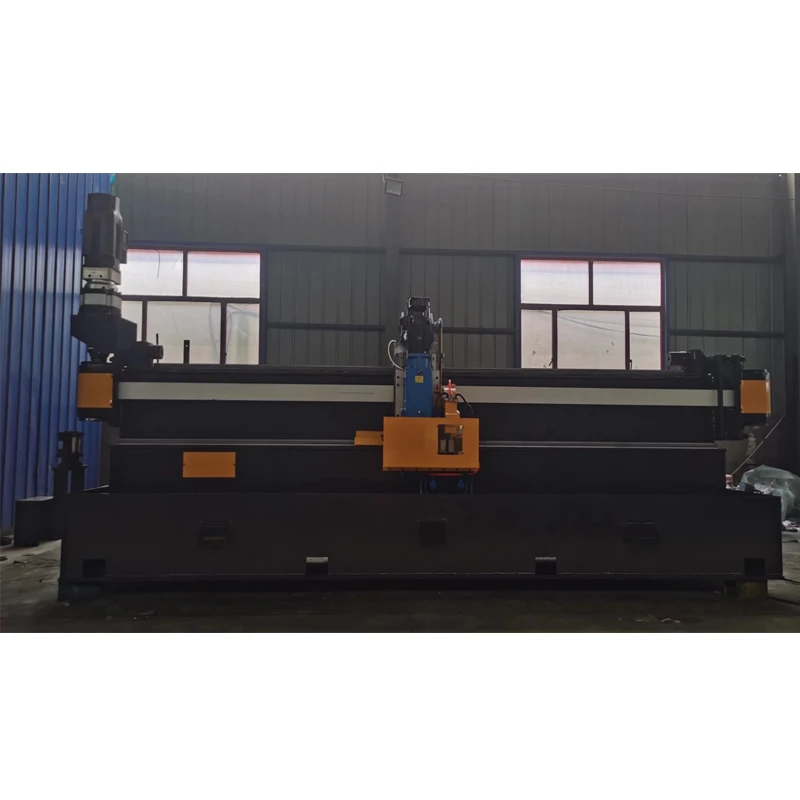
aluminum profile roll forming
Authoritativeness in the domain of aluminum profile roll forming is driven by a deep understanding of both the material science and the engineering processes involved. An authoritative approach demands a comprehensive mastery of roll forming equipment, tool designs, and process parameters. This involves meticulous calibration of equipment to adapt to the unique properties of aluminum, customizations that vary depending on the specific end-use requirements. For instance, optimizing roll pressure and rotation speed is crucial for maintaining the integrity of the aluminum microstructure, preventing issues such as micro-cracking or unwanted surface roughness.
The cornerstone of trustworthiness in aluminum profile roll forming is stringent quality control protocols. Implementing advanced quality assurance methods such as in-line non-destructive testing (NDT) techniques and laser measurement systems during the roll forming process ensures that each aluminum profile meets the highest industry standards. These protocols are crucial for industries where regulatory compliance is mandatory, particularly in sectors like aerospace where component failures can have catastrophic consequences. My collaborations with leading industry players have always emphasized the importance of such quality measures, ensuring product reliability and customer satisfaction.
In conclusion, aluminum profile roll forming is an indispensable technique with profound implications for modern manufacturing industries. Its advantages are manifold, spanning from reduced environmental impact to heightened product performance. Through continuous innovation and meticulous quality assurance, companies can leverage roll forming to remain competitive. Insights from real-world applications and exhaustive research underline its value proposition, making it a pillar of not only current but future manufacturing endeavors. By embracing advancements in roll forming technology, businesses can confidently navigate the complex demands of today's market, ensuring sustained success and industry leadership.