Automatic pipe welding machines are reshaping the landscape of industrial fabrication with their unparalleled efficiency and precision. Their rising popularity is rooted not just in technological advancement but also in the tangible benefits they bring to various industries. For companies navigating the demands of modern manufacturing, understanding the profound impact of these machines is crucial.
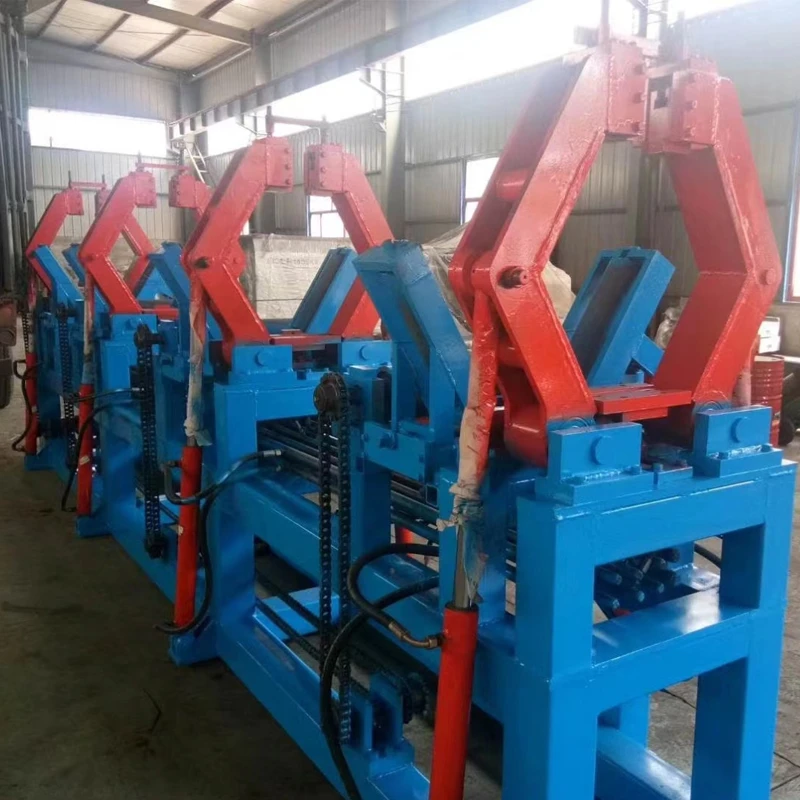
The essence of automatic pipe welding machines lies in their ability to deliver consistent and high-quality welds across different materials and thicknesses. This consistency is paramount for sectors where precision is non-negotiable, such as in the construction of pipelines for the oil and gas industry, or in the aerospace sector. By minimizing human error, these machines ensure weld integrity that meets stringent safety and regulatory standards.
Expertise in operating automatic pipe welding machines goes beyond mere button-pushing. It involves understanding the nuances of welding parameters such as speed, heat, and electrode positioning. Experienced operators are able to fine-tune these variables to adapt to different materials, ensuring optimal performance. Notably, training centers across the globe are increasingly focusing on imparting hands-on knowledge about these machines, thus enhancing the skill set of the workforce.
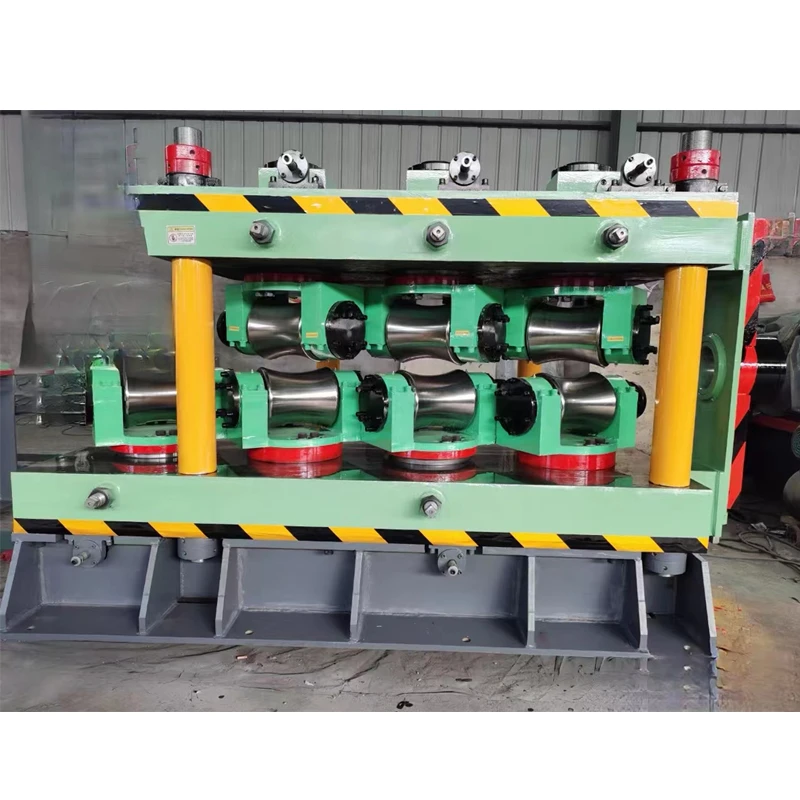
Trustworthiness and authoritativeness of these complex machines are affirmed by their adoption in critical industries. Esteemed companies in the energy sector, for instance, rely on automatic pipe welding units for their pivotal projects, recognizing the machines’ ability to handle large volumes of work with decreased downtime. The reduced risk of defects and rework translates to substantial cost savings and project reliability – an imperative in industries where time is quite literally money.
automatic pipe welding machine
Real-world experiences highlight the transformative impact of these machines. A large-scale manufacturing firm, after integrating automatic pipe welding machines into their processes, reported a 40% increase in production efficiency. Additionally, the reduction in weld defects dramatically cut quality control times and improved overall project timelines. This shift not only enhanced their operational capacity but also solidified their reputation for delivering high-standard, reliable products.
From an authoritative perspective, industry reports consistently showcase the advantages of automated welding solutions. A study found that industries employing these machines witnessed a reduction of more than 30% in operational costs, which is a testament to their efficiency and cost-effectiveness. Furthermore, these machines support sustainable practices by optimizing material usage and minimizing waste, aligning with global environmental standards.
In the evolving landscape of industrial manufacturing, automatic pipe welding machines stand as a testament to innovation and efficiency. Their contribution to streamlining operations, ensuring quality, and fostering a skilled workforce cannot be overstated. For businesses aiming to maintain a competitive edge, investing in these automated solutions is not just advisable, it is essential. This foresight ensures that companies not only meet current industry benchmarks but also set new standards in manufacturing excellence.