In the evolving landscape of manufacturing, cold rolling mill machines stand as a cornerstone of innovation, efficiency, and productivity. These machines have revolutionized the metalworking industry by providing a method to produce a smoother and more precise finish. While various methods are used in metal processing, the cold rolling technique offers distinct advantages that reinforce its position in modern fabrication shops and industries.
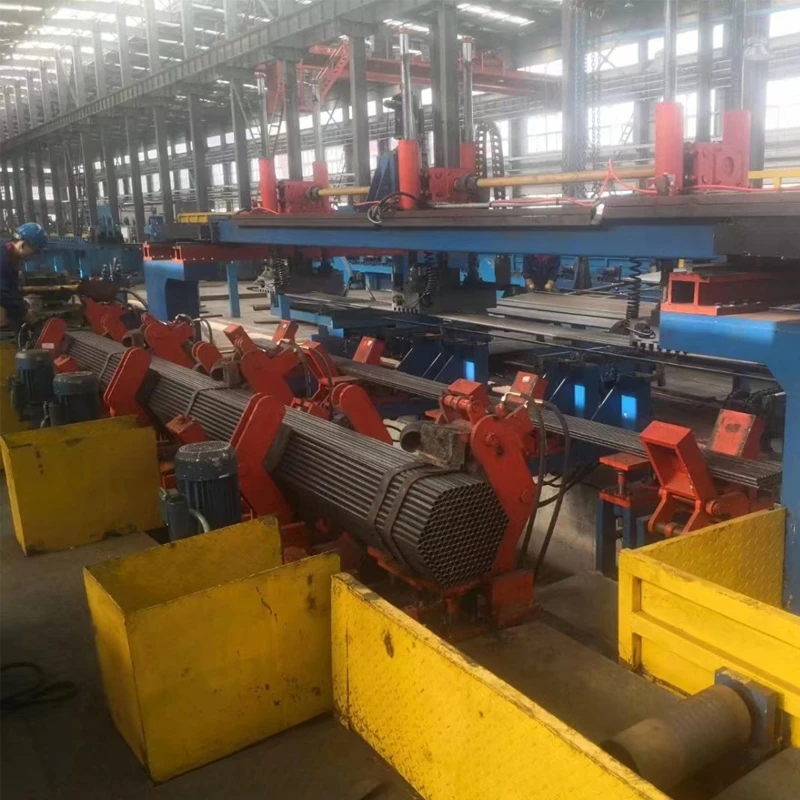
Cold rolling mill machines are integral in the production of steel strips, sheets, and plates. They operate at room temperature, as opposed to hot rolling, and utilize compressive forces to shape the metal. This process not only enhances the material's surface finish but also improves the mechanical properties of the metal, such as hardness and tensile strength. Industries from automotive to construction depend heavily on the robust outputs of cold rolling, making these machines indispensable.
One significant benefit of the cold rolling process is the superior tolerance and surface quality it achieves. When metal is processed at room temperature, dimensional accuracy is enhanced, and thus, products require less machining and processing, resulting in cost savings for companies. Precision parts in industries such as aerospace and electronics rely on these fine tolerances and exceptional finishes that cold rolling mill machines provide.
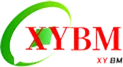
Furthermore, the technological advancements in cold rolling mill machines have led to great strides in efficiency and sustainability. Modern machines incorporate cutting-edge technologies such as automated controls and IoT integration, which increase operational efficiency and reduce the need for human intervention. This automation not only minimizes error rates but also optimizes energy consumption, aligning with global sustainability goals. Moreover, compact and innovative designs mean modern cold rolling mills consume less floor space, a crucial factor for manufacturers looking to maximize their production environments.
cold rolling mill machine
Expert operators of cold rolling mill machines know the significance of maintaining the equipment's calibration and condition. Regular maintenance ensures the longevity of the machines and the quality of the metal produced. Expertise in the operational protocols of these machines provides a competitive advantage to manufacturing facilities, enabling them to deliver high-quality products consistently. For this reason, continuous training and investment in skilled personnel are crucial.
Historically, the development of cold rolling mill technology has been marked by significant milestones, spearheaded by authoritative industry leaders dedicated to advancing metal processing capabilities. Innovators in this field have continuously pushed boundaries, from basic single-stand mills to complex multi-stand setups, enabling today’s manufacturers to meet diverse and stringent market demands.
Trustworthiness and reliability are pillars of the reputation of manufacturers and suppliers of cold rolling mill machines. Companies that invest in quality engineering and robust construction gain a stronger foothold in the market, offering assurances of machine longevity and consistent performance. Customer feedback and endorsements also play pivotal roles in bolstering a company’s reputation, highlighting the importance of post-sale support and service.
In conclusion, cold rolling mill machines are vital to producing the precision, quality, and efficiency demanded by numerous industrial sectors. As technology progresses, the capabilities and functionalities of these machines expand, creating more opportunities for industries to innovate and thrive. By understanding the full potential of cold rolling mill machines, businesses can leverage these advanced technologies to optimize their manufacturing processes, ultimately leading to enhanced products and improved bottom lines.