Navigating the landscape of coil straightening cutting machines requires a nuanced understanding of both the machinery's intricate mechanics and industry best practices. These machines, pivotal in the metal manufacturing sector, transform coiled metal into precise, flat sheets that meet exact specifications. Any manufacturing unit dealing with large-scale metal processing can vastly benefit from the efficiency and capabilities of a high-quality coil straightening cutting machine.
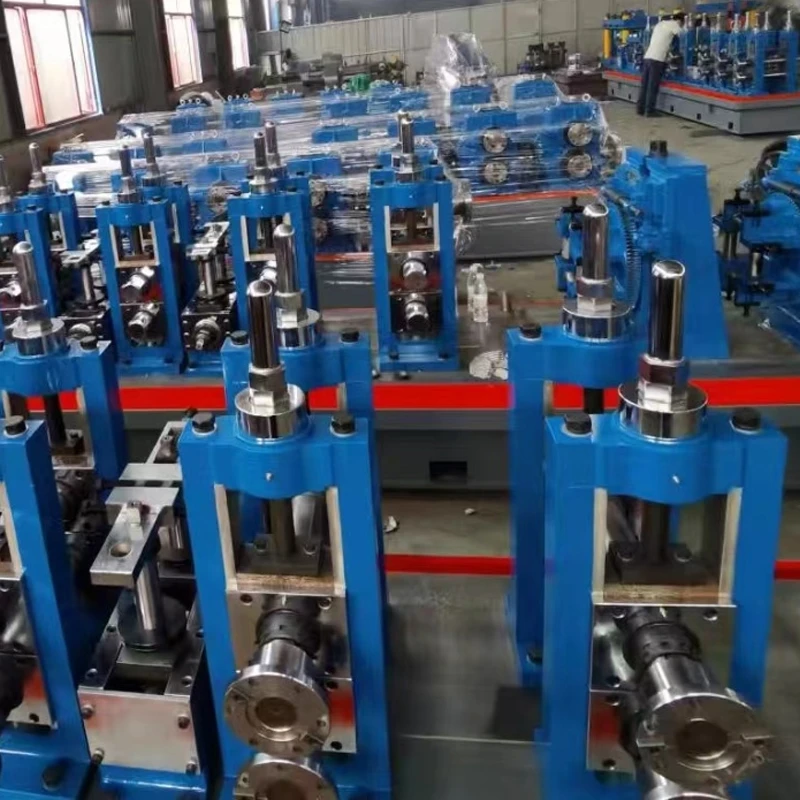
The primary components of these machines consist of uncoilers, straighteners, feeding rollers,
and cutting devices. Each plays a crucial role in the seamless conversion of raw material into usable formats. The uncoiler first unwinds the coiled material, which is then passed through the straightener. This component corrects any inherent imperfections and ensures the metal is suitably flat before reaching the feeding rollers. Once aligned correctly, the material is then accurately measured and subsequently cut by the cutting device.
Key to optimizing the performance of these machines is the quality of the straightening mechanism. By applying precision engineering, top-tier coil straightening machines utilize advanced alignment systems that minimize stress on the metal. These systems typically include sophisticated roller arrangements and pressure adjustment capabilities, allowing operators to adapt settings based on the metal thickness and type. Thus, ensuring optimal flatness without compromising the material's structural integrity.
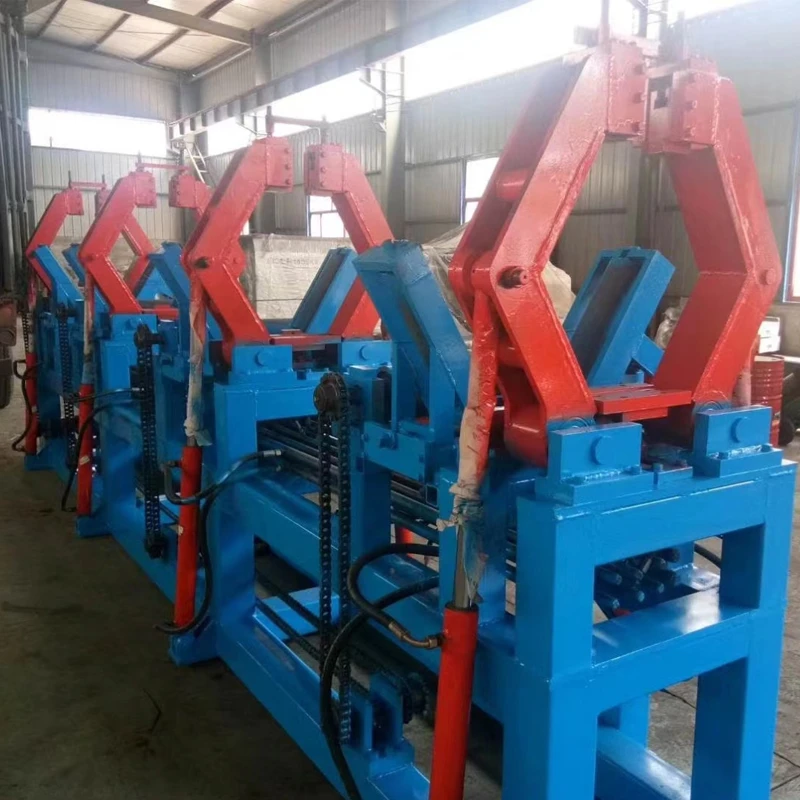
Choosing the appropriate coil straightening cutting machine boils down to understanding specific operational demands. For instance, the gauge of metal being processed, the required cut lengths, and production volume are vital considerations. Additionally, equipment featuring user-friendly interfaces and automated control systems offers enhanced efficiency and reduces the margin for human error, thus enhancing overall productivity.
Integration of Industry 4.0 technology into these machines has revolutionized traditional operations. Smart sensors and IoT capabilities allow real-time monitoring and data analysis, equipping manufacturers with insights that drive improvements in production processes. Predictive maintenance, facilitated through IoT integration, minimizes downtime and extends the machine's lifecycle by alerting operators before potential malfunctions occur.
coil straightening cutting machine
Safety remains paramount in the use of coil straightening cutting machines. Modern machines incorporate advanced safety features such as emergency stop buttons, overload protection, and guards around moving parts. Regular operator training and adherence to safety protocols further fortify the secure operation of these machines, ensuring a safe working environment alongside high efficiency.
To maintain and improve the trustworthiness of these machines, manufacturers should prioritize robust after-sales support and easy access to spare parts. Establishing a network of skilled technicians for periodic maintenance and repairs can prevent expensive downtimes, thus maintaining production schedules and boosting overall return on investment.
Companies specializing in manufacturing these machines must stay abreast of industry regulations and standards. Compliance with international safety standards and certifications not only reflects a company’s commitment to quality but also adds a layer of authenticity and trust among potential clients.
In conclusion, investing in a coil straightening cutting machine involves considering numerous factors—precision engineering, compatibility with existing systems, integration of advanced technologies, and adherence to safety standards. By evaluating these criteria meticulously, businesses can significantly enhance their production capabilities, paving the way for greater efficiency and profitability in a competitive market. These machines not only symbolize engineering prowess but also serve as a testament to a facility’s commitment to maintaining quality and innovation in metal processing operations.