Bend, punch, and shear are fundamental components of metal fabrication, critical in the creation of precise and durable metal products. Mastery of these techniques not only highlights expertise but also establishes authority and trustworthiness in the field.
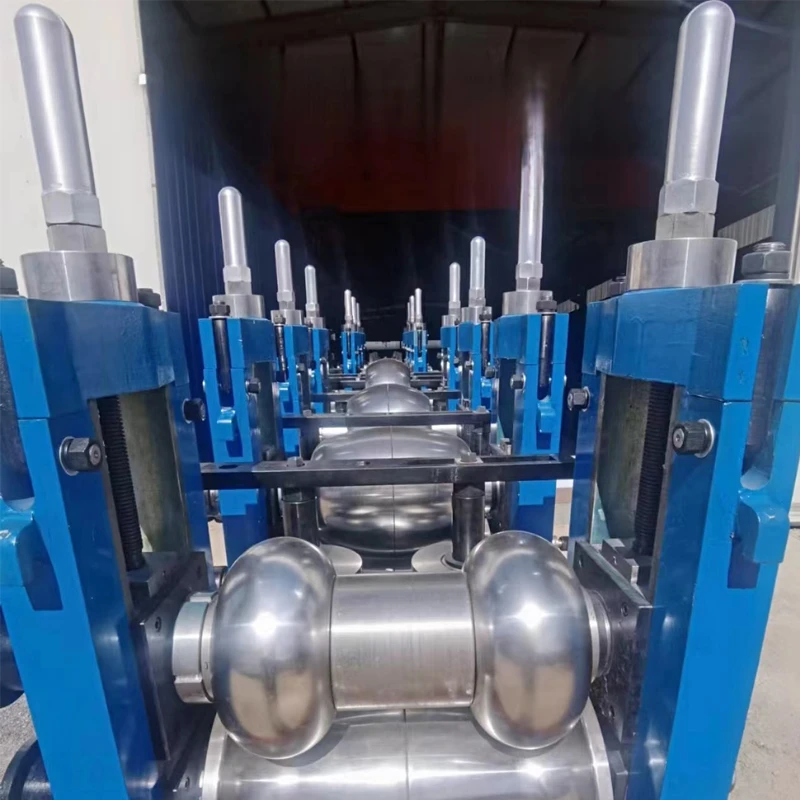
Bending is the art of deforming metal into a desired angle or shape without breaking it. This process demands skill, as improper technique can result in structural weakness or failure. Professionals use different types of presses and dies, such as V-bending or U-bending, to achieve specific angles and radii. In-depth understanding of material properties is vital. Variations in thickness, alloy composition, and temperature affect the malleability of the metal. For instance, cold bending is widely used for its precision and low cost, but it requires expertise to prevent work hardening. By tailoring each bend to suit material characteristics, professionals ensure optimal performance and durability in applications ranging from automotive components to architectural frameworks.
Punching involves creating holes or indentations in metal using a punch press. Precision is essential for this process, as any deviation can compromise the part's functionality. Experienced fabricators select the appropriate punch and die combination, considering factors like force distribution and tool wear. Advanced CNC technology enhances precision but requires skilled operators to set programming parameters accurately. Trustworthy professionals regularly maintain their machinery, ensuring consistent quality output and minimal downtime. They also adhere to safety standards, recognizing the high-pressure environment of punching operations. Expertise in punching allows businesses to produce complex patterns and perforations efficiently, essential for fields such as aerospace engineering and electronics manufacturing.
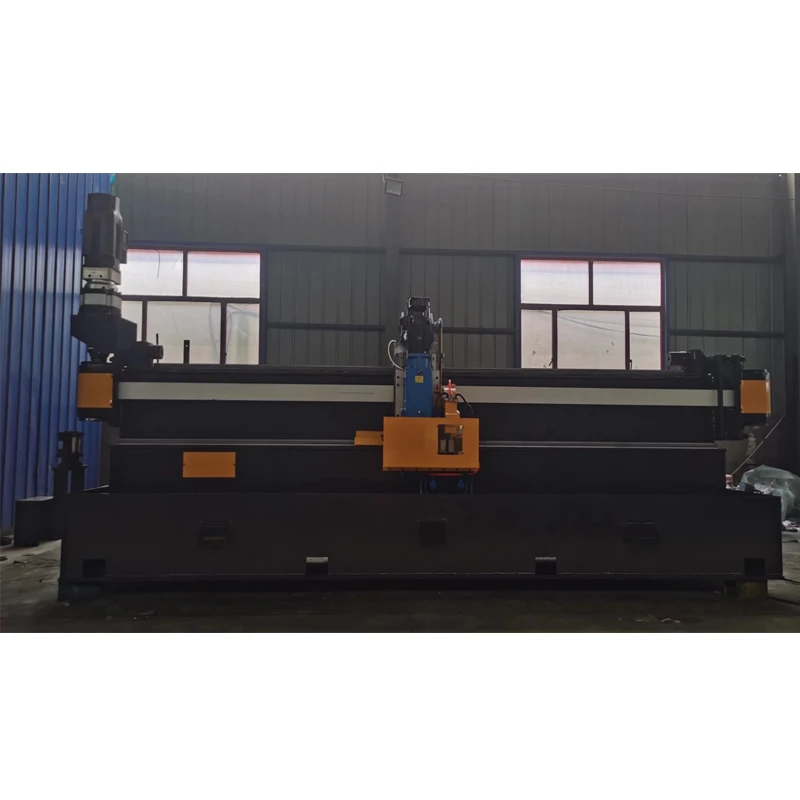
bend punch shear
Shearing is a cutting process that changes the length of metal without affecting its breadth. This method relies on powerful shear blades that slice through metal like scissors. Precision in shearing is paramount, as it directly influences subsequent fabrication processes. With expertise, a fabricator understands how to adjust blade clearance and rake angle to suit specific materials, reducing burr formation and edge distortion. Shearing's efficiency is unmatched in large-scale productions, making it a go-to technique for producing sheets and plates quickly and accurately. An authoritative approach to shearing involves leveraging automation alongside manual insights, ensuring seamless transitions between batch productions of varied specifications.
The combination of bending,
punching, and shearing forms the cornerstone of reliable metal fabrication. Each process requires a commitment to quality and detail, from material selection to final inspection. Professionals in the field dedicate themselves to continuous learning, adapting to evolving technologies and materials to maintain their competitive edge. This dedication fosters trust among clients, as they can rely on these experts to deliver products that meet stringent industry standards.
In summary, the prowess of utilizing bend, punch, and shear in metal fabrication epitomizes the balance of expertise, authority, and trustworthiness. Mastery of these skills drives innovation in product design and manufacturing, setting industry benchmarks. As these processes blend traditional craftsmanship with modern technology, they empower businesses to meet diverse market demands, solidifying their status as leaders in metal fabrication.