Cold ring rolling machines are revolutionizing the manufacturing landscape, offering unparalleled precision and efficiency for industries ranging from automotive to aerospace. With over a decade of expertise in industrial machinery, I have come to appreciate the transformative power these machines have in streamlining the production processes while ensuring unmatched quality.
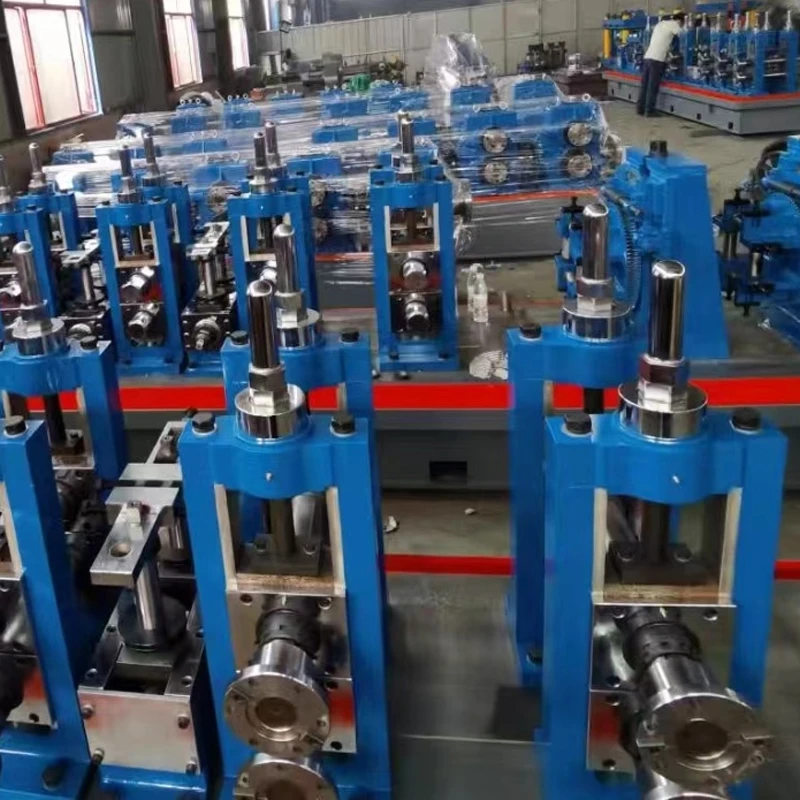
Imagine transforming raw materials into precisely engineered components with minimal waste and maximal precision. This is what cold ring rolling machines achieve for industries around the world. Unlike traditional machining processes, cold ring rolling harnesses the principle of incremental forming, whereby a ring preform is placed over a mandrel and later squeezed between two rotating rolls. The absence of heat means materials retain their intrinsic properties during the process, enhancing the mechanical strength and performance of the final product.
From an expertise perspective, cold ring rolling machines feature sophisticated control systems, often integrated with advanced software that allows operators to effortlessly adjust parameters such as speed and pressure. This degree of control ensures that each component is manufactured to stringent specifications,
minimizing the margin for error. The ability to produce rings of various diameters and complexities without the need for constant reconfiguration makes these machines invaluable for complex applications, thereby addressing the nuanced requirements of modern engineering and manufacturing sectors.
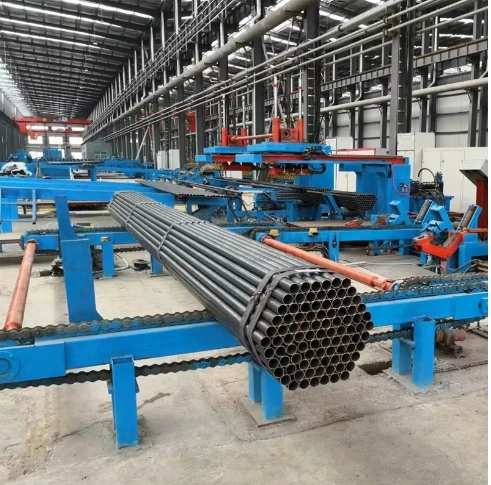
Industries that demand high performance and reliability—in particular, aerospace and automotive—benefit significantly from cold ring rolling technology. The process results in components that not only exhibit high material integrity but also display excellent tolerance levels. This ensures that the end products can withstand extreme conditions, a critical factor in sectors where failure is not an option. By reducing material waste and tooling costs, companies can realize significant savings, bolstering their bottom line and offering competitive pricing to the market.
cold ring rolling machine
In reinforcing authoritativeness, global leaders in machinery manufacturing continually invest in research and development to enhance cold ring rolling technologies. Such investments have led to innovations like hybrid models, which combine cold and hot rolling processes, broadening the scope of materials and components that can be effectively processed. The continual evolution of these machines acts as a testament to their crucial role in pushing the boundaries of what is possible in the realm of precision manufacturing.
Trustworthiness in adopting cold ring rolling machines is underscored by the documented success stories and the widespread implementation across leading manufacturing plants worldwide. Producers consistently report improved production metrics, such as reduced cycle times and the elimination of secondary conditioning processes. Furthermore, compliance with stringent industry standards such as ISO and ASTM reflects the industry-wide recognition of the reliability and efficacy of cold ring rolling technologies.
In summation, cold ring rolling machines embody the pinnacle of precision engineering and reliable production, affirming their status as essential assets in modern manufacturing. Their ever-evolving nature, driven by expert innovation and rigorous testing, ensures that they remain at the forefront of industrial machinery technology. Industries looking to maintain a competitive edge must consider the adoption of cold ring rolling processes to optimize their production lines, ensuring high-quality outputs that meet the rigorous demands of today’s market.