Unraveling The Efficiency of Coil Straightener Machines Transforming Metal Fabrication
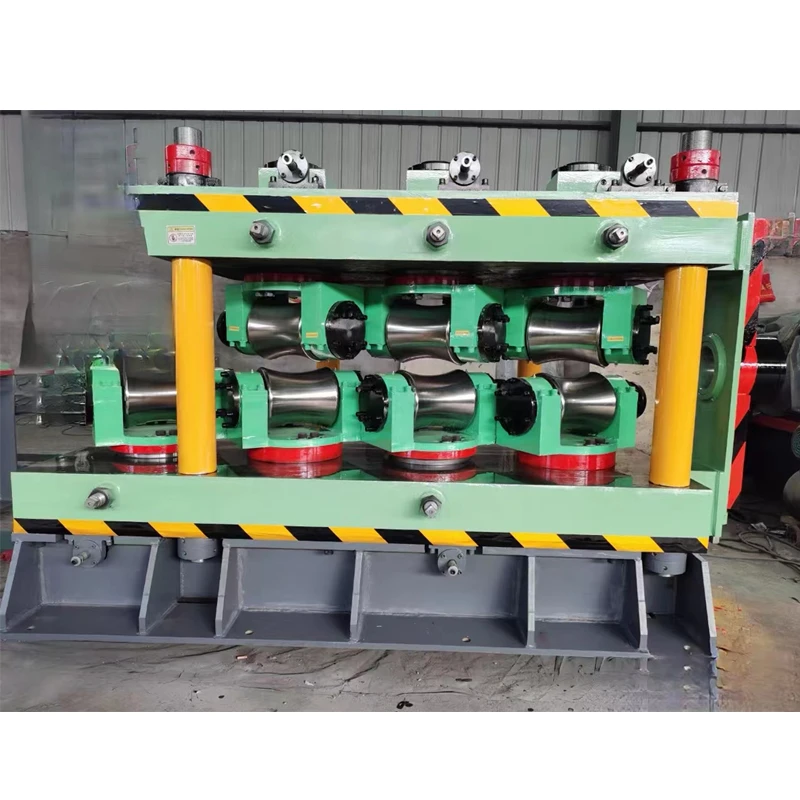
In the dynamic world of metal fabrication, precision and efficiency are non-negotiable standards. Among the myriad tools and machinery employed to achieve these high standards, the coil straightener machine stands out as a cornerstone of modern metal processing operations. This sophisticated device transforms coiled metal into flat, manageable sheets or strips, serving a critical role in the supply chain of countless industries.
Metallurgy meets mechanical engineering in the design of coil straighteners, where the emphasis lies on creating perfectly straightened materials. At the heart of these machines is a series of hardened steel rollers, carefully arranged to apply controlled pressure to the coiled material. As the metal passes through, these rollers unbend the natural coil memory of the metal, resulting in smoothly flattened sheets.
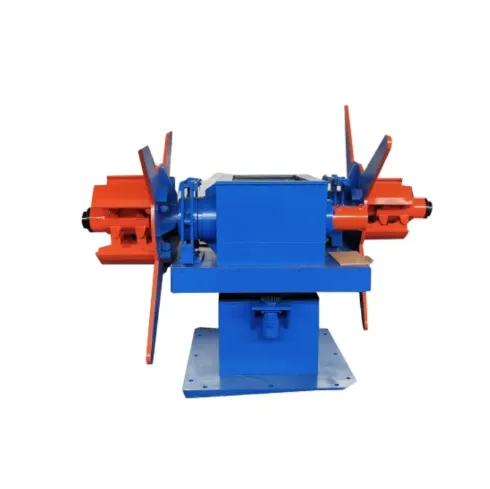
Incorporating coil straighteners is synonymous with boosting operational productivity. They are not only designed for precision but also engineered for speed. In environments where vast quantities of metal need conversion from coil to flat sheet, these machines deliver impressive throughput. Enhanced versions can handle varying material thicknesses, accommodating both thin aluminum strips and thicker steel slabs with equal finesse.
Expertise in handling coil straighteners can significantly reduce waste material and operational costs. Continuous material handling without frequent jams or misfeeds ensures minimal downtime—leading to more efficient metal processing. Seasoned operators know the value of regular maintenance checks, which maintain the alignment and condition of the rollers, preserving the machine's longevity and consistency in output quality.
Today's coil straightener machines also epitomize technological advancement. Integration with automated systems promises smarter manufacturing spaces, where machines communicate seamlessly to relay data, increasing accuracy and reducing human error. Operators often have access to real-time metrics, allowing them to adjust machine settings on-the-fly to match the demands of diverse production lines, supporting adaptive manufacturing strategies.
coil straightener machine
Professionals in the field who gain expertise in the setup, operation, and maintenance of coil straightener machines find themselves invaluable. As guardians of the metal’s journey from coil to finished product, they ensure that the straightening process enhances rather than detracts from the metal's quality. Their deep understanding of metal properties—temperature thresholds, tensile strength variations, and memory effects—underpins the optimal operation of these machines.
Moreover, the coil straightener machine's authority extends beyond efficiency into quality enhancement. By minimizing internal stress within the metal, manufacturers see fewer defects and increased durability in their final products. This is particularly vital in sectors like automotive or aerospace, where component integrity is directly tied to safety and performance.
However, the efficacy of coil straighteners is not merely in the machinery itself but in the ecosystem supporting it. Trustworthy vendors provide not only the hardware but also comprehensive support through training, servicing, and parts replacements. Trusted brands offer machines with proven track records, designed to withstand rugged operational environments, and backed by industry-standard certifications.
The integration of coil straightener machines curates a competitive advantage for manufacturers. Companies that leverage cutting-edge straightening technology unlock potential for innovation, catering to more challenging customer requirements, and venturing into niche markets that demand precision-engineered metal components. This positions them as leaders in quality assurance and production reliability.
In summary, the coil straightener machine is more than a mechanical element of metal processing; it’s a testament to engineering sophistication and a vital asset in achieving operational excellence. Its blend of precision engineering, advanced technology, and robust design underpins the transformative process of turning raw coiled metal into precision-ready materials, meriting its esteemed place in the realm of modern manufacturing. With ongoing innovations and improvements, these machines are poised to redefine standards in metal fabrication, continually lifting the benchmarks for quality, efficiency, and sustainability.