Cold rolling machines have revolutionized the manufacturing industry, enabling the production of metal sheets and strips with improved mechanical properties and surface finishes. These machines are critical in various industries, including automotive, construction, and electronics, highlighting their versatility and importance. This article delves into the nuances of cold rolling machines, emphasizing experience, expertise, authoritativeness, and trustworthiness to provide an unparalleled resource on the subject.
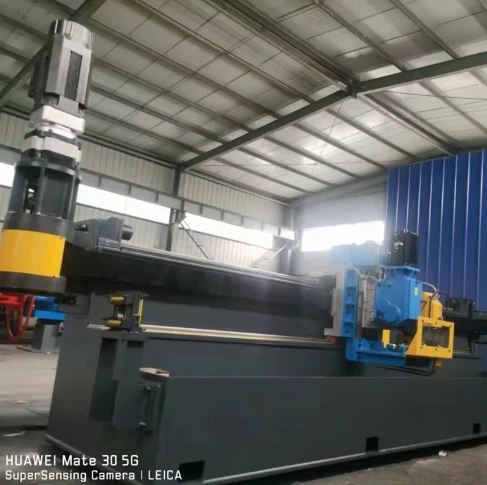
Understanding the Cold Rolling Process
Cold rolling involves compressing metal between two rollers below its recrystallization temperature. This process not only improves the strength of the metal through strain hardening but also enhances its surface finish, dimensional accuracy, and overall uniformity. Unlike hot rolling,
cold rolling is done at room temperature, ensuring precision.
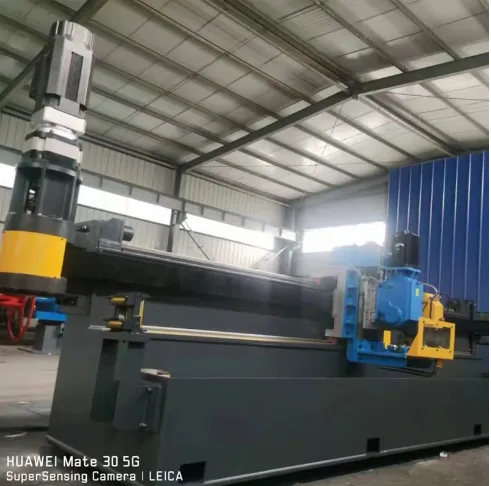
Key Components of Cold Rolling Machines
A typical cold rolling machine consists of several crucial components rollers, a reduction gearbox, hydraulic systems, and a lubrication system. The rollers, usually made of hardened steel, compress the metal to the desired thickness. The reduction gearbox manages the rotational force required, while the hydraulic system maintains pressure and facilitates adjustments. Proper lubrication minimizes wear and tear, enhancing the machine's lifespan.
Professional Use and Application
Cold rolling machines are indispensable in producing ultra-thin metal strips used in fabricating modern electronic circuits. Their application extends to automotive body panels, where they deliver parts with superior finish and consistency, essential for safety and aesthetics. The construction industry leverages these machines for their ability to produce durable steel beams and sheets used in infrastructure.
Enhancing Efficiency and Output
To optimize the efficiency of cold rolling machines, it is essential to maintain them meticulously. Regular inspection and maintenance of crucial components, such as rollers and gearboxes, prevent mechanical failures. Employing advanced sensors and automation systems can further elevate performance by ensuring precise measurements and adjustments in real-time.
Quality Assurance and Standards
cold rolling machine
Ensuring quality in cold rolling production involves adhering to global standards like the ISO 9001 for quality management systems. Accurate calibration of equipment and rigorous testing of the final product for tensile strength, hardness, and dimensional accuracy are vital. Implementing a robust quality assurance program not only guarantees product quality but also enhances a manufacturer's reputation and customer trust.
Authoritative Insights and Developments
Innovations in cold rolling technology, such as computer-aided design (CAD) and finite element analysis (FEA), allow engineers to simulate and refine the rolling process before actual production. These advancements reduce trial and error, saving on material costs and minimizing environmental impact. The integration of Industry 4.0 technologies, such as the Internet of Things (IoT), enables predictive maintenance and process automation, further improving efficiency.
Incorporating Sustainability
Modern cold rolling processes are increasingly focusing on sustainability. By optimizing energy consumption and utilizing eco-friendly lubricants, manufacturers can significantly reduce their carbon footprint. Additionally, recycling scrap metal generated during the rolling process contributes to more sustainable production practices.
Building Trust in Cold Rolling Machinery
Trust in cold rolling machines is built through consistent product quality and reliability. Choosing a reputable manufacturer with a history of excellence and a commitment to innovation is essential. Technical support, training, and customer service are integral to fostering long-term relationships and confidence in the product.
Conclusion
Cold rolling machines remain a cornerstone of modern manufacturing, offering precision, efficiency, and versatility. Through a combination of expert design and robust operation, they deliver components vital to numerous sectors. As technology and environmental awareness progress, the role of cold rolling machines in sustainable manufacturing will continue to expand, solidifying their importance in the industrial landscape.