The world of manufacturing frequently revolves around the efficiency and precision of machines that handle raw materials. Decoilers and feeders are pivotal components in this domain, playing a crucial role in the seamless processing of metal coils, wires, and other rolled materials. These machines are indispensable for industries where accuracy and speed determine the success of production lines.
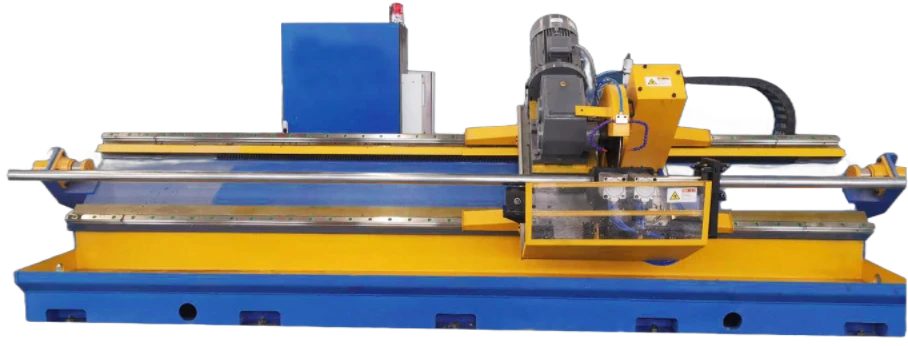
Decoilers and feeders are engineered to handle heavy loads with precision. The decoiler's primary function is to unroll metal coils systematically, preventing mishandling that could lead to costly downtime or material wastage. Its design often includes an adjustable braking system that controls the tension of the coil, ensuring a consistent unwind rate that matches the operational speed of the feeder.
Feeders, on the other hand, take the unraveled material from the decoiler and push it precisely into various processing machines—be it stamping, cutting, or welding equipment. The synchronization between these two machines is vital, as any misalignment or malfunction can lead to inaccuracies that compromise the final product's quality. Modern feeders are equipped with sophisticated automation systems, including PLC controls and servo motors, allowing for real-time adjustments and increased throughput.
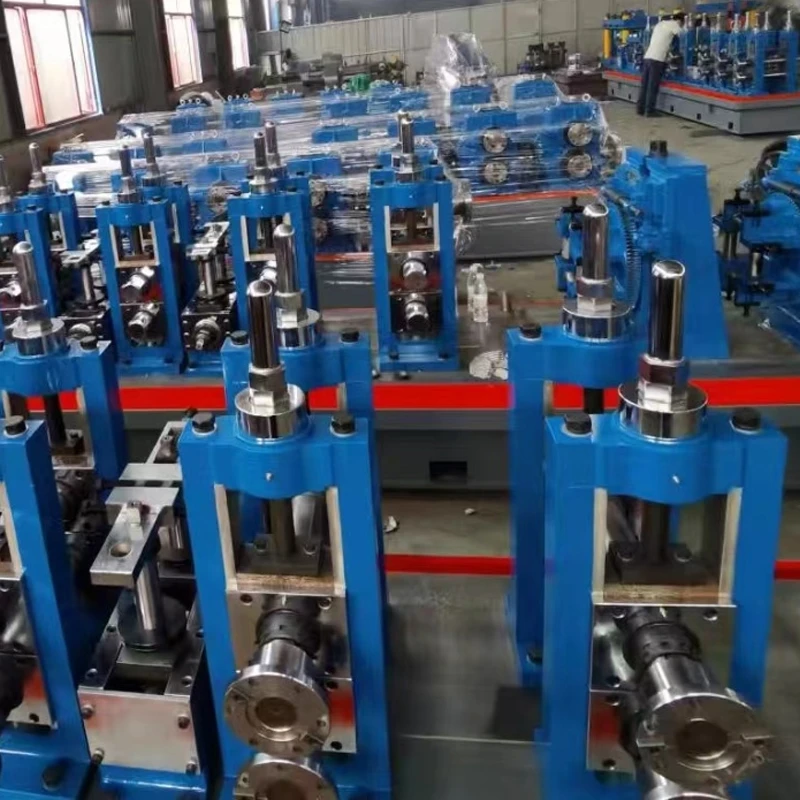
Investing in high-quality decoilers and feeders brings significant advantages. Firstly, they minimize material wastage and increase production efficiency by reducing manual handling and the associated errors. Secondly, these machines support a wide range of material types and thicknesses, offering flexibility across different projects. Finally, by ensuring precise material feeding, they uphold the quality and integrity of the manufacturing process, directly influencing product reliability and customer satisfaction.
For those in the industry seeking to elevate their production capabilities, understanding the expertise required to operate decoilers and feeders is paramount. Operators need thorough training in machine settings, maintenance routines, and troubleshooting techniques. Regular inspections and timely maintenance prevent wear and tear, reducing the frequency of mechanical failures and extending the machine’s lifespan.
decoilers and feeders
Output can only be as good as the inputs, highlighting the importance of source materials. Selecting quality coils tailored to the decoiler and feeder specifications can streamline the process, further enhancing operational efficacy. This precision in sourcing and operation ensures production lines remain uninterrupted, maximizing potential output while maintaining top-notch standards.
In terms of authoritativeness, manufacturers and suppliers of decoilers and feeders often provide comprehensive documentation and support. Prospective buyers should seek machines that come with detailed instruction manuals and access to expert advice, which help facilitate smooth installation and operation. Engaging with suppliers that offer ongoing technical support can also be a game-changer, providing peace of mind and added security.
Trustworthiness in the use of decoilers and feeders is built on consistent performance and safety. Industry-compliant machines adhere to rigorous safety standards, minimizing risks to operators and reducing liability concerns. Safety features, like emergency stop mechanisms and protective housings, are not optional extras but essential components of a trustworthy manufacturing environment.
The landscape of industrial production is changing rapidly, with technological advancements pushing the capabilities of decoilers and feeders further. Innovations such as IoT integration and predictive maintenance are entering the realm, promising even greater efficiency and minimizing unscheduled downtime. By continually upgrading equipment and training personnel, manufacturers can stay ahead of the curve and maintain a competitive edge in their field.
In conclusion, the utilization of advanced decoilers and feeders is more than a necessity—it's an investment in quality, efficiency, and success. By embracing these machines' full potential, manufacturers can markedly improve their production processes, ensuring consistent output and a satisfied customer base. This level of investment is crucial for maintaining industry leadership and pushing the boundaries of what is possible in modern manufacturing.