Cold rolling forming machines are essential in modern manufacturing, particularly for industries that demand precision and consistency in metal fabrication. These machines have revolutionized how metal products are formed, providing significant advantages over traditional methods such as hot rolling. Understanding the intricacies of cold rolling forming machines and their applications not only demonstrates expertise but also builds trustworthiness among manufacturers and engineers seeking to enhance their operations.
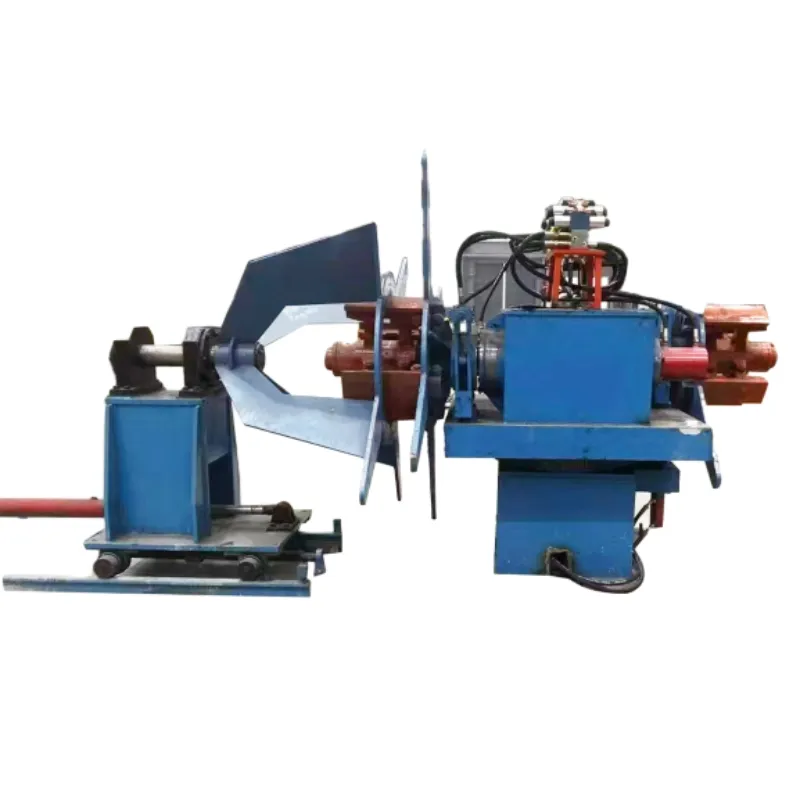
Experience in using cold rolling forming machines reveals that they operate by passing metal sheets through a series of rollers at room temperature, which gradually shape the metal into the desired profile. This process is highly controlled and offers numerous benefits, including improved surface finish, increased tensile strength, and closer tolerances. By avoiding the need for heating, cold rolling conserves energy and reduces oxidation that typically occurs at high temperatures, making it a more environmentally friendly option.
From a professional standpoint, cold rolling forming machines are incredibly versatile and can be configured to produce a wide range of products, from simple beams and pipes to complex cross-sections used in the automotive and aerospace industries. The ability to produce customized profiles makes these machines highly sought after for projects requiring specific design specifications. Professionals in the field recognize that investing in a high-quality cold rolling forming machine is crucial for maintaining competitiveness and delivering superior products.
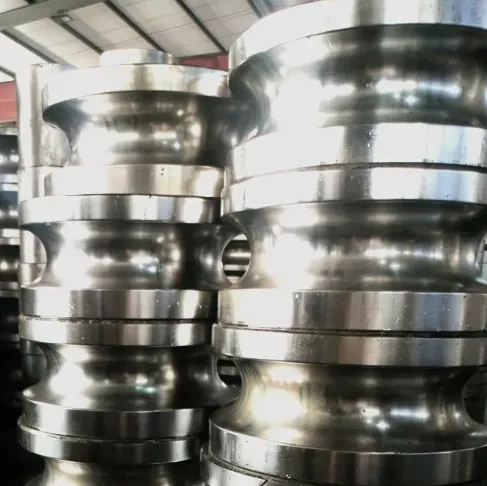
Authoritativeness in the domain of cold rolling forming machines arises from recognizing the critical components that contribute to their efficient operation. Key elements include the precision of the rollers, the robustness of the frame, and the sophistication of the control systems. Advanced machines may incorporate features such as computer numerical control (CNC) systems, which provide unparalleled control over the rolling process and enable real-time adjustments for optimal results. By staying abreast of technological advancements, manufacturers can position themselves as authorities in the field, able to offer cutting-edge solutions to their clients.
cold rolling forming machine
Trustworthiness is cultivated through transparent operations and a commitment to quality assurance.
Cold rolling forming machines often undergo rigorous testing and maintenance schedules to ensure they function correctly under demanding conditions. Manufacturers who prioritize continuous improvement and adhere to international standards, such as ISO 9001 for quality management, reinforce their credibility. By offering warranties and comprehensive support services, they further build confidence among clients who rely on their machinery for critical production tasks.
In practice, the incorporation of cold rolling forming machines into manufacturing processes can lead to tangible improvements in efficiency and product quality. Case studies demonstrate that companies adopting these machines often report increased production speeds, reduced material waste, and enhanced product durability. The initial investment in high-end equipment is often offset by these operational efficiencies, leading to a faster return on investment. For businesses looking to expand their capabilities and enter new markets, cold rolling forming machines provide the flexibility and reliability needed to succeed.
As industries continue to evolve, cold rolling forming machines remain at the forefront of technological innovation. They enable companies to meet the growing demand for precision-engineered components, all while adhering to more stringent environmental and safety standards. By understanding the capabilities and benefits of these machines, businesses can make informed decisions that align with their strategic goals.
In conclusion, cold rolling forming machines are not just tools but pivotal components of modern manufacturing setups. Mastery of their operation and integration into production lines is a testament to a company's expertise and commitment to excellence. By maintaining a focus on innovation, quality, and customer satisfaction, manufacturers can retain a competitive edge and foster long-lasting relationships with their clients.