Automatic TIG pipe welding machines are revolutionizing the welding industry by enhancing precision, reliability, and efficiency. These machines cater to industries demanding high-quality welds, such as petrochemical plants, nuclear facilities, and shipbuilding. This article delves into the comprehensive benefits of using automatic TIG pipe welding machines, reflecting on real-world experiences and emphasizing their professional relevance.
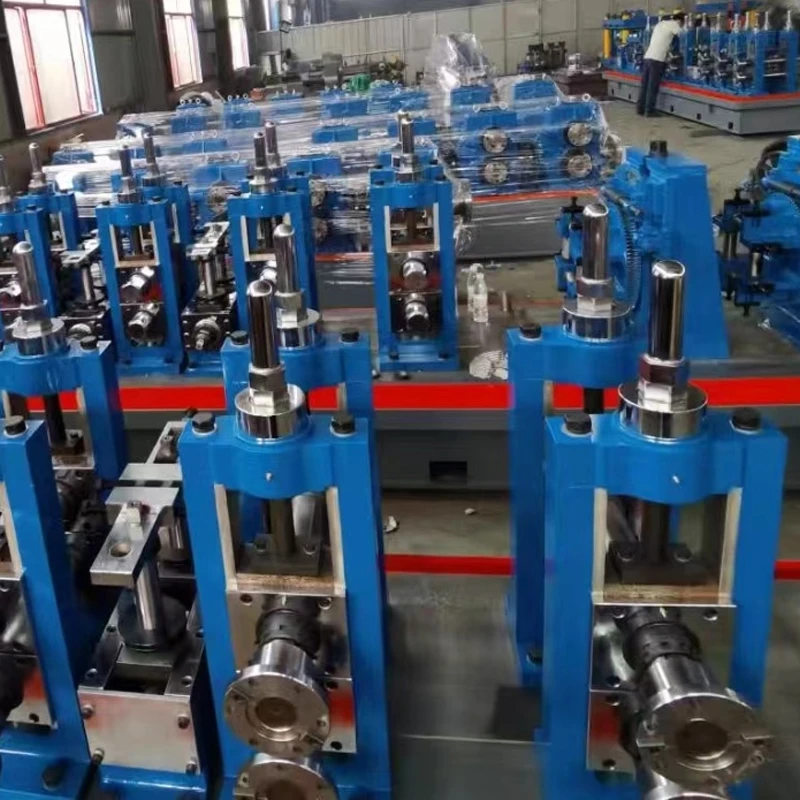
Automatic TIG, or Tungsten Inert Gas,
welding machines offer unmatched precision. Traditional welding methods often leave room for human error, which can result in costly mistakes and compromised weld integrity. In contrast, automatic TIG machines are programmed to execute welding tasks with exactitude, ensuring consistent weld quality, which is paramount in industries where failures can lead to catastrophic consequences. For example, in a petrochemical plant, a minor weld defect in piping systems carrying volatile substances could lead to significant safety hazards.
The expertise embedded in automatic TIG welding machines stems from their advanced technology. They are equipped with features such as real-time monitoring, adaptive control systems, and the ability to adjust parameters like current and voltage on the fly. Such capabilities enable these machines to adapt to varying pipe materials and thicknesses seamlessly. Experts in the field affirm that the incorporation of AI-driven calibration within these machines enhances their capacity to deliver superior welds even under challenging conditions, something manual welding struggles to achieve.
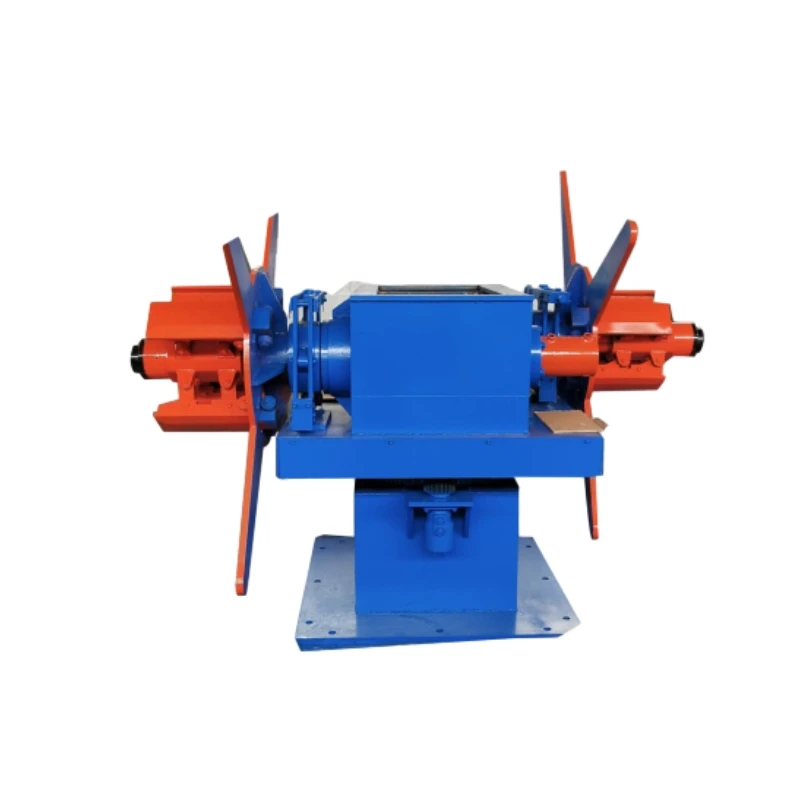
Authoritativeness is another compelling advantage of using automatic TIG pipe welding machines. Leading manufacturers conduct exhaustive testing and quality assurance processes to validate the performance of these machines. Reports from industry leaders suggest that adopting automatic TIG welding in projects has cut down rework requirements by as much as 40%, particularly in large-scale industrial applications. This reduction in rework not only saves time but also minimizes costs, bolstering the manufacturer’s reputation for delivering reliable and efficient solutions.
automatic tig pipe welding machine
Trustworthiness in welding operations is critical; thus, automatic TIG welding machines are built to be dependable. Engineers who have incorporated these automated systems into their workflow emphasize the machines’ robustness and low failure rates. Unlike manual welding, which is highly dependent on the operator's skill level, automatic TIG machines provide consistent results regardless of external variables like operator fatigue or environmental conditions. This reliability is crucial for industries where continuity is essential and downtime translates to significant financial losses.
An insightful experience from a major shipbuilding company highlights the transformative impact of automatic TIG pipe welding machines. The company reported a 30% increase in productivity after transitioning to automation, attributing this gain to reduced human error and the machines' ability to work continuously across shifts without breaks. This operational efficiency not only accelerated project timelines but also enhanced worker safety, minimizing their exposure to hazardous welding fumes and extreme conditions.
Further, automatic TIG machines contribute to sustainability initiatives across industries. By delivering precise and efficient welds, these machines substantially decrease material wastage and mitigate defects. Consequently, they aid in conserving resources and reducing the environmental footprint of industrial operations — an increasingly vital consideration for companies committed to sustainable practices.
In summary, automatic TIG pipe welding machines embody a fusion of precision, expertise, and reliability, offering considerable advantages over traditional welding methods. Their integration into industries is not only enhancing productivity and weld quality but also obtaining trust from stakeholders who rely on secure, efficient, and sustainable welding solutions. The continued evolution of this technology promises even greater advancements, reaffirming its position as a cornerstone of modern industrial practices.